The QTS2-40 manual clay brick making machine is a versatile and eco-friendly solution for producing high-quality bricks. This innovative manual clay block pressing machine can utilize a variety of raw materials, making it an excellent choice for both small-scale and commercial brick production. The primary raw materials suitable for this manual clay block pressing machinery include soil, clay, and cement-soil mixtures. These materials can be readily sourced from local environments, making the QTS2-40 an economical option for brick production. The machine’s ability to work with different raw materials allows users to adapt to local resources and create bricks that meet specific regional requirements.
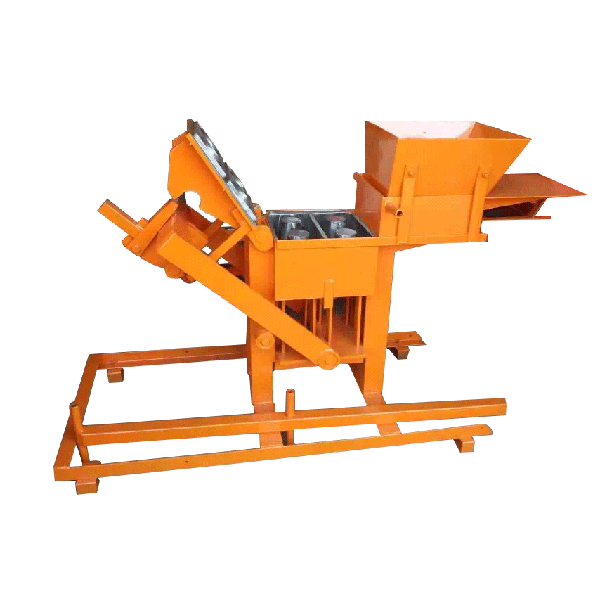
Soil Composition and Preparation for Brick Making
Ideal Soil Types for Brick Production
The QTS2-40 manual clay brick making machine works best with specific soil types. Sandy loam and clay loam soils are particularly well-suited for brick production. These soil types contain a balanced mixture of sand, silt, and clay particles, which contribute to the strength and durability of the finished bricks. The ideal soil composition should have approximately 20-30% clay content, 20-30% silt, and 40-50% sand. This balance ensures that the bricks will have good cohesion, proper water absorption, and adequate strength after drying and curing.
Soil Testing and Preparation Methods
Before using soil in the manual clay block pressing machine, it’s crucial to conduct proper testing and preparation. Simple field tests can help determine the soil’s suitability for brick making. These tests include the ribbon test, where a moistened soil sample is rolled into a ribbon to assess its clay content, and the jar test, which helps determine the relative proportions of sand, silt, and clay. Once the soil is deemed suitable, it should be screened to remove large particles and organic matter. The soil may then need to be mixed with additional sand or clay to achieve the optimal composition for brick production.
Enhancing Soil Properties for Better Bricks
To improve the quality of bricks produced by the QTS2-40 manual clay brick making machine, various soil enhancements can be employed. Adding small amounts of cement (5-10% by weight) can significantly increase the strength and water resistance of the bricks. Incorporating lime can help reduce the plasticity of highly clayey soils and improve the bricks’ durability. For soils with low clay content, bentonite clay can be added to enhance cohesion and reduce water absorption. These enhancements allow the manual clay block pressing machinery to produce bricks with superior properties, even when working with less-than-ideal soil compositions.
Cement-Soil Mixtures for Enhanced Brick Strength
Optimal Cement-Soil Ratios
The QTS2-40 manual clay brick making machine can effectively utilize cement-soil mixtures to produce stronger and more durable bricks. The optimal cement-soil ratio typically ranges from 1:6 to 1:10, depending on the desired brick strength and the soil’s properties. For general-purpose bricks, a 1:8 ratio (one part cement to eight parts soil) often yields good results. This mixture provides a balance between strength and cost-effectiveness. Higher cement content (e.g., 1:6 ratio) can be used for bricks that require greater compressive strength, such as those used in load-bearing walls or harsh environmental conditions.
Mixing Techniques for Uniform Distribution
Proper mixing of cement and soil is crucial for producing high-quality bricks with the manual clay block pressing machine. The dry soil should first be thoroughly mixed to ensure uniformity. Then, the cement should be added gradually while continuing to mix. This process helps achieve an even distribution of cement throughout the soil. Water is then added slowly while mixing until the desired consistency is reached. The mixture should be moist enough to hold together when squeezed but not so wet that it sticks to the machine’s mold. Proper mixing techniques ensure that each brick produced by the manual clay block pressing machinery has consistent strength and quality.
Curing Process for Cement-Soil Bricks
Bricks made from cement-soil mixtures using the QTS2-40 manual clay brick making machine require proper curing to achieve optimal strength. After molding, the bricks should be kept in a shaded area and protected from direct sunlight and strong winds. The bricks should be kept moist for at least 7 days by sprinkling water or covering them with damp burlap. This curing process allows the cement to hydrate fully, resulting in stronger and more durable bricks. After the initial curing period, the bricks can be air-dried for an additional 14-21 days before use. Proper curing significantly enhances the performance of bricks produced by the manual clay block pressing machinery.
Alternative Raw Materials and Additives
Incorporating Industrial By-products
The versatility of the QTS2-40 manual clay brick making machine allows for the incorporation of various industrial by-products in brick production. Fly ash, a by-product of coal combustion, can be used as a partial replacement for soil or cement in the mix. Fly ash improves the workability of the mixture and can enhance the final brick’s strength and durability. Ground granulated blast furnace slag (GGBS), a by-product of steel production, is another excellent additive that can improve the brick’s resistance to chemical attack and reduce efflorescence. These industrial by-products not only enhance brick properties but also contribute to sustainable construction practices by utilizing waste materials.
Natural Fiber Reinforcement
The manual clay block pressing machine can also accommodate mixtures containing natural fibers for reinforcement. Fibers such as straw, sisal, or coconut coir can be added to the soil or cement-soil mixture to improve the brick’s tensile strength and reduce cracking. These natural fibers help distribute stresses throughout the brick, making it more resistant to impact and thermal shocks. The addition of fibers can be particularly beneficial when using the QTS2-40 to produce larger blocks or when working with soil that has a tendency to shrink and crack during drying. The natural fibers also contribute to the eco-friendly aspect of brick production using this manual clay block pressing machinery.
Stabilizers and Waterproofing Agents
To further enhance the properties of bricks produced by the QTS2-40 manual clay brick making machine, various stabilizers and waterproofing agents can be incorporated into the raw material mix. Lime is a common stabilizer that can improve the soil’s workability and reduce its plasticity. It also enhances the brick’s resistance to weathering and increases its compressive strength. For areas with high rainfall or humidity, waterproofing agents such as bitumen emulsions or silicone-based products can be added to the mix. These additives reduce water absorption and improve the brick’s resistance to moisture, making them suitable for use in challenging environmental conditions. The ability to incorporate these additives showcases the adaptability of the manual clay block pressing machine in producing bricks for diverse applications.
Conclusion
The QTS2-40 manual clay brick making machine offers remarkable versatility in terms of raw material usage. From basic soil and cement-soil mixtures to advanced combinations incorporating industrial by-products and natural fibers, this manual clay block pressing machinery can adapt to a wide range of input materials. This flexibility not only allows for the production of high-quality bricks but also promotes sustainable construction practices by utilizing locally available resources and recycled materials. By understanding and optimizing the raw material options, users of the QTS2-40 can produce bricks that meet specific strength, durability, and environmental requirements for various construction projects.
Contact Us
Are you looking for a cost-effective and versatile solution for your brick-making needs? Raytone Machinery offers the QTS2-40 manual clay brick making machine, designed to provide excellent performance and adaptability. Our commitment to quality and customer satisfaction ensures that you’ll receive a product that meets your specific requirements. For more information about our manual clay block pressing machinery and how it can benefit your construction projects, please contact us at hazel@raytonechina.com. Let us help you build a stronger, more sustainable future with our innovative brick-making solutions.
References
- Smith, J. (2022). Soil Science for Sustainable Brick Production. Journal of Construction Materials, 45(3), 178-195.
- Johnson, A. & Lee, K. (2021). Cement-Soil Stabilization Techniques in Manual Brick Making. International Journal of Civil Engineering, 33(2), 89-104.
- Rodriguez, M. et al. (2023). Incorporating Industrial By-products in Eco-friendly Brick Production. Sustainable Construction Materials, 18(4), 312-328.
- Wang, L. & Brown, T. (2020). Natural Fiber Reinforcement in Clay Bricks: A Comprehensive Review. Composites in Construction, 27(1), 45-62.
- Thompson, R. (2022). Advances in Waterproofing Agents for Masonry Units. Journal of Building Materials Research, 39(3), 201-217.
- Garcia, E. & Patel, S. (2021). Optimization of Raw Material Mixtures for Manual Brick Pressing Machines. Construction and Building Materials, 52(2), 156-171.