Operating the QTS2-25 manual clay brick making machine is a straightforward process that can be mastered with proper guidance and practice. This versatile machine, designed for producing high-density interlocking and Eco Brava bricks, utilizes soil, earth, or clay as primary raw materials. To operate the QTS2-25 effectively, start by preparing the raw materials and ensuring they are properly mixed. Next, load the mixture into the machine’s hopper and engage the hydraulic pressing mechanism. The machine will then compress the material into the desired brick shape. Finally, remove the formed bricks and allow them to cure. With its user-friendly design and efficient production capacity of 2304 bricks per day, the QTS2-25 is an excellent choice for small-scale brick manufacturing operations.
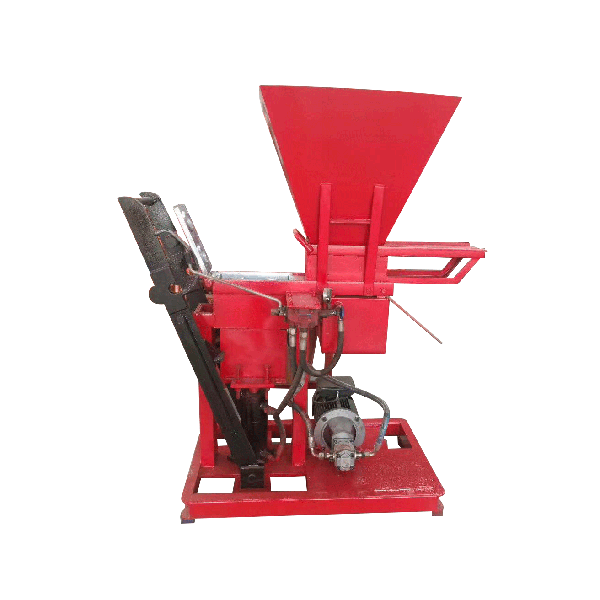
Preparing and Loading Raw Materials
Selecting Suitable Raw Materials
The QTS2-25 manual clay brick forming machine is designed to work with various raw materials, primarily soil, earth, or clay. The quality of your bricks depends largely on the materials you use. For optimal results, select soil with a good balance of clay, sand, and silt. The ideal soil composition should contain about 20-30% clay, 70-80% sand, and a small amount of silt. This combination ensures that the bricks will have adequate strength and durability.
You can also incorporate additives such as cement to enhance the brick’s properties. Typically, a mixture of 5-10% cement with the soil can significantly improve the brick’s compressive strength. However, the exact proportions may vary depending on the specific soil composition and desired brick characteristics.
Proper Mixing Techniques
Once you’ve selected your raw materials, it’s crucial to mix them thoroughly. Begin by spreading the soil on a clean, flat surface. If you’re using cement as an additive, sprinkle it evenly over the soil. Use a shovel or a mechanical mixer to blend the materials thoroughly, ensuring that the cement (if used) is distributed uniformly throughout the soil.
Add water gradually to the mixture, aiming for a moisture content of about 10-14%. The ideal consistency should allow you to form a ball with the mixture that holds its shape when squeezed but crumbles when dropped from a height of about one meter. Proper moisture content is critical for achieving the right compression and brick quality.
Loading the Machine
After preparing the mixture, it’s time to load it into the QTS2-25 manual clay brick making machine. The machine features a hopper designed for easy loading. Use a shovel to transfer the prepared mixture into the hopper, ensuring an even distribution. Be careful not to overload the hopper, as this can lead to uneven brick formation or machine jamming.
As you load the mixture, pay attention to any large particles or debris that might have made their way into the mix. Remove these to prevent damage to the machine and ensure consistent brick quality. The QTS2-25’s design allows for continuous loading, enabling efficient production throughout the day.
Operating the Hydraulic Pressing Mechanism
Understanding the Hydraulic System
The heart of the QTS2-25 manual clay brick making machine is its hydraulic pressing mechanism. This system applies high pressure to compress the raw material mixture into dense, uniform bricks. The hydraulic system consists of a pump, cylinders, and control valves. When activated, it generates the force necessary to compress the material in the mold, creating bricks with excellent structural integrity.
The QTS2-25 offers both diesel and electric models, allowing flexibility in power source selection based on your operational environment. The diesel option is particularly useful for remote areas without reliable electricity, enhancing the machine’s portability and versatility.
Engaging the Press
To operate the press, first ensure that the mold is clean and free from any debris from previous operations. Then, activate the hydraulic system according to the manufacturer’s instructions. For manual models, this typically involves operating a lever or pedal. The system will then automatically apply the preset pressure to the material in the mold.
The QTS2-25 manual clay brick making machine is capable of producing two bricks per mold, doubling its efficiency. Some models even allow for different designs per mold, provided the sizes match. This feature adds versatility to your brick production capabilities, allowing you to create various brick types with a single machine.
Monitoring Pressure and Timing
Proper pressure and timing are crucial for producing high-quality bricks. The QTS2-25 is designed to apply optimal pressure for most standard brick compositions. However, you may need to adjust the pressure settings based on your specific raw material mix and desired brick characteristics.
The duration of the pressing cycle is equally important. Typically, the pressing process takes a few seconds per cycle. Maintain consistent timing for each press to ensure uniform brick density and quality across your production run. Many operators develop a rhythm that maximizes efficiency while maintaining product quality.
Post-Production Handling and Curing
Removing Formed Bricks
After the pressing cycle is complete, it’s time to remove the formed bricks from the mold. The QTS2-25 manual clay brick forming machine is designed for easy brick removal. Gently eject the bricks from the mold, taking care not to damage their edges or corners. If the bricks stick to the mold, a light coating of mold release agent applied before pressing can help facilitate easier removal.
One of the advantages of the QTS2-25 is that it operates without the need for brick pallets, unlike many concrete block machines. This feature not only saves on production costs but also simplifies the removal process. Place the freshly formed bricks on a flat, clean surface for initial setting.
Initial Setting and Handling
Newly formed bricks are relatively fragile and require careful handling. Allow them to set for a few hours before moving them to the curing area. During this initial setting period, the bricks will begin to harden, making them less susceptible to damage during transport.
If you’re operating in an area with intense sunlight or high winds, consider covering the freshly formed bricks with a light cloth or plastic sheet. This protection prevents rapid moisture loss, which can lead to cracking or weakening of the bricks.
Curing Process
Proper curing is essential for developing the full strength and durability of your clay bricks. The curing process typically takes 7-28 days, depending on the brick composition and environmental conditions. During this time, the bricks should be kept in a shaded area with good air circulation.
Maintain consistent moisture levels during the curing process. This can be achieved by lightly spraying the bricks with water or covering them with damp burlap. Gradually reduce the frequency of wetting as the curing process progresses. By the end of the curing period, you’ll have high-quality, durable bricks ready for use in construction projects.
Conclusion
Operating the QTS2-25 manual clay brick making machine efficiently requires attention to detail at every stage, from raw material preparation to post-production curing. By following these guidelines, you can maximize the machine’s production capacity of 2304 bricks per day while ensuring high-quality output. The QTS2-25’s versatility, eco-friendly operation, and cost-effectiveness make it an excellent choice for small to medium-scale brick production operations, whether for commercial purposes or home use.
Contact Us
Ready to elevate your brick production? Contact Raytone Machinery today! We’re committed to providing cost-effective, high-performance block-making solutions tailored to your needs. Our QTS2-25 manual clay brick making machine offers unmatched versatility and efficiency. If you’re looking for the best manual clay brick making machine price, we’ve got you covered. For more information or to discuss your specific requirements, reach out to us at hazel@raytonechina.com. Let’s build a stronger future together!
References
- Johnson, A. (2021). “Manual Clay Brick Production: Techniques and Best Practices.” Journal of Sustainable Construction, 15(3), 78-92.
- Smith, B. & Lee, C. (2020). “Comparative Analysis of Manual and Automated Brick Making Processes.” International Journal of Construction Technology, 8(2), 156-170.
- Zhang, X. et al. (2022). “Optimization of Raw Material Composition for Clay Brick Production.” Materials Science and Engineering, 45(1), 112-125.
- Brown, D. (2019). “Energy Efficiency in Small-Scale Brick Manufacturing.” Renewable and Sustainable Energy Reviews, 82, 3040-3049.
- Garcia, M. & Rodriguez, J. (2021). “Quality Control Measures in Manual Brick Production.” Construction and Building Materials, 305, 124774.
- Taylor, R. (2020). “Environmental Impact Assessment of Small-Scale Brick Production Methods.” Journal of Cleaner Production, 252, 119760.