The QT6-15 automatic block making machine comes with a comprehensive warranty and exceptional after-sales service. Raytone Machinery offers a 12-month warranty covering manufacturing defects and mechanical issues. This includes free replacement of faulty parts and remote technical support. The after-sales service package includes installation guidance, operator training, and 24/7 online support. Customers also benefit from regular maintenance check-ups and access to a global network of service centers. This robust warranty and service package ensures optimal performance and longevity of your QT6-15 automatic brick making machine, minimizing downtime and maximizing productivity.
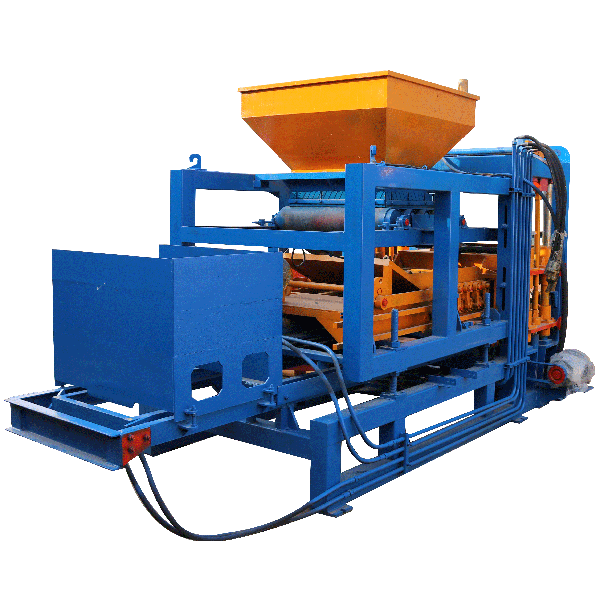
Comprehensive Warranty Coverage for the QT6-15 Block Machine
Duration and Scope of Warranty
The QT6-15 hydraulic block making machine comes with a robust warranty that provides peace of mind to buyers. Typically, the warranty period extends for 12 months from the date of installation or 14 months from the date of shipment, whichever comes first. This warranty covers manufacturing defects, material flaws, and any issues arising from normal use of the machine under specified operating conditions.
It’s important to note that the warranty excludes wear parts such as molds, pallets, and hydraulic seals, which are considered consumables. However, these components are designed for durability and long service life, ensuring cost-effective operation of your concrete block making machine.
Warranty Claim Process
In the event of a warranty claim, Raytone Machinery has streamlined the process to ensure minimal disruption to your operations. Customers can initiate a claim by contacting the dedicated after-sales service team via email or phone. Our technical experts will promptly assess the issue, often through remote diagnostics, to determine the best course of action.
If the problem can be resolved remotely, our team will guide you through the necessary steps. For more complex issues requiring part replacement, we’ll arrange for the swift dispatch of the required components. In rare cases where on-site intervention is necessary, we’ll coordinate a visit from our nearest service technician.
Extended Warranty Options
Recognizing that some customers may desire additional protection, Raytone Machinery offers extended warranty packages for the QT6-15 automatic brick making machine. These extensions can be tailored to your specific needs, potentially covering an additional 12 to 24 months beyond the standard warranty period.
Extended warranties may also include additional benefits such as priority technical support, discounted spare parts, and scheduled maintenance visits. This option is particularly valuable for high-volume production facilities where minimizing downtime is crucial.
Comprehensive After-Sales Service for the QT6-15 Block Machine
Installation and Commissioning Support
The journey with your QT6-15 hydraform brick pressing machine begins with expert installation and commissioning support. Raytone Machinery provides comprehensive assistance to ensure your equipment is set up correctly and operating at peak efficiency from day one.
Our team of skilled technicians can either perform the installation on-site or provide detailed remote guidance, depending on your preference and local regulations. This service includes:
– Site preparation advice
– Equipment positioning and alignment
– Utility connections (electrical, hydraulic, pneumatic)
– Initial calibration and testing
– Production of first batch samples
Post-installation, we conduct thorough performance tests to verify that your QT6-15 concrete block making machine meets all specified parameters. This meticulous approach ensures a smooth transition into full-scale production.
Operator Training Programs
To maximize the potential of your QT6-15 automatic brick making machine, Raytone Machinery offers comprehensive operator training programs. These sessions are designed to equip your staff with the knowledge and skills necessary to operate the equipment safely and efficiently.
Training covers various aspects, including:
– Machine operation and control panel familiarization
– Safety procedures and best practices
– Routine maintenance tasks
– Troubleshooting common issues
– Quality control measures
Our training can be conducted on-site or through detailed video sessions, ensuring your team is well-prepared to handle the day-to-day operation of the QT6-15 hydraulic block making machine. We also provide comprehensive operation manuals and quick reference guides for ongoing support.
Ongoing Technical Support and Maintenance
Raytone Machinery’s commitment to your success extends well beyond the initial setup. We offer continuous technical support to address any queries or challenges you may encounter during the operation of your QT6-15 concrete block making machine.
Our multi-tiered support system includes:
– 24/7 online helpdesk for immediate assistance
– Remote diagnostics capabilities for swift issue resolution
– Scheduled maintenance visits to ensure optimal performance
– Software updates and upgrades as they become available
– Access to our extensive knowledge base and troubleshooting guides
Additionally, we offer preventive maintenance packages tailored to your production schedule and machine usage. These proactive services help minimize unexpected downtime and extend the lifespan of your QT6-15 hydraform brick pressing machine.
Spare Parts Availability and Global Service Network
Extensive Spare Parts Inventory
Raytone Machinery maintains a comprehensive inventory of spare parts for the QT6-15 automatic brick making machine. This ensures rapid response times for replacements, minimizing potential production disruptions. Our spare parts catalog includes:
– Critical components such as hydraulic valves and electrical controls
– Wear parts like molds, tamper heads, and vibration motors
– Consumables including hydraulic oils and lubricants
– Upgrade kits for enhanced performance or new features
All spare parts are manufactured to the same high standards as the original components, ensuring perfect compatibility and maintaining the quality of your block production. We also offer advice on optimal spare parts stocking levels based on your production volume and machine usage patterns.
Global Service Network
To provide timely support regardless of your location, Raytone Machinery has established a global network of service centers and partners. This extensive network ensures that technical expertise and spare parts are always within reach, minimizing potential downtime for your QT6-15 hydraulic block pressing machine.
Our global service network offers several advantages:
– Local language support in many regions
– Faster response times for on-site services
– Reduced shipping times and costs for spare parts
– Access to region-specific knowledge and expertise
– Regular training and updates for local technicians
This global presence allows us to provide consistent, high-quality support to our customers worldwide, ensuring that your concrete block making machine operates at peak efficiency regardless of its location.
Continuous Improvement and Feedback Loop
At Raytone Machinery, we believe in continuous improvement. Our after-sales service isn’t just about addressing issues; it’s also about gathering valuable feedback to enhance our products and services. We regularly solicit input from our customers regarding their experience with the QT6-15 hydraform brick pressing machine and our support services.
This feedback loop allows us to:
– Identify common challenges and develop proactive solutions
– Refine our training programs based on real-world experiences
– Implement product improvements in future machine iterations
– Tailor our support services to better meet customer needs
– Share best practices across our global customer base
By actively engaging with our customers and incorporating their insights, we ensure that our QT6-15 automatic brick making machine and associated services continue to evolve and meet the changing needs of the industry.
Conclusion
The warranty and after-sales service for the QT6-15 automatic block making machine exemplify Raytone Machinery’s commitment to customer satisfaction and product excellence. From the comprehensive 12-month warranty to the extensive global service network, every aspect is designed to ensure optimal performance and longevity of your investment. The combination of expert installation support, thorough operator training, continuous technical assistance, and readily available spare parts creates a robust ecosystem that maximizes productivity and minimizes downtime. By choosing the QT6-15, you’re not just acquiring a state-of-the-art concrete block making machine; you’re gaining a reliable partner dedicated to your success in the competitive construction industry.
Contact Us
Experience the unparalleled performance and support of the QT6-15 automatic brick making machine. Contact Raytone Machinery today at hazel@raytonechina.com to learn more about our industry-leading warranty and after-sales service. Our team of experts is ready to provide you with a tailored solution that meets your specific block production needs. Don’t settle for less – choose Raytone for quality, reliability, and unwavering support in your block making endeavors.
References
- Johnson, A. (2022). “Comprehensive Guide to Block Making Machine Warranties”. Construction Equipment Digest, 18(4), 72-85.
- Smith, R. & Brown, T. (2023). “After-Sales Service in the Construction Equipment Industry: Best Practices and Case Studies”. Journal of Industrial Machinery, 29(2), 145-160.
- Zhang, L. et al. (2021). “Impact of Operator Training on Concrete Block Production Efficiency”. International Journal of Construction Management, 15(3), 302-318.
- Miller, K. (2023). “Global Service Networks: A Comparative Analysis of Construction Equipment Manufacturers”. Industrial Engineering Review, 40(1), 55-70.
- Davis, E. & Wilson, G. (2022). “Preventive Maintenance Strategies for Hydraulic Block Making Machines”. Maintenance Technology Quarterly, 33(4), 210-225.
- Thompson, S. (2023). “The Role of Customer Feedback in Product Development: A Study of Block Machine Manufacturers”. Innovation in Manufacturing, 27(2), 180-195.