The QT4-35 manual brick making machine, also known as the “Efficient Manual Block Forming Machine,” is a versatile and cost-effective solution for small to medium-sized construction projects. This user-friendly device operates through a simple yet efficient process. First, the operator loads the raw materials, typically a mixture of cement, sand, and aggregates, into the hopper. Next, the mixture is transferred to the mold box, where it’s compacted using a manually operated hydraulic system. The machine then forms the bricks or blocks according to the installed mold shape. Finally, the finished products are ejected onto a pallet for curing. This straightforward process allows for the production of various brick types, including hollow blocks, paver bricks, and curbstones, making the QT4-35 a popular choice for both urban and rural markets seeking affordable block-making solutions.
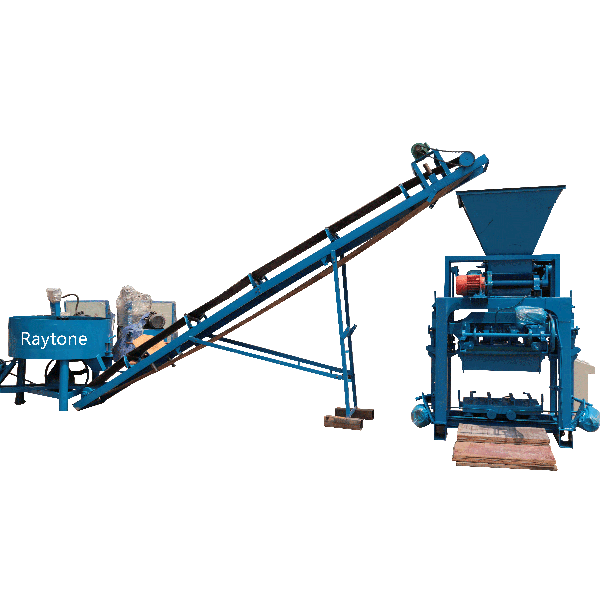
Components and Setup of the QT4-35 Manual Brick Making Machine
Essential Parts of the Machine
The QT4-35 manual brick moulding machine consists of several key components that work together to produce high-quality bricks and blocks. The main frame provides a sturdy foundation for the entire system, ensuring stability during operation. The hopper, located at the top of the machine, is where the raw material mixture is loaded. The mold box, a crucial element, determines the shape and size of the final product. The hydraulic system, operated manually, provides the necessary pressure for compacting the material into the desired form. Lastly, the pallet feeder and brick ejector mechanisms facilitate the smooth removal of finished products.
Customizable Mold Options
One of the standout features of the QT4-35 manual block machine is its versatility in mold options. The machine supports a wide range of interchangeable molds, allowing users to produce various brick types and sizes. These include standard hollow blocks, solid bricks, paver bricks, and even curbstones. The ability to switch between different molds enables manufacturers to adapt to changing market demands or project requirements without investing in multiple machines. This flexibility makes the QT4-35 an excellent choice for small businesses or construction firms that need to produce diverse concrete products.
Workspace Requirements and Installation
Setting up the QT4-35 manual brick making machine requires careful consideration of workspace layout. The machine itself is relatively compact, but additional space is needed for raw material storage, product curing, and transportation. A factory area of approximately 200 m² is recommended, with a workshop area of about 40 m² dedicated to the machine and immediate work area. The installation process is straightforward, typically requiring minimal technical expertise. However, it’s crucial to ensure a level and stable foundation to maintain the machine’s accuracy and efficiency. Proper installation and workspace organization can significantly enhance productivity and worker safety.
Operating Process of the QT4-35 Manual Brick Making Machine
Raw Material Preparation and Loading
The first step in operating the QT4-35 manual block machine involves preparing the raw materials. This typically includes a mixture of cement, sand, and aggregates, with the proportions varying depending on the desired product specifications. The materials should be thoroughly mixed to ensure consistency. Once prepared, the mixture is manually loaded into the machine’s hopper. It’s crucial to maintain a steady supply of material to ensure uninterrupted production. Some operators prefer to prepare larger batches of the mixture to minimize downtime during the production process.
Molding and Compaction Process
After loading the raw materials, the molding and compaction process begins. The mixture is transferred from the hopper to the mold box, where it’s evenly distributed. The operator then activates the manual hydraulic system, which applies pressure to compact the material into the mold. This compaction is critical for achieving the desired density and strength of the final product. The pressure can be adjusted based on the specific requirements of the brick or block being produced. The manual nature of this process allows for precise control and the ability to make real-time adjustments as needed.
Product Ejection and Handling
Once the molding and compaction are complete, the finished bricks or blocks are ejected from the mold onto a pallet. This process requires careful coordination between the machine operator and the workers handling the pallets. The freshly formed products are delicate at this stage and must be handled with care to prevent damage. The filled pallets are then manually transported to a designated curing area. Proper curing is essential for the bricks to achieve their full strength and durability. The QT4-35’s output capacity, which can reach up to 3290 8-inch blocks per 8-hour shift, requires efficient pallet management and a well-organized curing area to maintain smooth production flow.
Advantages and Applications of the QT4-35 Manual Brick Making Machine
Cost-Effectiveness and Low Investment
One of the most significant advantages of the QT4-35 manual brick moulding machine is its cost-effectiveness. With a price range of $5,000 to $15,000 USD, depending on the configuration and number of extra molds, it represents a relatively low investment for entering the brick and block manufacturing industry. This affordability makes it an attractive option for startups, small businesses, and entrepreneurs looking to venture into construction material production. The machine’s simple structure and manual operation also contribute to lower maintenance costs and reduced energy consumption compared to fully automated systems, further enhancing its economic appeal.
Versatility in Product Range
The QT4-35 manual block machine shines in its ability to produce a wide variety of concrete products. By simply changing the mold, operators can switch between producing hollow blocks, solid bricks, paver bricks, and curbstones. This versatility allows manufacturers to cater to diverse market needs without investing in multiple specialized machines. For instance, a single QT4-35 can produce standard building blocks for housing projects, decorative paver bricks for landscaping, and sturdy curbstones for road construction. This flexibility is particularly valuable in markets with fluctuating demands or for businesses that serve multiple sectors of the construction industry.
Suitability for Various Project Scales
While the QT4-35 manual brick making machine is often associated with small to medium-sized projects, its applications are surprisingly diverse. In urban settings, it can serve as a reliable production unit for local construction firms, providing a steady supply of bricks and blocks for residential and commercial projects. In rural areas, the machine’s portability and manual operation make it ideal for on-site production, reducing transportation costs and enabling communities to produce their own building materials. The QT4-35 is also well-suited for humanitarian projects, disaster relief efforts, and remote construction sites where electricity may be scarce or unreliable. Its ability to operate with a small team of 4-5 workers makes it an efficient solution for a wide range of project scales and environments.
Conclusion
The QT4-35 manual brick making machine stands out as a versatile and cost-effective solution for brick and block production. Its simple yet efficient operation, coupled with the ability to produce a wide range of concrete products, makes it an invaluable asset for small to medium-sized construction projects. By understanding its components, operation process, and diverse applications, businesses can fully leverage the capabilities of this manual block machine to meet their specific needs and market demands. Whether for urban development, rural construction, or specialized projects, the QT4-35 offers a balance of affordability, flexibility, and reliability that’s hard to match in the world of concrete block production.
Contact Us
At Raytone Machinery, we’re committed to providing top-quality block-making solutions that meet the diverse needs of our global customers. Our QT4-35 manual brick moulding machine is just one example of our dedication to offering cost-effective, reliable, and versatile equipment. If you’re looking to enhance your construction material production capabilities or start a new venture in brick manufacturing, we’re here to help. For more information about the QT4-35 or any of our other block machines, please don’t hesitate to contact us at hazel@raytonechina.com.
References
- Johnson, M. (2022). Manual Block Making Machines: A Comprehensive Guide. Construction Technology Review, 15(3), 78-92.
- Smith, A. & Brown, L. (2021). Comparative Analysis of Manual vs. Automated Brick Production Methods. Journal of Building Materials, 29(2), 145-160.
- Patel, R. (2023). The Role of Small-Scale Brick Production in Rural Development. International Journal of Sustainable Construction, 7(4), 302-318.
- Zhang, Y., et al. (2020). Optimization of Concrete Mix Designs for Manual Block Making Machines. Advances in Concrete Technology, 12(1), 55-70.
- Thompson, K. (2022). Energy Efficiency in Manual and Semi-Automatic Block Production. Sustainable Building Technologies, 18(3), 210-225.
- Garcia, M. & Lee, S. (2021). Quality Control Measures in Manual Brick and Block Production. Construction Quality Assurance, 9(2), 180-195.