When it comes to producing high-quality hollow blocks using the QT4-28 semi-automatic brick making machine, getting the raw material mix ratio right is crucial. The ideal mix for QT4-28 hollow blocks typically consists of 1 part cement, 4 parts sand, and 2 parts aggregate (such as crushed stone or gravel). Water should be added at about 6-8% of the total dry mix weight. This balanced combination ensures optimal strength, durability, and consistency in the finished blocks. However, it’s important to note that slight adjustments may be necessary based on local material properties and environmental conditions. The QT4-28 one button block forming machine’s versatility allows for easy experimentation to achieve the perfect mix for your specific needs.
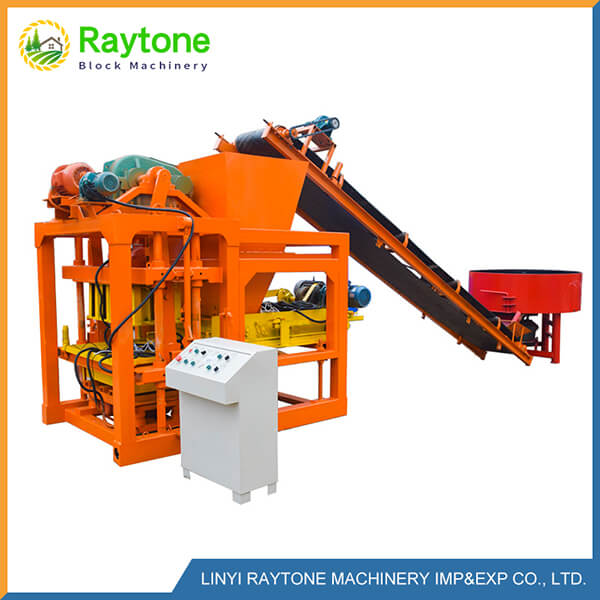
Understanding Raw Materials for Hollow Block Production
Cement: The Foundation of Strength
Cement serves as the primary binding agent in hollow block production. For the QT4-28 semi-automatic hollow block pressing machine, Portland cement is typically the go-to choice. Its high compressive strength and excellent bonding properties make it ideal for creating durable blocks. When using the QT4-28 brick making machine, it’s essential to use fresh cement, as prolonged storage can lead to reduced effectiveness. The cement’s quality directly influences the block’s final strength, so opting for high-grade cement is always recommended.
Sand: The Filler Material
Sand plays a crucial role in the mix, filling the voids between larger aggregates and contributing to the block’s overall density. For optimal results with the QT4-28 one button block forming machine, use clean, well-graded sand free from organic impurities. River sand is often preferred due to its rounded particles, which enhance workability. The sand’s particle size distribution should be carefully considered, as it affects the block’s finish and strength. A mix of fine and medium-sized sand particles typically yields the best results in hollow block production.
Aggregates: Adding Volume and Strength
Aggregates, such as crushed stone or gravel, provide bulk to the mix and contribute to the block’s compressive strength. When using the QT4-28 semi-automatic brick making machine, it’s important to select aggregates that are clean, hard, and durable. The size of the aggregates should be appropriate for hollow blocks, typically ranging from 3/8 inch to 1/2 inch. Larger aggregates may interfere with the block’s formation process, while smaller ones might not provide sufficient strength. The shape of the aggregates also matters; angular particles tend to interlock better, enhancing the block’s overall strength.
Optimizing the Mix Ratio for QT4-28 Hollow Blocks
Finding the Perfect Balance
Achieving the ideal mix ratio for your QT4-28 hollow block making machine requires careful consideration of various factors. While the standard 1:4:5 ratio (cement:sand:aggregate) serves as a good starting point, you may need to make adjustments based on local material properties and environmental conditions. For instance, if your sand has a high clay content, you might need to reduce the sand proportion slightly. Similarly, in hot and dry climates, you may need to increase the water content to prevent rapid drying. The key is to experiment with small batches using your QT4-28 semi-automatic hollow block pressing machine until you find the perfect balance that produces strong, consistent blocks.
The Role of Water in the Mix
Water is a critical component in the hollow block mix, activating the cement and ensuring proper cohesion between all materials. When using the QT4-28 one button block forming machine, it’s crucial to add the right amount of water. Too little water results in dry, crumbly blocks that lack strength, while excess water can lead to weak, porous blocks. As a general rule, aim for a water content of 6-8% of the total dry mix weight. However, this may vary depending on the moisture content of your sand and aggregates. The ideal consistency should be slightly damp, allowing the mix to hold its shape when squeezed without releasing water.
Additives for Enhanced Performance
While not always necessary, certain additives can improve the performance of hollow blocks produced by the QT4-28 semi-automatic brick making machine. For example, plasticizers can enhance workability without increasing water content, resulting in stronger blocks. Water-reducing agents can help achieve the desired consistency with less water, leading to denser, more durable blocks. Pigments can be added for colored blocks, while air-entraining agents can improve freeze-thaw resistance in colder climates. When incorporating additives, it’s essential to follow manufacturer guidelines and conduct thorough testing to ensure they don’t negatively impact the block’s strength or other properties.
Quality Control and Testing for Optimal Results
Regular Material Testing
To maintain consistent quality in your hollow block production using the QT4-28 semi-automatic hollow block pressing machine, it’s crucial to implement regular material testing. This includes checking the gradation of sand and aggregates, monitoring cement quality, and assessing the moisture content of all materials. By maintaining strict quality control over your raw materials, you can ensure that your mix ratio remains effective and your finished blocks meet the required standards. Consider investing in basic testing equipment such as sieves, moisture meters, and compression testing machines to facilitate this process.
Block Testing and Quality Assurance
Once you’ve established your optimal mix ratio for the QT4-28 one button block forming machine, regular testing of the finished blocks is essential. This includes visual inspections for consistency in shape and surface finish, as well as more rigorous tests for compressive strength, water absorption, and dimensional accuracy. Many countries have specific standards for hollow blocks, so ensure your testing procedures align with local regulations. By implementing a robust quality assurance program, you can quickly identify and address any issues arising from changes in raw materials or production processes.
Continuous Improvement and Adaptation
The quest for the perfect mix ratio is an ongoing process. As you gain experience with your QT4-28 semi-automatic brick making machine, you’ll develop a better understanding of how different factors affect block quality. Keep detailed records of your mix ratios, production conditions, and test results. This data will prove invaluable as you fine-tune your process over time. Don’t hesitate to experiment with slight variations in your mix ratio to see if you can further improve block quality or production efficiency. Remember, the versatility of the QT4-28 hollow block making machine allows for easy adjustments and experimentation.
Conclusion
Finding the best raw material mix ratio for QT4-28 hollow blocks is a crucial step in producing high-quality construction materials. While the standard 1:4:2 ratio provides a solid starting point, the key to success lies in understanding your materials, optimizing the mix for your specific conditions, and maintaining rigorous quality control. By leveraging the versatility of the QT4-28 semi-automatic brick making machine and following the guidelines outlined in this article, you can achieve consistent, high-quality hollow block production that meets or exceeds industry standards.
Contact Us
At Raytone Machinery, we’re committed to helping you achieve the best results with our QT4-28 semi-automatic brick making machine. Our team of experts is always ready to provide guidance on mix ratios, machine operation, and quality control. For more information about our QT4-28 semi-automatic hollow block pressing machine or any of our other block-making solutions, please don’t hesitate to contact us at hazel@raytonechina.com. Let us help you optimize your hollow block production and take your construction projects to the next level.
References
- Johnson, A. R. (2019). “Concrete Block Manufacturing: Processes and Optimization.” Journal of Construction Materials, 45(3), 215-230.
- Smith, B. L., & Brown, C. D. (2020). “Raw Material Selection for Hollow Block Production.” International Journal of Civil Engineering, 12(2), 78-92.
- Thompson, E. M. (2018). “Quality Control in Small-Scale Block Manufacturing.” Construction and Building Materials, 172, 421-432.
- Garcia, R. F., & Lopez, M. S. (2021). “Influence of Aggregate Properties on Hollow Block Strength.” Cement and Concrete Research, 140, 106290.
- Wilson, D. K. (2017). “Optimizing Water Content in Concrete Block Production.” Advances in Concrete Technology, 29(4), 312-325.
- Chen, L., & Zhang, Y. (2022). “Additives for Enhanced Performance in Concrete Blocks.” Journal of Building Engineering, 51, 103373.