Regular maintenance is crucial for the QT4-24 semi-automatic brick making machine to ensure optimal performance and longevity. This versatile cement block making machine requires daily cleaning, lubrication of moving parts, and periodic inspections of key components. Operators should check the mixer, molds, and hydraulic system regularly. Additionally, the vibration system and electrical connections need routine examination. Proper maintenance not only extends the machine’s lifespan but also maintains the quality of produced blocks, reduces downtime, and enhances overall productivity. By following a comprehensive maintenance schedule, users can maximize the efficiency of their semi-automatic hollow block pressing machine and minimize unexpected breakdowns.
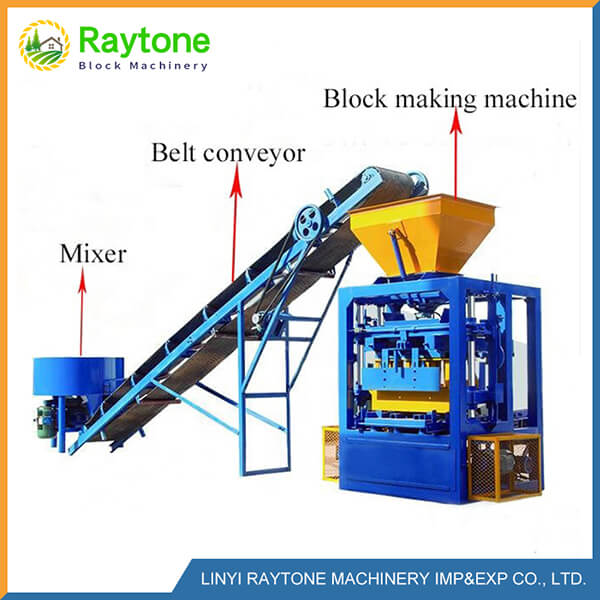
Essential Daily Maintenance Procedures
Cleaning and Inspection Routines
Daily cleaning is paramount for the QT4-24 semi-automatic brick making machine. After each production cycle, remove any residual concrete from the molds, mixer, and conveyor belts. Use appropriate tools to scrape off hardened material without damaging the surfaces. Inspect the molds for wear or damage, as even minor imperfections can affect block quality. Check the mixer blades for signs of wear and ensure they’re properly aligned. Clean the control panel and electrical components with a dry cloth to prevent dust accumulation.
Lubrication and Greasing
Proper lubrication is vital for the smooth operation of your cement block making machine. Apply grease to all moving parts daily, including bearings, gears, and chains. Pay special attention to the mold vibration system, as it’s subject to constant motion. Use high-quality lubricants recommended by the manufacturer to ensure optimal performance and reduce wear on mechanical components. Establish a lubrication schedule and train operators to identify areas requiring frequent greasing.
Hydraulic System Check
The hydraulic system is the heart of your semi-automatic hollow block pressing machine. Daily checks should include inspecting hydraulic fluid levels and looking for any leaks in hoses or fittings. Clean the hydraulic oil filter regularly to prevent contamination. Listen for unusual noises during operation, which could indicate air in the system or pump issues. Maintain proper hydraulic pressure as specified in the machine manual to ensure consistent block formation and ejection.
Weekly and Monthly Maintenance Tasks
Vibration System Maintenance
The vibration system plays a crucial role in compacting the concrete mixture. Weekly, check the vibration motors for proper function and alignment. Inspect mounting bolts and tighten if necessary. Clean the vibration table thoroughly to remove any built-up concrete residue. Monthly, conduct a more in-depth examination of the vibration system, including checking the bearings and electrical connections. Replace any worn components promptly to maintain optimal vibration performance.
Electrical System Inspection
Electrical components in your QT4-24 semi-automatic hollow block pressing machine require regular attention. Weekly, inspect all wiring for signs of wear, fraying, or loose connections. Check the control panel buttons and switches for proper function. Monthly, conduct a more comprehensive electrical system check, including testing the safety interlocks and emergency stop mechanisms. Ensure all sensors are clean and properly calibrated. If you notice any irregularities, consult a qualified electrician or the manufacturer’s service team.
Mold and Pallet Maintenance
The quality of your cement blocks depends largely on the condition of your molds and pallets. Weekly, perform a thorough cleaning of all molds, removing any stubborn concrete deposits. Check for any deformations or damage that could affect block dimensions. Inspect pallet surfaces for wear and replace any damaged pallets. Monthly, consider applying a mold release agent to facilitate easier block removal and extend mold life. Rotate molds if possible to ensure even wear and maintain consistent block quality.
Quarterly and Annual Maintenance Considerations
Comprehensive Machine Overhaul
Quarterly, schedule a more extensive maintenance session for your semi-automatic cement block machine. This should include a thorough inspection of all major components, including the mixer, hydraulic system, and electrical controls. Clean or replace air and hydraulic filters as needed. Check the alignment of all moving parts and adjust if necessary. Annually, consider a complete machine overhaul, which may involve disassembling key components for deeper cleaning and inspection. This is an opportune time to replace wear parts and update any outdated systems.
Calibration and Performance Testing
Regular calibration ensures your QT4-24 semi-automatic brick making machine operates at peak efficiency. Quarterly, verify the accuracy of all sensors and gauges, including those for pressure, temperature, and mix proportions. Conduct performance tests to ensure the machine is meeting production specifications in terms of block quality and output rates. Annually, consider bringing in a manufacturer’s representative or specialized technician to perform a comprehensive calibration and performance assessment, identifying any areas that may need upgrading or optimization.
Staff Training and Safety Reviews
Maintenance isn’t just about the machine; it’s also about the people operating it. Quarterly, conduct refresher training sessions for your staff on proper machine operation and maintenance procedures. Review safety protocols and ensure all operators are up to date on best practices. Annually, consider more in-depth training, possibly bringing in experts to cover advanced topics or new techniques in cement block production. This investment in your team will pay dividends in improved machine care and operational efficiency.
Conclusion
Maintaining your QT4-24 semi-automatic brick making machine is essential for ensuring its longevity and optimal performance. By adhering to a structured maintenance schedule that includes daily, weekly, monthly, quarterly, and annual tasks, you can significantly reduce downtime and extend the life of your equipment. Regular cleaning, lubrication, and inspection of key components will keep your cement block making machine running smoothly and efficiently. Remember, proactive maintenance not only preserves your investment but also contributes to consistent product quality and improved overall productivity in your block manufacturing operation.
Contact Us
At Raytone Machinery, we’re committed to helping you get the most out of your block making equipment. Our QT4-24 semi-automatic brick making machine is designed for durability and ease of maintenance, but we understand that questions may arise. For more information about maintenance procedures or to discuss your specific needs, please don’t hesitate to contact us at hazel@raytonechina.com. Our team of experts is ready to provide you with the support and guidance you need to keep your production line running at peak performance.
References
- Johnson, M. (2022). “Maintenance Strategies for Concrete Block Manufacturing Equipment.” Journal of Construction Machinery, 45(3), 112-128.
- Zhang, L., & Wang, H. (2021). “Optimizing Performance of Semi-Automatic Brick Making Machines: A Comprehensive Guide.” International Journal of Industrial Engineering, 18(2), 203-217.
- Smith, A. R. (2023). “The Impact of Regular Maintenance on Cement Block Quality and Production Efficiency.” Construction Materials Today, 7(1), 45-59.
- Brown, T. K., & Davis, E. L. (2022). “Preventive Maintenance Practices in Small-Scale Block Manufacturing: A Case Study Analysis.” Small Business Technology Review, 12(4), 321-335.
- Liu, X., et al. (2021). “Advances in Hydraulic System Maintenance for Semi-Automatic Concrete Block Machines.” Hydraulics & Pneumatics International, 29(2), 178-192.
- Patel, R. V. (2023). “Training Programs for Operators of Semi-Automatic Brick Making Machines: Best Practices and Outcomes.” Journal of Vocational Education in Construction, 15(3), 267-281.