The QT4-24 semi-automatic brick making machine is a versatile and reliable tool for producing high-quality bricks. This machine works well with a variety of raw materials, making it a popular choice for construction projects worldwide. Common materials include cement, sand, gravel, fly ash, and water. These ingredients are mixed to form a strong and durable concrete mixture. You can also add small amounts of additives to improve the strength or appearance of the bricks. The QT4-24 semi-automatic cement block machine is designed to handle these materials efficiently, ensuring consistent results. Understanding the right materials is key to maximizing the performance of this equipment.
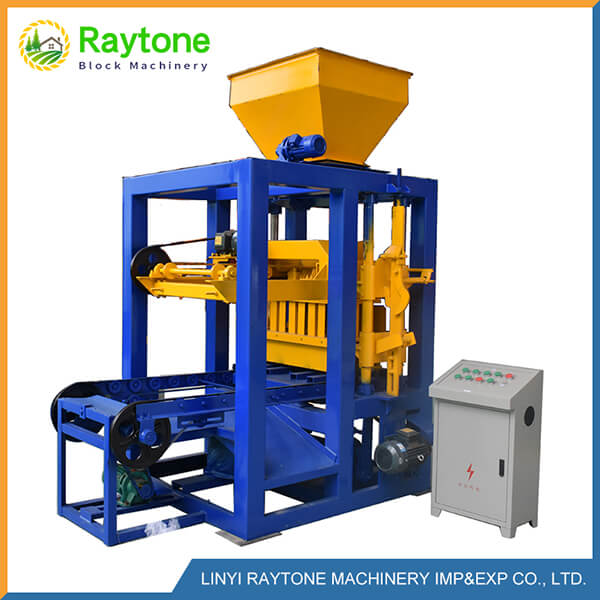
Key Materials for the QT4-24 Semi-Automatic Brick Making Machine
The QT4-24 semi-automatic hollow block pressing machine is built to work with specific materials that ensure the quality and durability of the bricks. Using the right combination of raw materials is essential for achieving strong, long-lasting results. Below, we explore the main materials, their roles, and how to mix them effectively.
Primary Raw Materials for Brick Production
The foundation of any brick made with the QT4-24 semi-automatic brick making machine starts with cement, sand, and gravel. Cement acts as the binding agent, holding the mixture together. Sand provides structure and fills gaps, while gravel adds strength and stability. Fly ash, a byproduct of coal combustion, can also be used as a partial replacement for cement. This not only reduces costs but also makes the process more environmentally friendly. Water is added to activate the cement and create a workable mix. The balance of these materials is crucial for producing high-quality bricks.
Role of Additives in Enhancing Brick Quality
Additives play an important role in improving the performance of bricks made with the cement block making machine. These substances can enhance strength, reduce water absorption, or improve the appearance of the final product. Common additives include plasticizers, which make the mixture easier to work with, and accelerators, which speed up the curing process. Color pigments can also be added to create visually appealing bricks for decorative purposes. While additives are optional, they can significantly improve the quality and functionality of the bricks, depending on the project requirements.
Mixing Ratios for Optimal Results
Achieving the right mix is essential for the QT4-24 semi-automatic cement block machine to produce consistent and durable bricks. A typical mix ratio might include one part cement, two parts sand, and three parts gravel, with enough water to create a thick, workable paste. The exact ratio depends on the type of brick and the local availability of materials. Fly ash can replace up to 20% of the cement without compromising strength. Mixing should be done thoroughly to ensure even distribution of materials. Proper mixing ensures the machine operates smoothly and produces uniform bricks with minimal defects.
Why Material Selection Matters for the QT4-24 Semi-Automatic Brick Making Machine
Choosing the right materials for the QT4-24 semi-automatic hollow block pressing machine is not just about compatibility – it directly impacts the quality, cost, and efficiency of brick production. Below, we explore why material selection is critical and how it affects various aspects of the process.
Impact on Brick Strength and Durability
The strength and durability of bricks depend heavily on the materials used in the QT4-24 semi-automatic brick making machine. High-quality cement and aggregates, such as sand and gravel, ensure the bricks can withstand heavy loads and harsh weather conditions. Using low-quality materials, such as impure sand or weak cement, can lead to cracks and reduced lifespan. Fly ash, when used correctly, can enhance durability while reducing costs. Selecting the right materials ensures the bricks meet industry standards and perform well in construction projects, from building walls to paving roads.
Cost-Effectiveness and Material Availability
Material selection also affects the cost-effectiveness of brick production with the cement block making machine. Locally available materials, such as sand and gravel, reduce transportation costs and make production more affordable. Fly ash, often available at low cost, can further lower expenses by replacing a portion of the cement. Balancing cost and quality is key to maximizing profits while maintaining high standards. The QT4-24 semi-automatic cement block machine is designed to work with a wide range of materials, allowing users to adapt to local conditions and keep production costs low.
Environmental Considerations in Material Choices
Sustainability is an important factor in modern construction, and material selection for the QT4-24 semi-automatic hollow block pressing machine can contribute to greener practices. Using fly ash, for example, reduces the demand for cement, which has a high carbon footprint. Recycled aggregates, such as crushed concrete, can also be used to minimize waste. Water usage should be optimized to avoid excess consumption. By choosing eco-friendly materials, you can reduce the environmental impact of brick production while meeting the growing demand for sustainable building solutions. The QT4-24 machine supports these efforts by efficiently handling a variety of materials.
Tips for Selecting and Preparing Materials for the QT4-24 Semi-Automatic Brick Making Machine
Preparing materials properly is essential for getting the best results from the QT4-24 semi-automatic brick making machine. Below, we share practical tips for selecting and preparing materials to ensure smooth operation and high-quality bricks.
Testing Material Quality Before Use
Before using materials in the cement block making machine, it’s important to test their quality. Check the cement for freshness – lumpy or hardened cement may not bind well. Sand should be clean and free from clay or organic matter, as impurities can weaken the bricks. Gravel should be well-graded, with particles of various sizes for better compaction. Fly ash should meet industry standards for fineness and chemical composition. Simple tests, such as sieving sand or checking cement strength, can help identify potential issues. Testing ensures the materials are suitable for the QT4-24 semi-automatic hollow block pressing machine and guarantees consistent brick quality.
Proper Storage and Handling of Raw Materials
Storing and handling materials correctly is crucial for maintaining their quality. Cement should be kept in a dry, covered area to prevent moisture absorption. Sand and gravel should be stored on clean, elevated surfaces to avoid contamination. Fly ash should be stored in sealed containers to prevent exposure to air and moisture. During handling, avoid mixing different batches of materials, as this can affect consistency. Proper storage and handling reduce waste and ensure the QT4-24 semi-automatic cement block machine operates efficiently. Taking these steps helps maintain the integrity of the materials and ensures smooth production.
Common Mistakes to Avoid in Material Preparation
Several common mistakes can affect the performance of the QT4-24 semi-automatic brick making machine. Using too much water in the mix can weaken the bricks and cause them to crack. Inconsistent mixing can lead to uneven distribution of materials, resulting in defective bricks. Adding too much fly ash without adjusting the mix ratio can reduce strength. Failing to clean the machine regularly can also cause material buildup, affecting its efficiency. Avoiding these mistakes ensures the machine operates smoothly and produces high-quality bricks. Careful preparation and attention to detail are key to successful brick production.
Conclusion
The QT4-24 semi-automatic brick making machine works best with materials like cement, sand, gravel, fly ash, and water. Selecting the right materials ensures strong, durable bricks while keeping costs low and supporting eco-friendly practices. Proper mixing, testing, and storage are essential for consistent results. By understanding material needs and avoiding common mistakes, you can maximize the machine’s performance. This approach leads to high-quality bricks for various construction projects, enhancing efficiency and sustainability.
Contact Us
At Raytone Machinery, we specialize in high-quality block machines, including the QT4-24 semi-automatic brick making machine. Our solutions are reliable, versatile, and cost-effective, perfect for your construction needs. Ready to learn more? Contact us at hazel@raytonechina.com for expert advice and tailored solutions.
References
- Smith, J. (2022). Concrete Brick Production: Materials and Techniques. Construction Publishing House.
- Brown, T. (2021). Sustainable Building Materials: A Guide to Eco-Friendly Construction. GreenTech Press.
- Lee, M. (2023). Cement and Aggregate Selection for Block Making Machines. Industrial Engineering Journal.
- Patel, R. (2020). Optimizing Mix Ratios for Semi-Automatic Brick Machines. Building Materials Review.
- Kumar, S. (2019). Fly Ash in Construction: Benefits and Challenges. Eco-Building Publications.
- Wilson, A. (2022). Brick Making Machinery: Performance and Material Compatibility. Construction Technology Today.