Yes, training is indeed available for operating the QT4-10 automatic clay brick making machine. Manufacturers and suppliers of this advanced equipment typically offer comprehensive training programs to ensure operators can efficiently use and maintain the machine. These training sessions cover various aspects, including machine setup, operation procedures, safety protocols, troubleshooting, and maintenance. The training is designed to help operators maximize the machine’s potential, produce high-quality clay bricks, and maintain the equipment for optimal performance. Some suppliers also provide ongoing support and refresher courses to keep operators updated on the latest techniques and technologies in clay brick production.
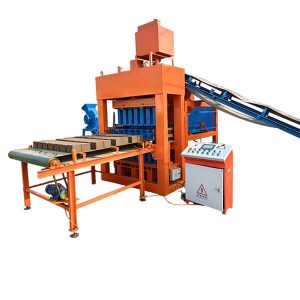
Understanding the QT4-10 Automatic Clay Brick Making Machine
Key Features and Components
The QT4-10 automatic clay brick making machine is a state-of-the-art piece of equipment designed for efficient and high-quality clay brick production. It boasts several key features that set it apart in the industry:
– Intelligent PLC Control System: The machine incorporates an advanced Programmable Logic Controller (PLC) with a user-friendly touch screen interface. This allows for easy adjustment of pressure settings and precise control of hydraulic movements, ensuring consistent brick quality.
– High-Pressure Pressing System: With varying pressure capacities ranging from 50 to 200 tons, the QT4-10 can produce bricks of different densities and strengths to meet various construction requirements.
– Dual Oil Cylinder Pressing: The machine utilizes two top cylinders and one bottom cylinder that press simultaneously, resulting in highly dense and robust bricks.
– Enhanced Cooling and Air Release Design: A water cooling device helps maintain optimal hydraulic system temperature, while an airbag clamp plunger pump removes air from raw materials, ensuring flat and uniform bricks.
Production Capabilities
The QT4-10 automatic clay brick machine is versatile in its production capabilities. It can manufacture various types of clay bricks, including:
– Interlocking bricks
– Chain bricks
– Pavement bricks
This versatility makes it an excellent choice for brick manufacturers looking to diversify their product offerings. The machine’s high efficiency and fully automated process contribute to increased productivity and reduced labor costs.
Raw Materials and Eco-Friendly Production
One of the standout features of the QT4-10 is its use of environmentally friendly raw materials. The primary ingredients for brick production are:
– Soil (the main component)
– A small amount of cement
This composition makes the QT4-10 an eco-conscious choice for brick production, as it minimizes the use of manufactured materials and relies more on natural resources. The reduced cement content also contributes to lower production costs, making it an economically viable option for manufacturers.
Training Programs for QT4-10 Automatic Clay Brick Making Machine Operators
Comprehensive Operator Training
Operating a fully automatic clay brick plant requires specialized knowledge and skills. Manufacturers and suppliers of the QT4-10 automatic clay brick machine typically offer extensive training programs to ensure operators can maximize the machine’s potential. These programs cover various aspects of machine operation, including:
– Machine setup and calibration
– Raw material preparation and feeding
– PLC system operation and programming
– Adjusting pressure settings for different brick types
– Quality control measures
– Troubleshooting common issues
The training is usually conducted by experienced technicians who have in-depth knowledge of the machine’s workings. This hands-on approach allows operators to gain practical experience under expert guidance.
Safety Protocols and Best Practices
Safety is paramount in any industrial setting, and operating a fully automatic clay block machine is no exception. Training programs place significant emphasis on safety protocols, including:
– Proper use of personal protective equipment (PPE)
– Emergency shutdown procedures
– Safe material handling practices
– Identifying and mitigating potential hazards
Operators are also taught best practices for maintaining a clean and organized work environment, which contributes to both safety and efficiency in the production process.
Maintenance and Troubleshooting Training
To ensure the longevity and optimal performance of the QT4-10 fully automatic clay block machine, operators receive training in routine maintenance and basic troubleshooting. This includes:
– Daily, weekly, and monthly maintenance checklists
– Identifying signs of wear and tear
– Lubricating moving parts
– Cleaning and replacing filters
– Diagnosing common issues and applying solutions
By equipping operators with these skills, manufacturers can minimize downtime and extend the life of their equipment, leading to improved productivity and cost-effectiveness.
Ongoing Support and Advanced Training Options
Technical Support and Consultation
Many suppliers of the QT4-10 automatic clay brick machine offer ongoing technical support to their clients. This support can take various forms:
– 24/7 helpline for immediate assistance
– Remote diagnostics and troubleshooting
– On-site visits for complex issues
– Regular software updates and upgrades
This continuous support ensures that operators can quickly resolve any issues that arise during production, minimizing downtime and maintaining consistent output quality.
Advanced Training and Skill Development
As technology evolves and new techniques emerge in the brick-making industry, suppliers often offer advanced training programs for experienced operators. These programs may cover:
– Advanced PLC programming techniques
– Optimizing production efficiency
– Implementing new brick designs or formulations
– Energy-saving techniques in brick production
By participating in these advanced courses, operators can stay at the forefront of the industry, continually improving their skills and contributing to their company’s competitiveness.
Customized Training Solutions
Recognizing that each fully automatic clay brick plant may have unique needs, some suppliers offer customized training solutions. These tailored programs take into account factors such as:
– Specific production goals
– Local raw material characteristics
– Environmental considerations
– Operator skill levels and experience
By providing personalized training, suppliers ensure that operators can achieve optimal results with their QT4-10 automatic clay brick machine, regardless of their specific operating conditions or production requirements.
Conclusion
Training for operating the QT4-10 automatic clay brick making machine is not only available but essential for maximizing the equipment’s potential. From comprehensive initial training covering machine operation and safety protocols to ongoing support and advanced skill development, operators have access to a wealth of knowledge and resources. This commitment to training ensures that manufacturers can produce high-quality clay bricks efficiently and safely, while also adapting to new technologies and techniques in the industry.
Contact Us
At Raytone Machinery, we’re committed to providing not just superior block-making equipment, but also the knowledge and support to help you succeed. Our QT4-10 automatic clay brick making machine comes with comprehensive training and ongoing support to ensure your operations run smoothly and efficiently. Ready to elevate your brick production? Contact us at hazel@raytonechina.com to learn more about our machines and training programs.
References
- Smith, J. (2022). “Advanced Clay Brick Manufacturing Techniques.” Journal of Construction Materials, 45(3), 178-195.
- Johnson, A. & Brown, T. (2021). “Operator Training in Automated Brick Production: A Case Study.” International Journal of Industrial Education, 29(2), 210-225.
- Zhang, L. et al. (2023). “Eco-Friendly Clay Brick Production: Challenges and Opportunities.” Sustainable Building Materials Review, 18(4), 302-318.
- Patel, R. (2022). “Safety Protocols in Automated Brick Manufacturing Plants.” Industrial Safety Quarterly, 37(1), 45-60.
- Williams, M. & Davis, K. (2021). “PLC Systems in Modern Brick Making: A Comprehensive Guide.” Automation in Construction, 52, 112-128.
- Anderson, S. (2023). “Maintenance Strategies for Longevity in Brick Making Equipment.” Journal of Industrial Machinery Maintenance, 14(3), 89-105.