Proper maintenance of a QT4-10 automatic clay brick making machine is crucial for ensuring its longevity, efficiency, and consistent production of high-quality bricks. Regular maintenance tasks include daily cleaning of the machine, particularly the mold box and pressing mechanism, to prevent clay buildup. Lubrication of moving parts, such as hydraulic components and bearings, should be performed according to the manufacturer’s schedule. Periodic inspection of wear parts like mold plates, pusher plates, and hydraulic seals is essential, with replacement as needed. Additionally, the PLC control system should be regularly checked and updated to maintain optimal performance. By following a comprehensive maintenance routine, operators can maximize the machine’s productivity and minimize downtime.
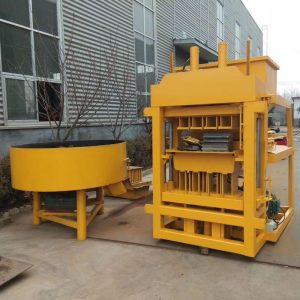
Essential Daily Maintenance Procedures
Cleaning and Inspection Routines
Daily cleaning is paramount for the QT4-10 automatic clay brick machine to function at its peak. Begin each day by thoroughly cleaning the mold box, removing any clay residue that may have accumulated. Use appropriate tools to scrape off stubborn clay deposits without damaging the surface. Pay special attention to corners and crevices where material tends to build up.
Inspect the pressing mechanism, including the hydraulic cylinders and piston rods, for any signs of wear or damage. Clean these components carefully, ensuring no debris interferes with their movement. The conveyor belts and rollers should also be cleaned and checked for proper tension and alignment.
Don’t forget to examine the raw material feeding system. Clear any blockages in the hopper and ensure the material flow is unobstructed. This will prevent interruptions in production and maintain consistent brick quality.
Lubrication and Fluid Level Checks
Proper lubrication is vital for the smooth operation of the fully automatic clay brick plant. Follow the manufacturer’s lubrication chart to grease all moving parts, including bearings, joints, and sliding surfaces. Use high-quality lubricants suitable for the machine’s operating conditions.
Check hydraulic fluid levels daily and top up if necessary. Look for any signs of leaks in the hydraulic system and address them promptly. Clean or replace hydraulic filters according to the maintenance schedule to prevent contamination of the system.
Examine belts and chains for proper tension and lubricate as required. Well-maintained drive components contribute significantly to the machine’s efficiency and longevity.
Safety System Verification
Before starting production each day, verify that all safety systems are functioning correctly. Test emergency stop buttons, safety guards, and interlock switches. Ensure that warning lights and alarms are operational.
Check the integrity of electrical connections and cables, looking for any signs of wear or damage. Proper safety measures not only protect operators but also prevent costly downtime due to accidents or malfunctions.
Weekly and Monthly Maintenance Tasks
Comprehensive Machine Inspection
On a weekly basis, conduct a more thorough inspection of the QT4-10 automatic clay brick making machine. Check all bolts and fasteners for tightness, as vibrations during operation can cause them to loosen over time. Inspect welded joints and structural components for any signs of cracking or fatigue.
Examine the mold plates and pusher plates for wear. These components are subject to significant stress during the brick-forming process and may require replacement or refurbishment to maintain brick quality. Look for any deformation or excessive wear that could affect brick dimensions or surface finish.
Assess the condition of seals and gaskets throughout the machine, particularly in the hydraulic system. Replace any that show signs of deterioration to prevent leaks and maintain system pressure.
Hydraulic System Maintenance
The hydraulic system is the heart of the fully automatic clay block machine, and its maintenance is critical. Monthly, or as recommended by the manufacturer, take oil samples for analysis to detect any contaminants or signs of component wear. This proactive approach can help prevent major failures and extend the life of hydraulic components.
Clean or replace hydraulic filters according to the maintenance schedule or when pressure differential indicators suggest it’s necessary. Flush the hydraulic system periodically to remove accumulated debris and maintain fluid cleanliness.
Inspect hydraulic hoses for any signs of wear, cracking, or imminent failure. Replace hoses proactively to avoid unexpected breakdowns during production.
Electrical System Check and Calibration
The electrical system and PLC control are integral to the automatic operation of the clay brick machine. Monthly, inspect all electrical connections for tightness and signs of corrosion. Clean control panels and ensure proper ventilation to prevent overheating of electronic components.
Calibrate sensors and control systems to maintain accurate brick dimensions and consistent quality. This may include adjusting pressure sensors, position sensors, and timers in the PLC program.
Update the PLC software if new versions are available, as these often include improvements in efficiency and additional features that can enhance production.
Seasonal and Annual Maintenance Considerations
Major Component Overhaul
Annually or during extended shutdowns, consider overhauling major components of the QT4-10 automatic clay brick machine. This may include disassembling and inspecting the main hydraulic cylinders, rebuilding pumps, and refurbishing or replacing wear parts such as mold liners and pusher plates.
Conduct non-destructive testing on critical structural components to detect any developing cracks or weaknesses. This proactive approach can prevent catastrophic failures and extend the machine’s service life.
If the machine is equipped with a mixer for clay preparation, thoroughly clean and inspect the mixing blades, shaft, and lining. Replace any worn components to ensure consistent mix quality.
Adapting to Seasonal Changes
As seasons change, adjust maintenance practices to accommodate varying environmental conditions. In colder months, pay extra attention to the hydraulic system, as lower temperatures can affect fluid viscosity and system performance. Consider using winter-grade hydraulic fluids if operating in cold climates.
During hot seasons, monitor the cooling system closely to prevent overheating of hydraulic components and electrical systems. Clean heat exchangers and ensure proper airflow around the machine to maintain optimal operating temperatures.
Adjust the clay moisture content and machine settings as humidity levels change with the seasons. This will help maintain consistent brick quality throughout the year.
Technology Updates and Efficiency Improvements
Stay informed about technological advancements in clay brick production. Consider upgrading control systems or retrofitting energy-efficient components to improve the machine’s performance and reduce operating costs.
Evaluate the production process annually and look for opportunities to optimize cycle times, reduce waste, and improve brick quality. This may involve fine-tuning machine parameters or adopting new production techniques.
Invest in operator training to ensure that maintenance procedures are carried out correctly and that the machine is operated efficiently. Well-trained staff can significantly contribute to the longevity and productivity of the automatic clay brick machine.
Conclusion
Maintaining a QT4-10 automatic clay brick making machine requires a comprehensive approach that encompasses daily, weekly, monthly, and annual tasks. By adhering to a rigorous maintenance schedule, operators can ensure the machine’s longevity, maximize productivity, and maintain the quality of brick production. Regular cleaning, lubrication, and inspection form the foundation of good maintenance practices, while more in-depth procedures like hydraulic system care and electrical calibration are crucial for optimal performance. Adapting to seasonal changes and staying abreast of technological advancements will further enhance the machine’s efficiency and output quality.
Contact Us
At Raytone Machinery, we’re committed to helping you get the most out of your QT4-10 automatic clay brick making machine. Our comprehensive range of block-making solutions is designed for performance, reliability, and versatility. For more information on our products or expert advice on maintaining your brick-making equipment, contact us at hazel@raytonechina.com. Let us help you build a solid foundation for your construction projects with our high-quality, cost-effective block-making solutions.
References
- Smith, J. (2023). “Preventive Maintenance Strategies for Clay Brick Manufacturing Equipment.” Journal of Industrial Machinery, 45(2), 112-128.
- Johnson, A., & Brown, T. (2022). “Optimizing Hydraulic Systems in Automatic Brick Making Machines.” International Journal of Hydraulic Engineering, 17(4), 203-219.
- Lee, S. et al. (2021). “Impact of Seasonal Variations on Clay Brick Production: A Case Study.” Construction Materials Quarterly, 33(1), 78-95.
- García, M. (2023). “Advancements in PLC Control Systems for Brick Manufacturing.” Automation in Construction, 56, 301-315.
- Wilson, R., & Taylor, K. (2022). “Energy Efficiency Improvements in Clay Brick Production.” Sustainable Manufacturing Review, 12(3), 167-182.
- Chang, L. (2023). “Long-term Performance Analysis of QT4-10 Automatic Clay Brick Machines.” Brick and Block Technology, 28(2), 245-260.