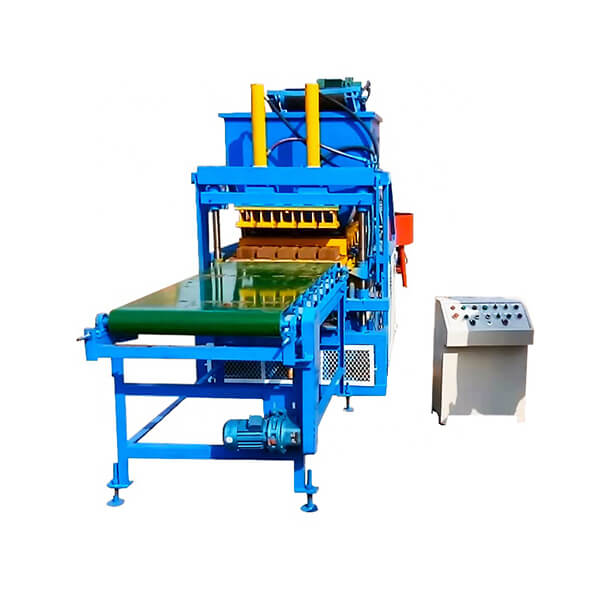
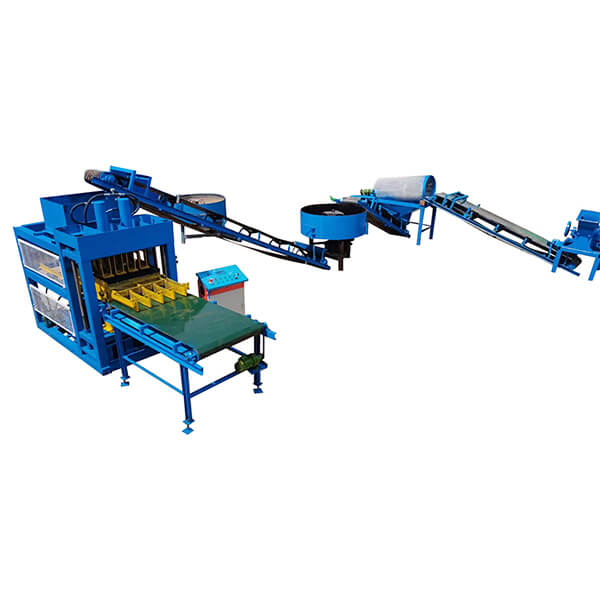
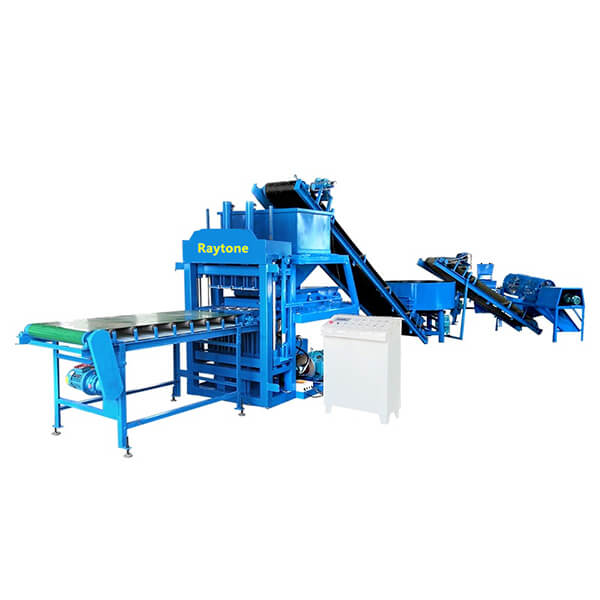
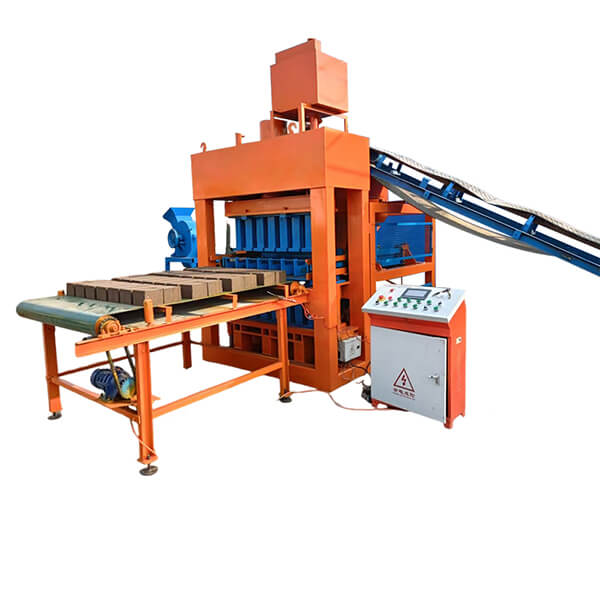

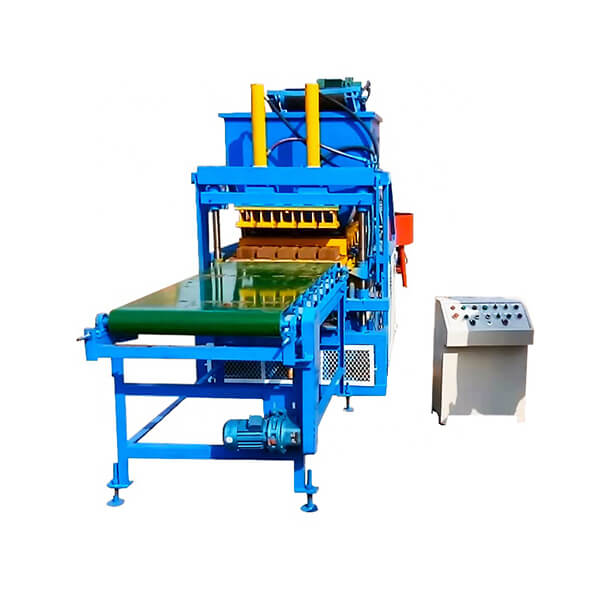
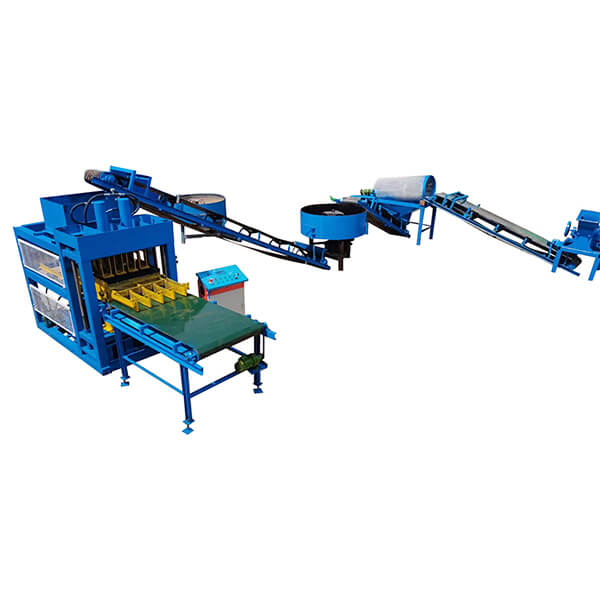
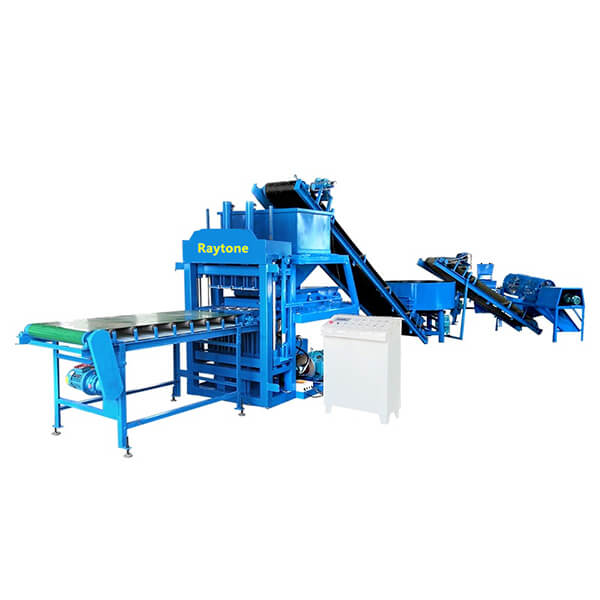
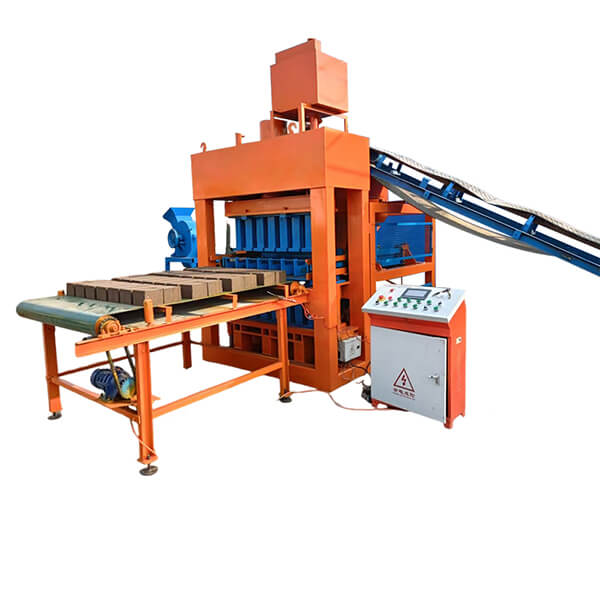

QT4-10 Automatic Brick Making Machine
The QT4-10 Automatic Clay Brick Making Machine is a high-efficiency, fully automated press for producing durable, eco-friendly clay bricks.
Introduction Of QT4-10 Automatic Brick Making Machine
The QT4-10 Automatic Clay Brick Making Machine is a high-efficiency, fully automated solution designed for the production of various types of clay bricks, including interlocking, chain, and pavement bricks. This machine uses advanced hydraulic technology, featuring a high-pressure pressing system with varying pressure capacities of 50 tons, 100 tons, 150 tons, and 200 tons to ensure precise brick formation. The raw materials for production are primarily soil and a small amount of cement, making it an eco-friendly and cost-effective option.
The key difference between the automatic clay brick machine and the automatic concrete block machine lies in their working principles. The automatic clay brick machine uses both top-down pressure and bottom-up pushing to form the bricks, which is essential for working with clay-based materials. In contrast, the automatic concrete block machine relies on top-down pressure combined with vibration at the bottom to compact the concrete mix. This difference in approach is due to the distinct properties of the raw materials—clay for the brick machine and concrete for the block machine—requiring different methods of compaction to achieve optimal results.
Advantages of the QT4-10 Automatic Brick Making Machine
1. Intelligent PLC Control System: The entire automatic clay brick machine is equipped with an intelligent PLC control system, working seamlessly with hydraulic movements for precise and efficient brick production.
2. User-Friendly Touch Screen: The PLC control box features an intuitive touch screen that allows easy adjustment of the pressure settings, providing simple and convenient control over the machine’s operation.
3. High-Quality Hydraulic Pump: The machine uses a high-quality hydraulic vane pump with low noise levels, ensuring strong oil pressure for clay brick pressing. The hydraulic system operates quietly, minimizing noise pollution during production.
4. Reliable Oil Pressure System: Featuring premium solenoid valves and proportional valves, the oil pressure system ensures fast and accurate control of the hydraulic movements. This guarantees the production of high-quality clay bricks with precise size and adequate pressure.
5. Efficient Hydraulic Oil Cooling: The water cooling device maintains the hydraulic oil at optimal temperatures, preventing overheating and ensuring the automatic clay brick machine operates steadily and reliably during long production runs.
6. Plunger Pump for Uniform Bricks: The machine uses a plunger pump with an airbag clamp version to remove air from raw materials, ensuring the bricks are smooth, flat, and uniform in size and shape.
7. Dual Hydraulic Cylinders: With two oil cylinders on the top mold and one oil cylinder under the down mold, the machine applies simultaneous pressure from both the top and bottom, resulting in strong, durable bricks that meet the highest standards of quality.
Get Free Quote of QT4-10 Automatic Brick Making Machine
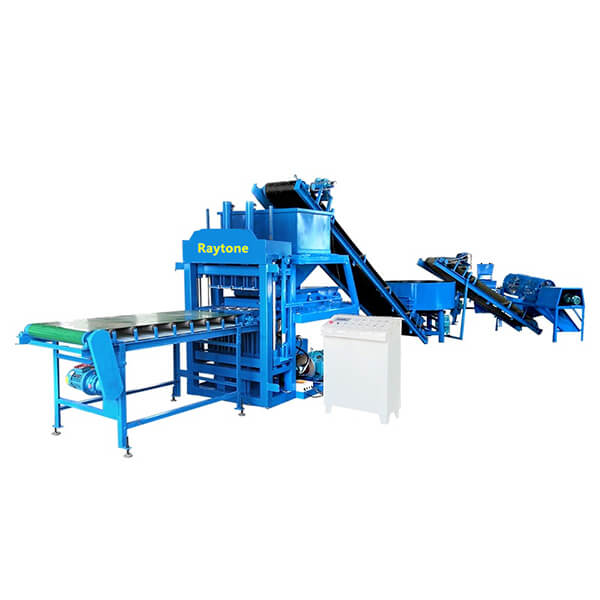
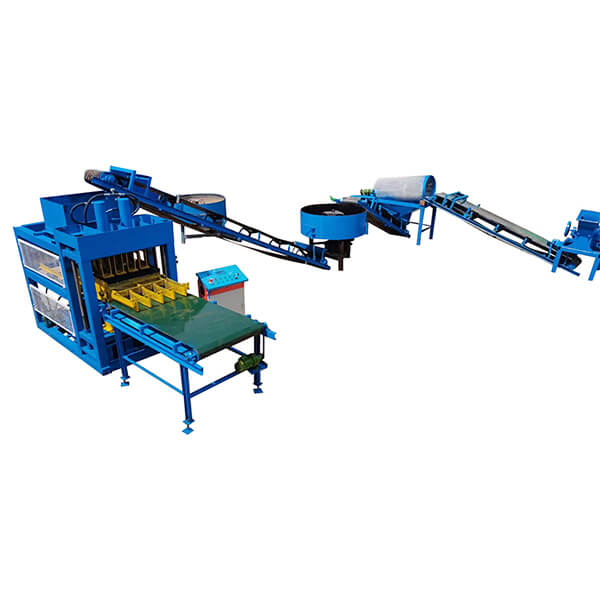
QT4-10 Automatic Clay Brick Making Machine Overview
The QT4-10 Automatic Clay Brick Making Machine uses high-pressure pressing (up to 100 tons) to produce various types of bricks, including interlocking, chain, and pavement bricks, by changing molds. It uses soil and a small amount of cement as raw materials.
- Production Capacity: Brick Size (300 × 150 × 100 mm):Pieces per Hour: 1,200;Pieces per Day: 9,600
- Price Range: $12,500 USD, depending on configuration
1. Flexible Power Options: Choose between diesel engine or electric motor power for versatility.
2. Easy Operation: PLC control allows operation by a single person, simplifying the process.
3. Fast Production: Each brick is made in under 10 seconds, ensuring quick output.
4. Adjustable Brick Height: Screw adjustment enables easy customization of brick height.
5. Customizable Molds: Molds can be changed according to meet customer-specific requirements for various brick types.
6. High Productivity: Produces 6000-8000 bricks per day, ideal for large-scale operations.
Detailed Introduction of QT4-10 Automatic Clay Brick Making Line
Number | Item | Function |
1 | Belt Conveyor | Transport raw materials of soil to next crushing machine |
2 | Soil crusher | Crush the soil into small powder |
3 | Belt Conveyor | Transport the crushed soil into the next soil screening machine |
4 | Soil screen | Filter good soil power |
5 | Belt Conveyor | Transport the screened soil into the pan mixer; |
6 | JQ500 Pan mixer | Mix raw material and water |
7 | Belt conveyor | Transport the soil from mixer to automatic clay brick making machine |
8 | Host brick machine | Produce different sizes of interlocking bricks |
Paraments Of QT4-10 Automatic Clay Brick Machine Host Machine
Item | Paraments |
Host brick machine | Dimension:2800*1550*2430mm
Moulding cycle: 7-10s Working method: hydraulic pressure Working method: hydraulic pressure power: 7.5KW Pressure: 20-25 mpa Weight: 2000kg With one set free mould 8.5*4*2.2 inch |
QT4-10 Clay Automatic Brick Machine Daily Production Capacity
Size (mm) | Photo | Pieces/Mould | Pieces/Hour | Piece/day |
300*150*100 | ![]() |
4 | 1200 | 9600 |
300*150*100 | ![]() |
4 | 1200 | 9600 |
300*150*100 | ![]() |
4 | 1200 | 9600 |
200*100*60mm | ![]() |
4 | 1200 | 9600 |
200*100*60 | ![]() |
4 | 1200 | 9600 |
QT4-10 Automatic Clay Brick Making Machine - Sample Brick Showcase
Clients can review the clay brick models shown in the photo below and choose the one that best suits their needs to confirm the corresponding brick molds for production.
We can also manufacture custom brick molds based on the dimensions and photos of your specific bricks.
1. How to adjust the brick height when need?
The brick height can be changed by adjusting screws.
2. How many land area is needed for automatic clay brick machine?
For the workshop, 70 Square meters can meet the needs of these modes automatic clay brick machine,
But for the curing area, because different brick productivity needs different land area, so the automatic clay brick machine needs curing area from 1200 square meters to 2500 square meters;
3. How many workers are needed for automatic clay brick making machine?
5 Workers in total.
One worker loads soil onto the Belt conveying machine for next crushing.
One Worker loads cement and water into the pan Mixer
One worker operates the automatic clay brick machine
Two Worker carries Fresh brick from: brick receiver to curing site
4. What is the ratio for making clay bricks?
Material Ratio for Bricks: 5%-10% cement and 90%-95% soil
5. What after-sale service do you supply?
We will supply customers manual and install video and we will can send our engineer to customers place to help customer install machine and train workers
6. What is the Raw Material Consumption in one day?
Here we take 300*150*100mm bricks as example and recommend 8% cement.
Size of Brick | 300*150*100mm lego brick |
Capacity of Brick | 14400 bricks in one day |
Material Ratio | 8% cement and 92% soil |
Consumption of Cement | 6912 KG per day |
Consumption of Soil | 79488 kg per day |
Consumption of water | 2-3 tons |
Working Videos
1. How to adjust the brick height when need?
The brick height can be changed by adjusting screws.
2. How many land area is needed for automatic clay brick machine?
For the workshop, 70 Square meters can meet the needs of these modes automatic clay brick machine,
But for the curing area, because different brick productivity needs different land area, so the automatic clay brick machine needs curing area from 1200 square meters to 2500 square meters;
3. How many workers are needed for automatic clay brick making machine?
5 Workers in total.
One worker loads soil onto the Belt conveying machine for next crushing.
One Worker loads cement and water into the pan Mixer
One worker operates the automatic clay brick machine
Two Worker carries Fresh brick from: brick receiver to curing site
4. What is the ratio for making clay bricks?
Material Ratio for Bricks: 5%-10% cement and 90%-95% soil
5. What after-sale service do you supply?
We will supply customers manual and install video and we will can send our engineer to customers place to help customer install machine and train workers
6. What is the Raw Material Consumption in one day?
Here we take 300*150*100mm bricks as example and recommend 8% cement.
Size of Brick | 300*150*100mm lego brick |
Capacity of Brick | 14400 bricks in one day |
Material Ratio | 8% cement and 92% soil |
Consumption of Cement | 6912 KG per day |
Consumption of Soil | 79488 kg per day |
Consumption of water | 2-3 tons |
Related Products
Related News
The M7MI TWIN diesel hydraform soil brick machine is a versatile and eco-friendly solution for brick-making, primarily using locally available soil, […]
The M7MI TWIN diesel hydraform soil brick machine boasts an impressive production capacity, capable of manufacturing up to 2,800 to 3,200 […]
The M7MI TWIN Hydraform Diesel Clay Brick Machine is revolutionizing the brick-making industry, especially in regions with unreliable electricity, such […]
The QT4-10 automatic clay brick making machine primarily utilizes soil and a small amount of cement as its main raw materials. […]
Proper maintenance of a QT4-10 automatic clay brick making machine is crucial for ensuring its longevity, efficiency, and consistent production of […]
The installation process for the QT4-10 automatic clay brick making machine involves several key steps to ensure optimal performance and longevity. […]
Yes, training is indeed available for operating the QT4-10 automatic clay brick making machine. Manufacturers and suppliers of this advanced […]
The QT4-10 automatic clay brick making machine is indeed energy-efficient, making it an excellent choice for sustainable brick production. This advanced […]