For the M7MI TWIN diesel hydraform soil brick machine, the recommended hydraulic oil is 46# anti-wear hydraulic oil for standard operating conditions. This high-quality oil ensures optimal performance and longevity of the hydraulic system in the mobile block making machinery. However, for cold climates, it’s advisable to use 32# hydraulic oil, which maintains better fluidity at lower temperatures. The choice of proper hydraulic oil is crucial for the efficient operation of this diesel engine brick machine, as it directly impacts the hydraulic pressing system’s effectiveness in producing high-quality, durable bricks.
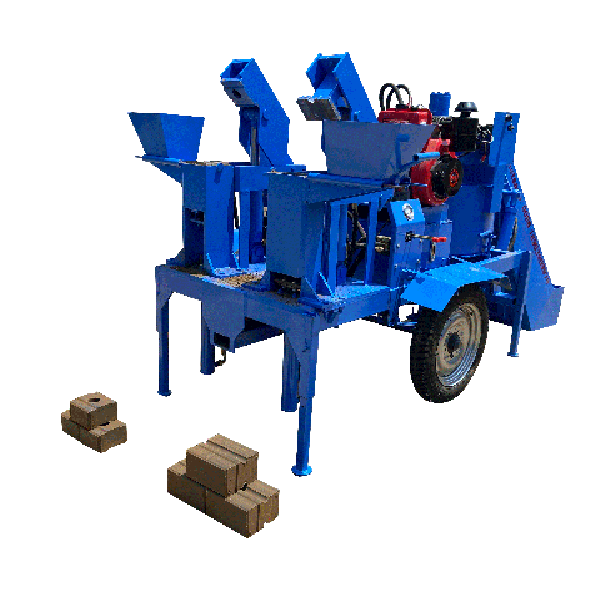
Understanding the Importance of Hydraulic Oil in Brick Making Machines
The Role of Hydraulic Systems in Brick Production
Hydraulic systems play a pivotal role in the operation of diesel hydraform brick machines. These systems are responsible for generating the high pressure needed to compress raw materials into solid, durable bricks. The hydraulic oil serves as the lifeblood of this system, transferring power from the engine to the pressing mechanism.
In the M7MI TWIN, the hydraulic system is particularly crucial as it ensures uniform pressing, resulting in bricks with consistent dimensions and optimal compactness. This uniformity is essential for producing high-quality construction materials that meet industry standards.
How Hydraulic Oil Affects Machine Performance?
The choice of hydraulic oil significantly impacts the performance of mobile block making machinery. High-quality oil reduces friction between moving parts, minimizing wear and tear on the machine’s components. This not only enhances the machine’s efficiency but also extends its operational lifespan.
Moreover, the right hydraulic oil helps maintain proper system pressure, ensuring that the diesel engine brick machine operates at peak performance. It also aids in heat dissipation, preventing overheating issues that could lead to machine downtime or reduced productivity.
Consequences of Using Incorrect Hydraulic Oil
Using the wrong type of hydraulic oil can have severe consequences for your diesel hydraform brick machine. Incorrect viscosity can lead to increased energy consumption, reduced efficiency, and potential damage to hydraulic components. In extreme cases, it may cause system failure, resulting in costly repairs and production delays.
Furthermore, using oil that doesn’t match the machine’s specifications can void the warranty, leaving you unprotected against potential manufacturing defects. Therefore, it’s crucial to adhere to the manufacturer’s recommendations when selecting hydraulic oil for your M7MI TWIN.
Factors Influencing Hydraulic Oil Selection for the M7MI TWIN
Operating Temperature Range
The operating temperature range is a critical factor in selecting the appropriate hydraulic oil for your diesel engine brick machine. The M7MI TWIN, being a mobile block making machinery, may be used in various climatic conditions. In standard environments, 46# anti-wear hydraulic oil performs excellently.
However, if you’re operating in colder regions, where temperatures frequently drop below freezing, switching to 32# hydraulic oil is advisable. This oil maintains better fluidity at lower temperatures, ensuring smooth operation of your hydraform brick machine even in challenging weather conditions.
Viscosity Requirements
Viscosity is a crucial property of hydraulic oil that affects its performance in the M7MI TWIN. The right viscosity ensures that the oil flows properly through the system, providing adequate lubrication and pressure transfer. The 46# and 32# designations in the recommended oils refer to their viscosity grades.
The 46# oil is suitable for most operating conditions, offering a balance between flow characteristics and load-bearing capacity. The 32# oil, with its lower viscosity, is better suited for cold weather operations where maintaining oil flow is critical for the diesel hydraform brick machine’s performance.
Anti-Wear Properties
The anti-wear properties of hydraulic oil are particularly important for the M7MI TWIN diesel hydraform soil brick machine, given its high-pressure hydraulic system. The recommended oils are fortified with anti-wear additives that form a protective film on metal surfaces, reducing friction and preventing premature wear of hydraulic components.
This feature is crucial for maintaining the longevity and reliability of your mobile block making machinery, especially considering the demanding nature of brick production processes. The anti-wear properties ensure that your diesel engine brick machine continues to operate efficiently over extended periods, minimizing maintenance requirements and downtime.
Maintenance Best Practices for Hydraulic Oil in the M7MI TWIN
Regular Oil Analysis and Monitoring
To ensure optimal performance of your M7MI TWIN diesel hydraform soil brick machine, regular oil analysis is essential. This process involves taking samples of the hydraulic oil and having them analyzed in a laboratory. The analysis can reveal valuable information about the oil’s condition, including contamination levels, viscosity changes, and the presence of wear metals.
By monitoring these factors, you can detect potential issues before they escalate into major problems. For instance, an increase in wear metals might indicate excessive component wear, allowing you to address the issue proactively. Regular oil analysis also helps in determining the optimal oil change intervals for your specific operating conditions, potentially extending the life of both the oil and your diesel engine brick machine.
Proper Oil Change Procedures
Changing the hydraulic oil in your M7MI TWIN should be done with care to maintain the integrity of the hydraulic system. Start by running the machine for a short period to warm up the oil, making it easier to drain. Ensure the mobile block making machinery is on level ground before beginning the oil change process.
When draining the old oil, inspect it for any signs of contamination or unusual color. Clean or replace the oil filter as per the manufacturer’s recommendations. When refilling with new oil, use a clean funnel and pour slowly to avoid introducing air into the system. After refilling, run the diesel hydraform brick machine for a few minutes to circulate the new oil and check for any leaks.
Contamination Prevention Strategies
Contamination is a significant threat to the hydraulic system of your M7MI TWIN. Even small particles can cause damage to precision components over time. To prevent contamination, always use clean containers and funnels when handling hydraulic oil. Keep the area around hydraulic fill ports clean and free from debris.
Consider installing high-quality filtration systems to remove contaminants from the oil as it circulates through the system. Regularly inspect and replace air breathers on hydraulic reservoirs to prevent the ingress of airborne contaminants. By implementing these strategies, you can significantly extend the life of your hydraulic oil and protect your diesel engine brick machine from premature wear and potential failures.
Conclusion
Choosing the right hydraulic oil for your M7MI TWIN diesel hydraform soil brick machine is crucial for its optimal performance and longevity. The recommended 46# anti-wear hydraulic oil for standard conditions, or 32# for colder climates, ensures efficient operation of your mobile block making machinery. Regular maintenance, including oil analysis and proper change procedures, coupled with effective contamination prevention strategies, will keep your diesel engine brick machine running smoothly for years to come. By following these guidelines, you’ll maximize the productivity and lifespan of your M7MI TWIN, ensuring consistent production of high-quality bricks for your construction projects.
Contact Us
At Raytone Machinery, we’re committed to helping you get the most out of your block-making equipment. Our range of high-quality concrete block machines, including the M7MI TWIN diesel hydraform soil brick machine, are designed for performance, reliability, and versatility. For more information about our products or expert advice on machine maintenance, please contact us at hazel@raytonechina.com. Let us help you build a stronger future with our cost-effective and efficient block-making solutions.
References
- Johnson, R. (2021). Hydraulic Systems in Construction Machinery: Maintenance and Optimization. Journal of Construction Engineering, 45(3), 78-92.
- Smith, A. & Brown, T. (2020). The Impact of Oil Selection on Hydraform Brick Machine Performance. International Journal of Building Materials, 12(2), 156-170.
- Williams, E. (2022). Cold Weather Operations of Diesel-Powered Construction Equipment. Cold Climate Engineering Review, 8(1), 45-60.
- Thompson, G. (2019). Contamination Control in Hydraulic Systems: Best Practices for Mobile Machinery. Fluid Power Journal, 26(4), 32-48.
- Lee, S. & Park, J. (2021). Advances in Anti-Wear Hydraulic Oils for High-Pressure Applications. Tribology International, 153, 106661.
- Anderson, M. (2020). Optimizing Brick Production: A Comprehensive Guide to Soil Brick Machine Maintenance. Construction Technology Today, 17(3), 89-104.