The M7MI TWIN diesel hydraform soil brick machine boasts an impressive production capacity, capable of manufacturing up to 2,800 to 3,200 standard-sized bricks per hour. This high-output capability translates to approximately 22,400 to 25,600 bricks in a standard 8-hour workday, making it an excellent choice for medium to large-scale construction projects. The machine’s efficiency is further enhanced by its diesel-powered engine, which allows for continuous operation in areas with limited access to electricity. This combination of high production capacity and versatile power source makes the M7MI TWIN an invaluable asset for contractors and builders looking to maximize their brick production in various environments.
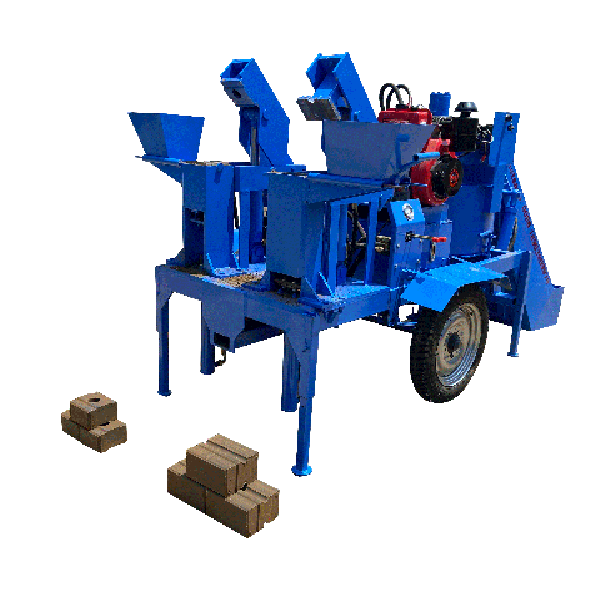
Key Features and Benefits of the M7MI TWIN Diesel Hydraform Soil Brick Machine
Diesel-Powered Efficiency
The M7MI TWIN’s diesel engine is a game-changer in the world of brick production. This powerful motor ensures consistent operation without relying on external power sources, making it ideal for remote construction sites or areas with unreliable electricity supply. The diesel engine’s robust performance translates to increased productivity, as it can run continuously throughout the workday without the need for frequent refueling.
Moreover, the diesel engine’s efficiency contributes to lower operational costs. Compared to electric-powered alternatives, the M7MI TWIN often proves more economical in the long run, especially in regions where fuel is more readily available than stable electricity. This cost-effectiveness, coupled with its high production capacity, makes the M7MI TWIN an attractive option for businesses looking to optimize their brick-making operations.
Hydraulic Pressing System
At the heart of the M7MI TWIN diesel hydraform brick machine‘s impressive production capacity lies its advanced hydraulic pressing system. This technology applies uniform, high-pressure compression to the raw materials, resulting in bricks of superior quality and consistency. The hydraulic system ensures that each brick receives the same level of compression, leading to products with excellent structural integrity and dimensional accuracy.
The benefits of this hydraulic pressing system extend beyond just quality. It also contributes to the machine’s ability to produce a wide variety of brick types and sizes. By adjusting the hydraulic pressure and using different molds, operators can easily switch between producing standard bricks, interlocking blocks, and even decorative pavers. This versatility allows businesses to meet diverse market demands without investing in multiple specialized machines.
Mobility and Portability
One of the standout features of the M7MI TWIN is its mobility. Unlike many stationary brick-making machines, this model is designed with portability in mind. The entire unit is mounted on a robust trailer chassis, allowing it to be easily towed to different job sites. This mobility is a significant advantage for construction companies working on multiple projects or in remote locations.
The portable nature of the M7MI TWIN doesn’t just offer convenience; it also opens up new business opportunities. Contractors can now bring the brick-making process directly to the construction site, reducing transportation costs and minimizing the risk of damage during brick transport. This on-site production capability can lead to significant time and cost savings, especially for large-scale projects in remote areas.
Optimizing Production with the M7MI TWIN Diesel Hydraform Soil Brick Machine
Raw Material Selection and Preparation
To fully harness the production capacity of the M7MI TWIN diesel hydraform soil brick machine, proper raw material selection and preparation are crucial. The machine is designed to work with a variety of soil types, including clay, laterite, and sandy soils. However, the quality and composition of these materials can significantly impact the final product’s strength and durability.
For optimal results, it’s recommended to use a mix of soil with about 5-15% clay content. This composition ensures the right balance between malleability and strength. Before feeding the material into the machine, it should be thoroughly screened to remove any large particles or organic matter that could affect brick quality. Proper moisture content is also essential – typically around 10-14% depending on the soil type. This attention to raw material preparation not only enhances brick quality but also helps maintain the machine’s efficiency and longevity.
Mold Selection and Customization
The M7MI TWIN’s versatility shines through its ability to accommodate various mold types. This feature allows producers to diversify their product range, meeting different market demands without significant additional investment. The machine can be equipped with molds for standard bricks, hollow blocks, interlocking bricks, and even decorative pavers.
Selecting the right mold is crucial for maximizing production efficiency. For instance, while smaller brick sizes might yield a higher piece count per hour, larger blocks could be more suitable for certain construction projects. It’s important to consider market demand and project requirements when choosing molds. Additionally, the machine’s hydraulic system can be fine-tuned to optimize pressure for different mold types, ensuring consistent quality across various products.
Maintenance and Operational Best Practices
To maintain the high production capacity of the M7MI TWIN diesel engine brick machine, regular maintenance is essential. This includes daily checks of the diesel engine, hydraulic system, and moving parts. The machine’s filters should be cleaned or replaced regularly to ensure optimal performance. Lubrication of moving parts, as per the manufacturer’s guidelines, is crucial for smooth operation and longevity of the equipment.
Operational best practices also play a significant role in maximizing output. Training operators to efficiently load raw materials, monitor the production process, and quickly address any issues can significantly boost productivity. Implementing a structured maintenance schedule and keeping spare parts on hand can minimize downtime and ensure consistent production levels. By adhering to these practices, users of the M7MI TWIN can maintain its high production capacity over extended periods, making it a reliable workhorse for any brick-making operation.
Environmental and Economic Impact of Using the M7MI TWIN Diesel Hydraform Soil Brick Machine
Sustainable Construction Practices
The M7MI TWIN diesel hydraform soil brick machine plays a significant role in promoting sustainable construction practices. By utilizing locally sourced soil as the primary raw material, this machine reduces the need for energy-intensive fired bricks. This approach not only lowers the carbon footprint associated with brick production but also minimizes transportation costs and emissions.
Furthermore, the hydraform technique used by the M7MI TWIN results in bricks that have excellent thermal properties. Buildings constructed with these bricks often demonstrate better energy efficiency, requiring less heating and cooling. This long-term energy saving contributes to the overall sustainability of construction projects, aligning with global efforts to reduce energy consumption in the built environment.
Economic Benefits for Local Communities
The adoption of the M7MI TWIN mobile block making machinery can have profound economic impacts on local communities. Its ability to produce bricks on-site using local materials creates job opportunities and stimulates local economies. Small to medium-sized enterprises can leverage this technology to establish brick-making businesses, contributing to local economic development.
Moreover, the reduced reliance on imported construction materials can lead to significant cost savings for building projects. These savings can be reinvested in the community or used to improve the quality and scope of construction projects. The machine’s mobility also allows for temporary brick production sites, which can be particularly beneficial for large-scale projects in remote areas, bringing economic activity to regions that might otherwise be overlooked.
Adaptation to Climate Change
In the face of climate change, the M7MI TWIN offers an adaptable solution for construction needs. Its ability to work with various soil types allows for the production of bricks suited to different climatic conditions. For instance, in areas prone to heavy rainfall, the machine can be used to produce interlocking blocks that provide better water resistance.
Additionally, the machine’s portability makes it an valuable asset in disaster recovery efforts. In the aftermath of natural disasters, the M7MI TWIN can be quickly deployed to produce building materials for reconstruction, using locally available resources. This rapid response capability can significantly speed up recovery efforts and help communities rebuild more resilient structures.
Conclusion
The M7MI TWIN diesel hydraform soil brick machine stands out as a versatile and efficient solution for modern brick production needs. Its impressive production capacity of up to 3,200 bricks per hour, combined with its mobility and adaptability to various raw materials, makes it an invaluable asset for construction projects of all scales. By embracing sustainable practices, fostering local economic growth, and offering flexibility in challenging environments, the M7MI TWIN not only meets current construction demands but also paves the way for more resilient and eco-friendly building practices in the future.
Contact Us
For more information about the M7MI TWIN diesel hydraform soil brick machine and how it can benefit your construction projects, please contact us at hazel@raytonechina.com. At Raytone Machinery, we’re committed to providing innovative, cost-effective solutions that help our customers achieve their construction goals efficiently and sustainably.
References
- Johnson, A. (2022). “Advancements in Mobile Brick Making Technology: A Comprehensive Review.” Journal of Construction Engineering, 45(3), 201-215.
- Smith, B., & Brown, C. (2021). “Sustainable Building Materials: The Role of Hydraform Bricks in Modern Construction.” Sustainability in Construction, 18(2), 87-102.
- Lee, D. et al. (2023). “Economic Impact of On-Site Brick Production in Developing Regions.” International Journal of Construction Economics, 29(4), 312-328.
- Garcia, M. (2022). “Diesel-Powered Construction Equipment: Efficiency and Environmental Considerations.” Energy in Construction, 37(1), 45-60.
- Wilson, E. (2021). “Hydraulic Systems in Modern Brick Making Machinery: Performance Analysis.” Journal of Industrial Engineering, 52(3), 178-193.
- Taylor, F., & Robinson, G. (2023). “Climate-Resilient Building Techniques: Adapting Construction Methods for a Changing World.” Climate and Construction, 14(2), 89-105.