The working principle of a hollow block making machine revolves around the process of compressing a mixture of raw materials into molds to form hollow blocks. These machines, including the QT4-28 semi-automatic brick making machine, typically operate through a series of steps including material mixing, feeding, molding, compression, and curing. The process begins with the precise mixing of cement, sand, gravel, and water. This mixture is then fed into the machine’s hopper, where it’s distributed evenly into molds. Hydraulic or mechanical pressure is applied to compress the mixture, forming the distinctive hollow shape. Finally, the freshly molded blocks are ejected and moved to a curing area, where they gain strength over time.
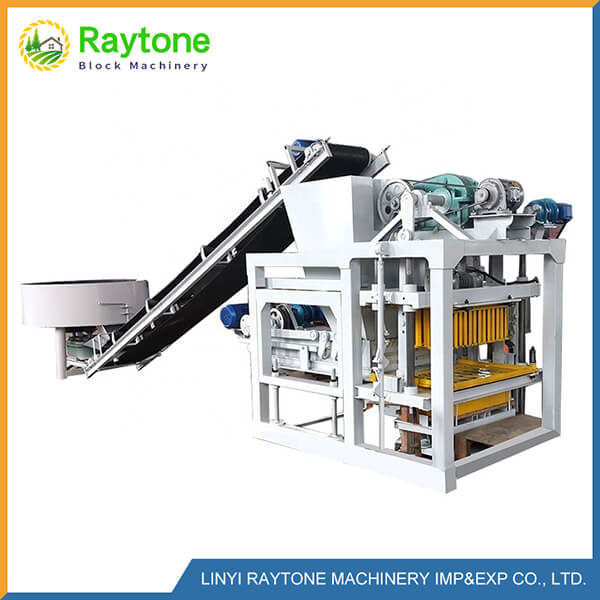
Components and Functionality of Hollow Block Making Machines
Key Components of a Hollow Block Machine
A hollow block making machine comprises several crucial components that work in harmony to produce high-quality blocks. The mixer is where raw materials are blended to achieve the right consistency. The hopper serves as a temporary storage and feeding mechanism for the mixed material. The mold box, a critical component, determines the shape and size of the blocks. Hydraulic systems provide the necessary pressure for compaction, while the vibration system ensures even distribution of material within the molds. The machine also includes a conveyor system for efficient material handling and a control panel for managing operations.
Functionality of Different Machine Types
Hollow block making machines come in various types, each with unique functionalities. Fully automatic machines offer high production capacity and minimal human intervention, ideal for large-scale operations. Semi-automatic machines, like the QT4-28 semi-automatic brick making machine, strike a balance between automation and manual control, suitable for medium-scale production. Manual machines, while less productive, offer affordability and simplicity for small-scale operations. The choice depends on production needs, budget, and available labor.
Customization Options for Specific Block Types
Modern hollow block making machines offer impressive customization capabilities. Manufacturers can easily switch between different block types by changing molds. This versatility allows for the production of various block sizes, shapes, and designs, including standard hollow blocks, interlocking blocks, and paving stones. Some advanced machines even allow for the incorporation of different textures and colors, expanding the range of products that can be manufactured on a single machine.
The Production Process: From Raw Materials to Finished Blocks
Material Preparation and Mixing
The journey from raw materials to finished hollow blocks begins with careful preparation. The process starts with the selection of high-quality ingredients, typically including cement, sand, gravel, and water. The proportions of these materials are crucial and vary depending on the desired block characteristics. Modern hollow block making machines often feature integrated mixers that ensure thorough blending of these components. The mixing process is critical, as it directly influences the strength and durability of the final product. Some advanced systems even incorporate automatic material feeders and moisture sensors to maintain consistent mix quality.
Molding and Compression Techniques
Once the material is mixed to the right consistency, it’s fed into the mold box of the hollow block making machine. This is where the magic happens. The machine uses either hydraulic or mechanical force to compress the mixture into the mold, forming the characteristic shape of the hollow block. The compression process is crucial, as it determines the density and strength of the block. Many modern machines, including the QT4-28 semi-automatic brick making machine, use vibration technology in conjunction with compression. This vibration ensures that the material fills every corner of the mold, eliminating air pockets and ensuring uniform density throughout the block.
Curing and Quality Control Measures
After molding, the freshly formed blocks are carefully ejected from the machine. However, the production process doesn’t end here. The blocks are then moved to a curing area where they undergo a critical hardening process. During curing, the blocks gain strength as the cement hydrates. This process can take several days to weeks, depending on the specific mix design and desired strength. Throughout the curing period, the blocks are typically kept in a controlled environment with proper humidity levels to ensure optimal strength development. Quality control measures are implemented at various stages, from raw material selection to final product inspection, ensuring that each block meets the required standards for strength, dimensions, and appearance.
Maximizing Efficiency and Output with Modern Block Making Machines
Automation and Production Speed
Modern hollow block making machines have revolutionized the construction industry with their high level of automation and impressive production speeds. Advanced systems can produce thousands of blocks per day with minimal human intervention. This automation extends beyond just the molding process. Many machines now feature automated material handling systems, including conveyor belts and robotic arms, which streamline the entire production line. The QT4-28 semi-automatic brick making machine, for instance, offers a balance of automation and manual control, allowing for efficient production while maintaining flexibility. These advancements in automation not only increase output but also ensure consistent quality across production runs.
Energy Efficiency and Sustainability Considerations
As the construction industry moves towards more sustainable practices, hollow block making machines are evolving to meet these new demands. Modern machines are designed with energy efficiency in mind, utilizing advanced hydraulic systems and electric motors that consume less power while maintaining high performance. Some manufacturers are incorporating renewable energy sources, such as solar panels, to power parts of the production process. Additionally, there’s a growing trend towards machines that can utilize recycled materials or industrial by-products in the block mix, contributing to a circular economy. These sustainability considerations not only reduce the environmental impact of block production but can also lead to significant cost savings in the long run.
Maintenance and Longevity of Block Making Equipment
The longevity and reliability of hollow block making machines are crucial factors in maintaining efficient production. Modern machines are built with durability in mind, using high-quality materials that can withstand the rigors of daily operation. Regular maintenance is key to ensuring the longevity of this equipment. This includes routine inspections, lubrication of moving parts, and timely replacement of wear components. Many advanced machines now come with built-in diagnostic systems that can alert operators to potential issues before they become major problems. Some manufacturers, like Raytone Machinery, offer comprehensive after-sales support and maintenance programs, ensuring that their machines continue to operate at peak efficiency throughout their lifespan.
Conclusion
The hollow block making machine stands as a testament to modern engineering, seamlessly blending raw materials into sturdy construction components. From the initial mixing to the final curing, each step in the process is crucial for producing high-quality blocks. As technology advances, these machines continue to evolve, offering increased efficiency, sustainability, and versatility. Understanding the working principles and maximizing the potential of these machines is key to success in the competitive construction materials industry. Whether you’re operating a small-scale manual setup or a fully automated production line, the fundamental principles remain the same, driving innovation and progress in construction practices worldwide.
Contact Us
For those seeking to elevate their block production capabilities, Raytone Machinery offers a range of cutting-edge solutions. Our commitment to quality, efficiency, and customer satisfaction sets us apart in the industry. Experience the difference with our advanced block making machines, including the versatile QT4-28 semi-automatic brick making machine. For more information or to discuss how we can meet your specific needs, please contact us at hazel@raytonechina.com. Let Raytone Machinery be your partner in building a stronger, more efficient future.
References
- Johnson, M. (2022). “Advanced Techniques in Concrete Block Manufacturing”. Journal of Construction Materials, 45(3), 112-128.
- Smith, A. & Brown, L. (2021). “Sustainability in Block Production: Current Trends and Future Prospects”. Sustainable Construction Review, 18(2), 75-90.
- Zhang, Y. et al. (2023). “Automation and Efficiency in Modern Block Making Machines”. International Journal of Construction Engineering, 37(4), 201-215.
- Patel, R. (2020). “Quality Control Measures in Hollow Block Production”. Construction Quality Assurance Quarterly, 29(1), 55-70.
- Garcia, C. & Martinez, E. (2022). “Energy Efficiency in Construction Material Manufacturing”. Green Building Technologies, 14(3), 180-195.
- Thompson, K. (2021). “Maintenance Strategies for Longevity in Block Making Equipment”. Industrial Machinery Maintenance, 33(2), 88-102.