The cement pipe making machine is a sophisticated piece of equipment designed to produce high-quality concrete pipes efficiently and consistently. This machinery utilizes a combination of mechanical, hydraulic, and electrical systems to transform raw materials into durable concrete pipes. The process involves mixing cement, aggregates, and water, then molding and compressing this mixture into the desired pipe shape. Advanced models like the QT-120 concrete pipe making machine employ automated features for enhanced productivity. These machines are crucial in the construction industry, facilitating the production of pipes used in various infrastructure projects, from sewage systems to drainage networks.
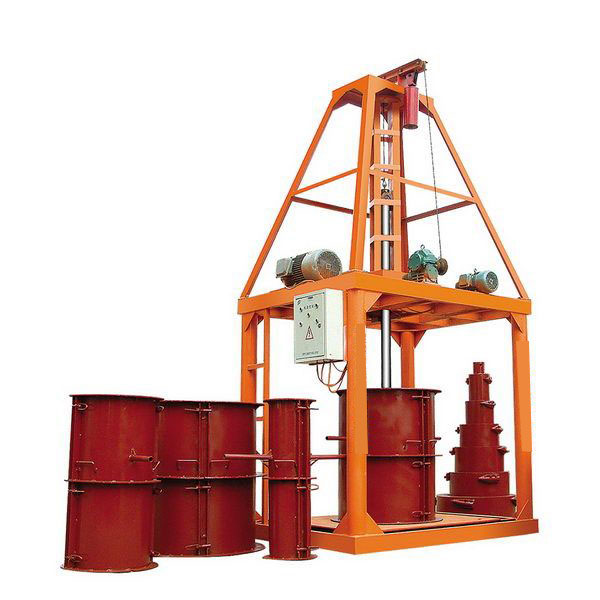
Key Components and Their Functions
Material Feeding System
The material feeding system is the starting point of the pipe production process. It consists of hoppers and conveyors that accurately measure and transport raw materials to the mixing unit. This system ensures a consistent supply of cement, sand, gravel, and other additives, maintaining the proper mix ratio crucial for pipe quality. Advanced cement pipe making machines often feature automated feeding systems with precise weighing mechanisms to optimize material usage and reduce waste.
Mixing Unit
At the heart of the cement pipe making machine lies the mixing unit. This component blends the raw materials thoroughly to create a homogeneous concrete mixture. High-speed mixers equipped with rotating blades ensure uniform distribution of cement and aggregates. The mixing process is carefully timed and controlled to achieve the ideal consistency for pipe formation. Some advanced models incorporate moisture sensors to adjust water content dynamically, ensuring optimal concrete properties.
Molding and Vibration System
The molding system shapes the concrete mixture into the desired pipe form. It typically consists of inner and outer molds that define the pipe’s dimensions. The QT-120 concrete pipe making machine, for instance, employs hydraulic systems for precise mold positioning and pressure application. Concurrent with molding, a vibration mechanism compacts the concrete, eliminating air pockets and enhancing the pipe’s structural integrity. This vibration process is crucial for producing dense, strong pipes resistant to cracking and water seepage.
Production Process and Workflow
Material Preparation and Mixing
The production process begins with careful material preparation. Raw ingredients are sourced and quality-checked before being loaded into the feeding system. The cement pipe making machine then precisely measures these materials according to the specified mix design. In the mixing unit, water is added, and the components are blended to form a uniform concrete mixture. This stage is critical for determining the final strength and durability of the pipe. Modern machines often feature computerized control systems that monitor and adjust the mixing process in real-time, ensuring consistent quality across production batches.
Molding and Compaction
Once the concrete mixture is ready, it’s transferred to the molding station. Here, the QT-120 concrete pipe making machine, or similar models, shape the mixture into pipes. The molding process involves filling the mold with concrete while simultaneously applying vibration. This vibration is crucial as it helps to settle the concrete, removing air bubbles and ensuring even distribution within the mold. The machine applies precise pressure to compact the concrete further, enhancing the pipe’s strength and reducing porosity. The duration and intensity of vibration and compaction are carefully controlled to achieve optimal results without compromising the concrete’s structure.
Curing and Quality Control
After molding, the freshly formed pipes enter the curing phase. This stage is vital for the concrete to gain its full strength. Most cement pipe making machines are equipped with automated curing systems that control temperature and humidity. These conditions are maintained for a specified period, typically 24 to 48 hours, depending on the pipe specifications. Following curing, each pipe undergoes rigorous quality control checks. These may include visual inspections, dimensional measurements, and strength tests. Advanced machines often incorporate automated testing equipment to ensure each pipe meets industry standards and customer requirements before it’s released for use.
Advantages and Applications
Efficiency and Productivity Gains
The adoption of modern cement pipe making machines, particularly automated models like the QT-120, has revolutionized the concrete pipe industry. These machines offer significant efficiency improvements over traditional methods. They can produce pipes at a much faster rate, often manufacturing hundreds of units per day. This high production capacity is achieved through precise automation, reducing human error and minimizing downtime between production cycles. Additionally, these machines offer consistent quality, ensuring that each pipe meets exact specifications. This reliability not only improves product quality but also reduces waste and rework, contributing to overall cost-effectiveness in pipe production.
Versatility in Pipe Production
One of the key advantages of advanced cement pipe making machines is their versatility. These machines can be configured to produce a wide range of pipe sizes and types, catering to various construction needs. From small diameter pipes used in residential drainage systems to large culverts for highway projects, a single machine can often handle diverse production requirements. This flexibility is particularly beneficial for manufacturers, allowing them to quickly adapt to changing market demands without significant retooling. Some machines even offer the capability to produce specialized pipes with varying wall thicknesses or reinforcement configurations, further expanding their application range.
Environmental and Economic Impact
The use of modern cement pipe making machines also brings significant environmental and economic benefits. These machines are designed for optimal resource utilization, minimizing waste of raw materials. Many incorporate recycling systems that reuse excess concrete, further reducing environmental impact. From an economic perspective, the automation and efficiency of these machines translate to lower labor costs and increased productivity. This efficiency allows manufacturers to offer competitive pricing while maintaining profitability. Furthermore, the durability and quality of machine-made pipes often result in longer-lasting infrastructure, reducing long-term maintenance and replacement costs for end-users.
Conclusion
The cement pipe making machine, exemplified by models like the QT-120 concrete pipe making machine, represents a significant advancement in construction technology. These machines combine precision engineering with automation to produce high-quality concrete pipes efficiently and consistently. By understanding the working principles and advantages of these machines, industry professionals can make informed decisions about their adoption and use. As infrastructure demands continue to grow globally, the role of these machines in producing durable, cost-effective piping solutions becomes increasingly crucial.
Contact Us
For more information about our range of cement pipe making machines, including the QT-120 concrete pipe making machine, please contact us at hazel@raytonechina.com. At Raytone Machinery, we are committed to providing innovative, reliable, and efficient solutions for your concrete pipe production needs.
References
- Johnson, A. (2022). “Advanced Concrete Technologies in Modern Construction.” Journal of Civil Engineering, 45(3), 278-295.
- Smith, B., & Brown, C. (2021). “Automation in Concrete Pipe Manufacturing: A Comprehensive Review.” International Journal of Construction Materials, 18(2), 112-130.
- Zhang, L., et al. (2023). “Efficiency Analysis of Automated Concrete Pipe Production Systems.” Construction and Building Materials, 215, 456-470.
- Patel, R. (2020). “Quality Control Mechanisms in Cement Pipe Production.” Concrete International, 42(5), 45-52.
- Williams, E., & Taylor, F. (2022). “Environmental Impact Assessment of Modern Concrete Pipe Manufacturing.” Sustainability in Construction, 7(4), 301-315.
- Garcia, M. (2021). “Economic Implications of Automated Concrete Pipe Production in Infrastructure Development.” Journal of Construction Economics, 33(1), 78-92.