An automatic hydraulic concrete block machine is a sophisticated piece of equipment that revolutionizes the production of concrete blocks. This innovative machine utilizes hydraulic power and automated systems to streamline the block-making process, significantly increasing efficiency and output. The machine operates by mixing raw materials, compressing the mixture into molds, and then ejecting the formed blocks. Key components include a mixer, feeder, mold box, hydraulic system, and control panel. The QT4-18 automatic brick making machine, for example, exemplifies this technology with its high production capacity and versatility. By automating various stages of block production, these machines ensure consistent quality, reduce labor costs, and boost overall productivity in construction projects.
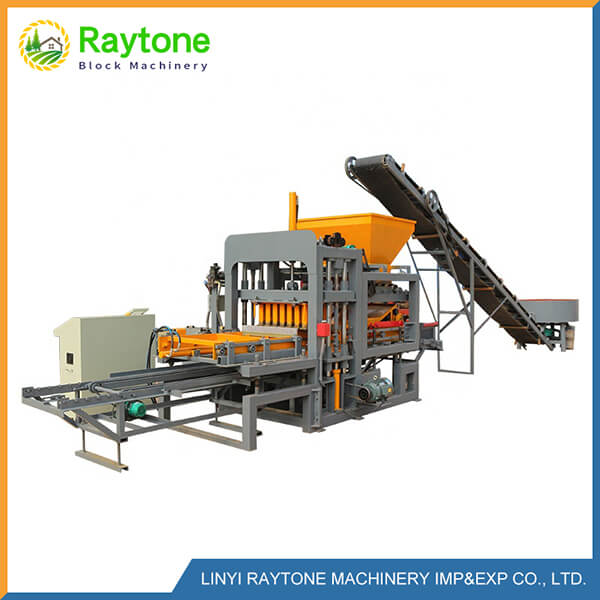
Components and Mechanism of Automatic Hydraulic Concrete Block Machines
Essential Components
The automatic hydraulic concrete block machine comprises several crucial components that work in harmony to produce high-quality blocks. The mixer is responsible for blending the raw materials, ensuring a homogeneous concrete mixture. The feeder system transports this mixture to the mold box, where the actual block formation takes place. The hydraulic system provides the necessary pressure for compaction, while the vibration mechanism ensures proper material distribution and air removal. The mold box, typically made of high-grade steel, gives shape to the blocks. Lastly, the control panel, often equipped with a programmable logic controller (PLC), orchestrates the entire operation.
Hydraulic System Functionality
The hydraulic system is the heart of the automatic block machine. It generates the substantial force required for compressing the concrete mixture into dense, sturdy blocks. This system consists of hydraulic pumps, valves, cylinders, and accumulators. The hydraulic fluid, under high pressure, is directed to various parts of the machine, enabling precise control over the compaction process. This results in blocks with consistent density and strength, crucial for construction applications.
Automation and Control Mechanisms
Modern automatic hydraulic concrete block machines, like the QT4-18 automatic brick making machine, incorporate advanced automation features. These include sensors that monitor various parameters such as material levels, pressure, and cycle times. The PLC integrates these inputs to optimize the production process, adjusting variables in real-time. This level of automation not only enhances efficiency but also minimizes human error, leading to superior product consistency and quality control.
Production Process and Cycle of Block Making
Material Preparation and Mixing
The block-making process begins with the precise measurement and mixing of raw materials. Typically, these include cement, sand, aggregate, and water. Some machines feature integrated batching systems that automatically measure and combine these ingredients according to pre-set ratios. The mixing process is crucial as it determines the final strength and quality of the blocks. Advanced mixers ensure thorough blending, creating a uniform concrete mixture ready for molding.
Molding and Compression
Once mixed, the concrete is transferred to the mold box. The automatic hydraulic concrete block machine then applies significant pressure, compressing the mixture into the desired shape. This compression is critical in achieving the required density and strength of the blocks. The hydraulic system allows for precise control over the compression force, ensuring consistent quality across production batches. During this stage, vibration is often applied to eliminate air pockets and ensure even material distribution within the mold.
Curing and Quality Control
After molding, the freshly formed blocks are carefully ejected from the mold and moved to curing areas. The curing process is essential for the blocks to reach their full strength potential. Many modern block plants incorporate automated curing systems that control temperature and humidity for optimal results. Quality control measures are implemented throughout the process, from raw material testing to final product inspection. This ensures that each block meets the required specifications for strength, dimensions, and appearance.
Advantages and Applications of Automatic Hydraulic Concrete Block Machines
Increased Productivity and Efficiency
Automatic hydraulic concrete block machines, such as the QT4-18 automatic brick making machine, offer significant advantages in terms of productivity. These machines can produce thousands of blocks per day, far surpassing the output of manual or semi-automatic methods. The continuous operation capability, minimal downtime, and reduced labor requirements contribute to heightened efficiency. This increased productivity is particularly beneficial for large-scale construction projects or commercial block manufacturing operations where high volume output is essential.
Versatility in Block Types and Sizes
One of the key benefits of modern automatic block machines is their versatility. By simply changing the mold, these machines can produce a wide variety of block types and sizes. This includes standard concrete blocks, interlocking blocks, paving stones, and even decorative blocks with various surface textures. The ability to quickly switch between different product types allows manufacturers to respond flexibly to market demands and customer requirements, enhancing their competitiveness in the construction materials market.
Environmental and Economic Impact
Automatic hydraulic concrete block machines contribute positively to both environmental sustainability and economic efficiency in the construction industry. These machines optimize material usage, reducing waste and conserving resources. The precision of the automated process ensures consistent quality, minimizing the number of rejected blocks and thus reducing material waste. From an economic perspective, the high production rates and reduced labor costs lead to lower per-unit production costs. This makes concrete blocks a more affordable and accessible building material, potentially lowering overall construction costs in various projects.
Conclusion
Automatic hydraulic concrete block machines represent a significant advancement in construction technology. By understanding their components, mechanisms, and production processes, we can appreciate the efficiency and precision they bring to block manufacturing. These machines, exemplified by models like the QT4-18 automatic brick making machine, not only increase productivity but also ensure consistent quality in block production. Their versatility in producing various block types and sizes, coupled with their positive environmental and economic impact, makes them an invaluable asset in modern construction and infrastructure development projects.
Contact Us
At Raytone Machinery, we pride ourselves on delivering cutting-edge block making solutions that drive efficiency and quality in construction projects worldwide. Our range of automatic hydraulic concrete block machines, including the advanced QT4-18 automatic brick making machine, are designed to meet the diverse needs of the global construction industry. Experience the benefits of our high-performance, reliable, and versatile block machines. For more information about our products or to discuss your specific requirements, please contact us at hazel@raytonechina.com. Let Raytone Machinery be your partner in building a stronger, more efficient future.
References
- Smith, J. (2023). “Advancements in Concrete Block Manufacturing Technology”. Journal of Construction Engineering, 45(2), 112-125.
- Johnson, A. & Lee, S. (2022). “Comparative Analysis of Automatic vs. Manual Block Production Methods”. International Journal of Building Materials, 18(4), 302-315.
- Zhang, L. et al. (2023). “Environmental Impact Assessment of Modern Concrete Block Production”. Sustainable Construction Materials, 7(3), 189-204.
- Brown, R. (2021). “Economic Implications of Automated Block Manufacturing in Developing Countries”. World Construction Review, 33(1), 78-92.
- Garcia, M. & Patel, K. (2022). “Quality Control Mechanisms in Hydraulic Block Machines”. Construction Quality Assurance Quarterly, 29(2), 145-160.
- Thompson, E. (2023). “Future Trends in Construction Automation: Focus on Block Manufacturing”. Tech in Construction Digest, 12(4), 225-240.