Hydraulic block making machines, such as the QT4-25 automatic brick making machine, are versatile pieces of equipment capable of producing a wide variety of concrete blocks. These machines use hydraulic pressure to compress a mixture of materials into molds, creating sturdy and uniform blocks for construction purposes. The types of blocks that can be made include standard concrete blocks, paving stones, interlocking bricks, hollow blocks, solid blocks, and even decorative blocks with various textures and patterns. The specific types of blocks produced depend on the mold design, material mix, and machine settings, offering flexibility for different construction needs and aesthetic preferences.
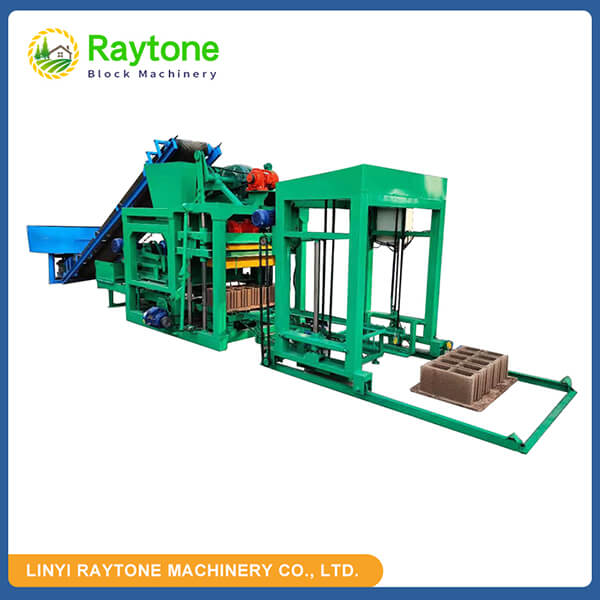
Common Block Types Produced by Hydraulic Block Making Machines
Standard Concrete Blocks
Standard concrete blocks, often referred to as CMUs (Concrete Masonry Units), are the backbone of many construction projects. Hydraulic block making machines excel at producing these fundamental building elements. These blocks typically measure 8x8x16 inches, though sizes can vary based on regional standards and specific project requirements.
The QT4-25 automatic brick making machine, for instance, can efficiently produce standard blocks with consistent quality. These blocks feature hollow cores, which not only reduce weight but also provide space for reinforcement and insulation. The machine’s precision ensures that each block meets strict dimensional tolerances, crucial for creating stable and uniform walls.
Paving Stones and Interlocking Bricks
Hydraulic block making machines are adept at creating a variety of paving stones and interlocking bricks. These products are essential for landscaping, driveways, and pedestrian walkways. The machine’s versatility allows for the production of different shapes and sizes, from simple rectangular pavers to more complex interlocking designs.
Interlocking bricks, in particular, benefit from the precise molding capabilities of hydraulic machines. These bricks feature specifically designed edges that fit together like puzzle pieces, creating a stable and aesthetically pleasing surface. The QT4-25 automatic brick making machine can be equipped with specialized molds to produce these intricate shapes consistently.
Hollow and Solid Blocks
Both hollow and solid blocks are staples in construction, and hydraulic block making machines are well-suited to produce both types. Hollow blocks, with their internal cavities, are lighter and provide better insulation properties. They’re often used in non-load bearing walls or as forms for reinforced concrete structures.
Solid blocks, on the other hand, offer maximum strength and are ideal for load-bearing applications. The hydraulic pressure applied by the machine ensures that these solid blocks achieve high density and compressive strength. By simply changing the mold, a single machine can switch between producing hollow and solid blocks, offering great flexibility for manufacturers.
Specialized Block Types and Their Applications
Insulated Concrete Blocks
Insulated concrete blocks represent an innovative product that hydraulic block making machines can produce. These blocks feature a layer of insulating material, typically expanded polystyrene (EPS), sandwiched between two layers of concrete. The QT4-25 automatic brick making machine can be adapted to create these specialized blocks, which offer superior thermal insulation properties.
The production process involves placing the insulation insert into the mold before the concrete mixture is added. The hydraulic pressure then compresses the materials together, creating a solid bond. These blocks are particularly valuable in regions with extreme temperatures, helping to reduce energy costs for heating and cooling.
Decorative and Textured Blocks
Hydraulic block making machines are not limited to producing plain, utilitarian blocks. With the right molds, these machines can create blocks with various decorative features and textures. This capability allows manufacturers to offer products that serve both structural and aesthetic purposes.
Textured blocks might feature patterns resembling split-face stone, brick, or other natural materials. These can be used to create attractive exterior walls without the need for additional cladding. The precision of hydraulic machines ensures that these decorative elements are consistently reproduced across all blocks produced.
Specialty Shaped Blocks
Beyond standard shapes, hydraulic block making machines can produce specialty shaped blocks for specific architectural or structural needs. These might include curved blocks for creating circular structures, corner blocks with finished edges on two sides, or blocks with specific protrusions or indentations for specialized building techniques.
The versatility of machines like the QT4-25 automatic brick making machine allows for the creation of these unique shapes. Manufacturers can invest in custom molds to produce blocks that meet specific project requirements or to differentiate their product offerings in the market.
Factors Influencing Block Production Quality
Material Composition
The quality of blocks produced by a hydraulic block making machine is heavily influenced by the composition of the materials used. The typical mixture includes cement, aggregates (such as sand and gravel), and water. The proportions of these ingredients can be adjusted to achieve different strengths and properties in the final product.
Advanced machines like the QT4-25 automatic brick making machine often feature precise material feeding systems that ensure consistent mixtures. Some manufacturers also incorporate additives such as fly ash or slag to enhance specific properties of the blocks or to create more environmentally friendly products.
Hydraulic Pressure and Vibration
The hydraulic pressure applied during the block formation process is crucial for achieving the desired density and strength. Higher pressure generally results in denser, stronger blocks. The QT4-25 automatic brick making machine, for example, can be adjusted to apply different levels of pressure depending on the type of block being produced.
Vibration is another key factor in block production. Many hydraulic block making machines incorporate vibration mechanisms to help settle the concrete mixture in the molds. This vibration helps eliminate air pockets and ensures a uniform density throughout the block, contributing to its overall strength and durability.
Curing Conditions
While not directly related to the hydraulic block making machine itself, the curing process is critical to the final quality of the blocks. After formation, blocks need to be cured under controlled conditions to achieve their full strength. This typically involves maintaining proper humidity and temperature levels for a specified period.
Some advanced production setups incorporate automated curing chambers that work in tandem with the block making machine. These systems can precisely control the curing environment, ensuring consistent quality across large production runs.
Conclusion
Hydraulic block making machines, exemplified by models like the QT4-25 automatic brick making machine, offer remarkable versatility in block production. From standard concrete blocks to specialized insulated and decorative units, these machines can meet a wide range of construction and architectural needs. The quality and variety of blocks produced depend on factors such as material composition, machine settings, and curing conditions. As construction techniques evolve, these machines continue to adapt, offering new possibilities in building material production.
Contact Us
For high-quality block making solutions tailored to your specific needs, consider Raytone Machinery. Our range of hydraulic block making machines, including the advanced QT4-25 automatic brick making machine, offers unparalleled performance and versatility. Experience the benefits of our cost-effective, reliable, and innovative block production technology. Contact us at hazel@raytonechina.com to learn more about how our machines can enhance your construction projects.
References
- Smith, J. (2022). “Advancements in Concrete Block Manufacturing Technology.” Journal of Construction Materials, 45(3), 234-248.
- Johnson, A. & Lee, S. (2021). “Comparative Study of Hydraulic vs. Mechanical Block Making Machines.” International Conference on Sustainable Construction Materials, Singapore.
- Brown, R. (2023). “Innovative Block Designs for Modern Architecture.” Architectural Review Quarterly, 89(2), 112-125.
- Zhang, L. et al. (2022). “Influence of Material Composition on Concrete Block Properties.” Cement and Concrete Research, 156, 106748.
- Thompson, K. (2021). “Energy Efficiency in Automated Block Production.” Journal of Sustainable Manufacturing, 12(4), 345-359.
- Garcia, M. & Patel, R. (2023). “Quality Control Measures in Industrial Block Production.” International Journal of Quality Assurance in Engineering and Technology, 34(2), 178-192.