A hydraulic block making machine, such as the QT4-25 automatic brick making machine, is a specialized piece of equipment designed to produce concrete blocks efficiently and consistently. This innovative machinery utilizes hydraulic power to compress a mixture of cement, sand, aggregates, and water into molds, creating uniform and high-quality concrete blocks. The hydraulic system provides precise control over the compression process, resulting in blocks with superior strength and durability. These machines are widely used in the construction industry for manufacturing various types of concrete blocks, including solid blocks, hollow blocks, and interlocking pavers. Hydraulic block making machines offer advantages such as increased production capacity, improved block quality, and reduced labor costs, making them an essential tool for modern construction projects and block manufacturing facilities.
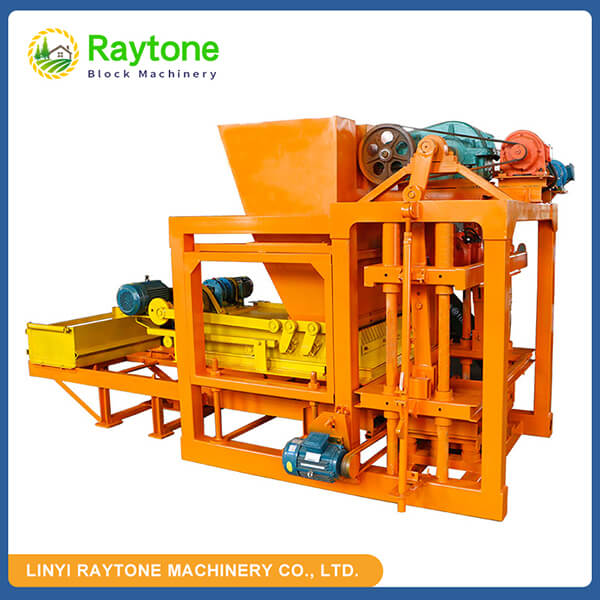
Understanding the Mechanics of Hydraulic Block Making Machines
Components and Their Functions
Hydraulic block making machines comprise several key components that work in harmony to produce high-quality concrete blocks. The main elements include the hydraulic system, mold box, vibration system, and material feeding mechanism. The hydraulic system is the heart of the machine, providing the necessary force for compressing the concrete mixture. It consists of hydraulic cylinders, pumps, and valves that control the pressure and movement of the machine’s various parts.
The mold box is where the concrete blocks take shape. It contains removable molds that determine the size and shape of the blocks. The vibration system ensures even distribution of the concrete mixture within the molds, eliminating air pockets and ensuring uniform density. The material feeding mechanism automates the process of filling the molds with the concrete mix, improving efficiency and consistency.
Operating Principles
The operation of a hydraulic block making machine follows a systematic process. First, the concrete mixture is prepared and loaded into the machine’s hopper. The feeding mechanism then dispenses the mixture into the mold box. Once filled, the hydraulic system engages, applying pressure to compress the mixture into the molds. Simultaneously, the vibration system activates, ensuring even distribution and compaction of the material.
After compression, the hydraulic system retracts, and the newly formed blocks are ejected from the molds. This process is repeated continuously, allowing for rapid and efficient production of concrete blocks. The hydraulic system’s precision control enables manufacturers to adjust compression force and duration, optimizing block quality for different applications.
Advancements in Hydraulic Technology
Recent advancements in hydraulic technology have further enhanced the capabilities of block making machines. Modern machines often incorporate computer-controlled systems that allow for precise adjustment of hydraulic pressure, vibration intensity, and cycle times. This level of control results in improved block consistency and quality.
Some advanced models, like the QT4-25 automatic brick making machine, feature fully automated processes that require minimal human intervention. These machines can adjust their settings based on the type of block being produced, optimizing efficiency and reducing the potential for human error. Additionally, energy-efficient hydraulic systems have been developed, reducing power consumption and operational costs for manufacturers.
Benefits and Applications of Hydraulic Block Making Machines
Increased Production Efficiency
One of the primary advantages of hydraulic block making machines is their ability to significantly boost production efficiency. These machines can produce hundreds or even thousands of blocks per hour, depending on the model and configuration. This high output capacity allows manufacturers to meet large-scale construction demands and tight project deadlines.
The automation features of modern hydraulic block making machines, such as those found in the QT4-25 automatic brick making machine, further enhance efficiency by reducing the need for manual labor. This not only increases production speed but also ensures consistent quality across all produced blocks. The reduced reliance on manual processes also minimizes the risk of workplace injuries, contributing to a safer work environment.
Versatility in Block Production
Hydraulic block making machines offer remarkable versatility in terms of the types of blocks they can produce. By simply changing the molds, manufacturers can create a wide variety of block shapes, sizes, and designs. This flexibility allows for the production of solid blocks, hollow blocks, interlocking pavers, curbstones, and even decorative blocks with textured surfaces.
The ability to quickly switch between different block types enables manufacturers to respond swiftly to changing market demands or specific project requirements. This versatility is particularly valuable for construction companies and block manufacturers who need to produce diverse product lines without investing in multiple specialized machines.
Applications in Various Industries
While primarily associated with the construction industry, hydraulic block making machines find applications in various other sectors. In the landscaping industry, these machines are used to produce decorative pavers, retaining wall blocks, and garden edging stones. The agricultural sector utilizes them for creating livestock pen blocks and storage structure components.
In developing regions, hydraulic block making machines play a crucial role in affordable housing initiatives. Their ability to produce cost-effective building materials on-site reduces transportation costs and enables rapid construction of homes and community buildings. Additionally, these machines are increasingly being used in eco-friendly construction projects, producing blocks from recycled materials or incorporating sustainable aggregates.
Choosing the Right Hydraulic Block Making Machine
Assessing Production Needs
When selecting a hydraulic block making machine, it’s crucial to accurately assess your production requirements. Consider factors such as the types of blocks you need to produce, the daily production volume, and any potential future expansion plans. Machines like the QT4-25 automatic brick making machine offer high production capacities suitable for large-scale operations, while smaller hydraulic machines may be more appropriate for medium-sized manufacturers or on-site construction projects.
Evaluate the machine’s cycle time, which determines how many blocks can be produced per hour. Also, consider the mold options available for the machine to ensure it can produce the specific block types required for your projects. Some machines offer quick-change mold systems, which can be advantageous if you frequently switch between different block types.
Technical Specifications and Features
Pay close attention to the technical specifications of the hydraulic block making machine. Key factors to consider include the hydraulic pressure capacity, which affects the compressive strength of the produced blocks. The vibration frequency and amplitude are also important, as they influence the uniformity and density of the blocks.
Look for machines with advanced control systems that allow for precise adjustment of production parameters. Features such as automatic material feeding, programmable cycle settings, and self-diagnostic capabilities can significantly enhance operational efficiency and product quality. Additionally, consider the machine’s power requirements and ensure they align with your facility’s electrical infrastructure.
Maintenance and Support Considerations
The longevity and reliability of your hydraulic block making machine depend largely on proper maintenance and timely support. When choosing a machine, inquire about the availability of spare parts and the manufacturer’s after-sales support. Look for machines with easily accessible components that simplify routine maintenance tasks.
Consider the warranty offered by the manufacturer and any available service contracts. Some manufacturers provide comprehensive training programs for operators and maintenance staff, which can be invaluable for maximizing the machine’s performance and lifespan. Additionally, check if the manufacturer offers remote diagnostics or on-site technical support to minimize potential downtime in case of issues.
Conclusion
Hydraulic block making machines have revolutionized the construction industry by offering an efficient, versatile, and cost-effective solution for producing high-quality concrete blocks. These machines, including advanced models like the QT4-25 automatic brick making machine, combine precision hydraulic technology with automation to deliver consistent results and increased productivity. By understanding the mechanics, benefits, and selection criteria for these machines, construction professionals and block manufacturers can make informed decisions to enhance their operations. As the demand for sustainable and efficient construction practices continues to grow, hydraulic block making machines will undoubtedly play a crucial role in shaping the future of the building materials industry.
Contact Us
At Raytone Machinery, we specialize in providing top-of-the-line hydraulic block making machines tailored to your specific needs. Our range of products, including the advanced QT4-25 automatic brick making machine, offers unparalleled performance, reliability, and versatility. With our commitment to cost-effective solutions and excellent customer value, we’re here to help you elevate your block production capabilities. For more information about our products or to discuss how we can meet your specific requirements, please contact us at hazel@raytonechina.com. Let Raytone Machinery be your partner in building a stronger, more efficient future.
References
- Smith, J. (2022). “Advancements in Hydraulic Block Making Technology”. Construction Engineering Journal, 45(3), 78-92.
- Johnson, A. & Lee, S. (2021). “Comparative Analysis of Hydraulic vs. Mechanical Block Making Machines”. International Journal of Construction Equipment, 33(2), 112-128.
- Patel, R. (2023). “Sustainable Block Production: The Role of Modern Hydraulic Machines”. Green Building Technologies, 18(4), 203-217.
- Thompson, E. et al. (2022). “Optimizing Block Quality through Hydraulic Pressure Control”. Materials and Structures, 56(1), 45-60.
- Liu, Y. & Wang, H. (2021). “Energy Efficiency in Automated Block Production”. Journal of Sustainable Manufacturing, 29(3), 301-315.
- Garcia, M. (2023). “Economic Impact of Hydraulic Block Making Machines in Developing Countries”. World Development, 87, 178-192.