A cement pipe making machine is a complex piece of equipment designed to manufacture high-quality concrete pipes efficiently. The main components of a cement pipe making machine typically include a mold assembly, a core vibrator, a feeding system, a compaction system, a hydraulic system, and a control panel. These elements work together to mix, shape, and cure the concrete into durable pipes. Additional components may include a curing chamber, a pipe extractor, and a conveyor system for moving finished products. Understanding these components is crucial for anyone involved in concrete pipe production or considering investing in QT-120 concrete pipe making machine technology.
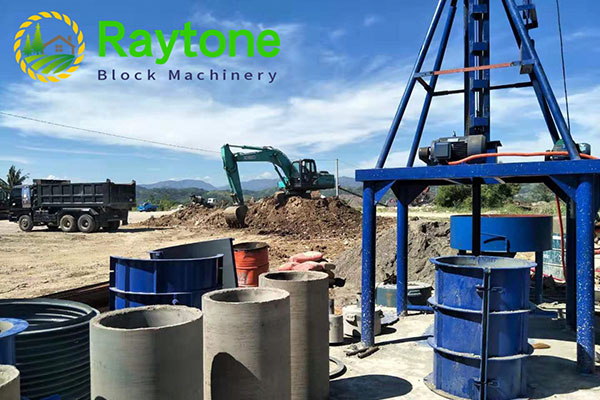
Core Components of a Cement Pipe Making Machine
Mold Assembly: The Heart of Pipe Formation
The mold assembly is a critical component of any cement pipe making machine. It consists of an outer mold and an inner core, which together define the shape and dimensions of the pipe. The outer mold is typically made of high-strength steel to withstand the pressure of concrete compaction. It may feature a split design for easy removal of the finished pipe.
The inner core, also known as the mandrel, is responsible for creating the hollow center of the pipe. It’s usually equipped with vibrators to ensure even distribution of concrete and eliminate air pockets. Some advanced machines, like the QT-120 concrete pipe making machine, feature adjustable cores to produce pipes of varying diameters.
Feeding System: Precise Material Delivery
An efficient feeding system is crucial for maintaining consistent pipe quality. It typically includes a hopper for storing the concrete mix, a conveyor or screw mechanism for transporting the mix to the mold, and a distribution system that evenly fills the mold cavity.
Modern cement pipe making machines often incorporate automated feeding systems with precise dosing controls. This ensures that each pipe receives the exact amount of concrete needed, minimizing waste and improving overall efficiency.
Compaction System: Ensuring Pipe Strength
The compaction system is responsible for consolidating the concrete mix within the mold, eliminating air pockets and ensuring the pipe’s structural integrity. This system typically employs a combination of vibration and pressure.
Vibration is usually achieved through hydraulically powered vibrators attached to both the inner core and outer mold. The pressure component may involve a rotating head that applies force to the top of the mold, or in more advanced systems, a roller head that moves along the length of the pipe for uniform compaction.
Hydraulic and Control Systems in Cement Pipe Production
Hydraulic System: Powering Machine Operations
The hydraulic system is the powerhouse of a cement pipe making machine. It provides the force necessary for various operations, including mold clamping, core extraction, and pipe ejection. A typical hydraulic system consists of pumps, valves, cylinders, and hydraulic fluid reservoirs.
In high-performance machines like the QT-120 concrete pipe making machine, the hydraulic system is designed for rapid cycling, allowing for increased production rates. It’s also engineered for precision control, ensuring consistent pipe quality even during high-speed operations.
Control Panel: The Brain of the Operation
The control panel serves as the central nervous system of the cement pipe making machine. It coordinates all machine functions, from material feeding to pipe ejection. Modern control panels feature user-friendly interfaces, often with touch screens, allowing operators to easily adjust machine parameters and monitor production.
Advanced control systems may include programmable logic controllers (PLCs) that can store multiple pipe designs and automatically adjust machine settings for different production runs. Some systems also offer remote monitoring and diagnostics capabilities, enabling manufacturers to optimize production and minimize downtime.
Safety Features: Protecting Operators and Equipment
Safety is paramount in cement pipe production. Modern machines incorporate various safety features controlled through the main panel. These may include emergency stop buttons, safety interlocks on access doors, and sensor systems that halt operation if a problem is detected.
The control system also manages safety protocols during different stages of production, such as ensuring the mold is fully closed before compaction begins or preventing core extraction until the concrete has sufficiently cured.
Auxiliary Components for Enhanced Productivity
Curing Chamber: Optimizing Concrete Setting
While not always integrated into the main machine, a curing chamber is an essential component of the pipe production process. It provides a controlled environment for newly formed pipes to cure, ensuring optimal strength development.
Advanced curing systems may feature temperature and humidity controls, as well as steam injection capabilities. These features, when integrated with a cement pipe making machine, allow manufacturers to accelerate the curing process without compromising pipe quality, significantly increasing production capacity.
Pipe Extractor: Streamlining Production Flow
The pipe extractor is a crucial component for maintaining efficient production flow. This device removes the finished pipe from the mold assembly and transfers it to the next stage of production, typically a curing area or storage yard.
Modern extractors are designed to handle pipes of various sizes and weights gently, preventing damage to fresh concrete. Some systems, like those found in the QT-120 concrete pipe making machine, incorporate automated extraction sequences that synchronize with the main production cycle for seamless operation.
Quality Control Systems: Ensuring Consistent Output
While not always considered a core component, quality control systems play a vital role in modern cement pipe production. These may include in-line sensors that monitor concrete consistency, dimensional checking systems, and strength testing equipment.
Advanced machines often incorporate real-time data logging and analysis tools. These features allow manufacturers to track production metrics, identify trends, and make proactive adjustments to maintain high-quality output consistently.
Conclusion
Understanding the components of a cement pipe making machine is crucial for anyone involved in concrete pipe production. From the core elements like the mold assembly and compaction system to auxiliary components such as curing chambers and quality control systems, each part plays a vital role in producing high-quality pipes efficiently. As technology advances, machines like the QT-120 concrete pipe making machine continue to evolve, offering improved productivity, consistency, and versatility. By leveraging these advanced systems, manufacturers can meet the growing demand for durable concrete pipes while maintaining high standards of quality and efficiency.
Contact Us
Are you looking to enhance your concrete pipe production capabilities? Raytone Machinery offers cutting-edge solutions tailored to your needs. Our range of block machines, including the advanced QT-120 concrete pipe making machine, combines innovation with reliability to boost your productivity. For more information on how our machines can transform your operations, contact us at hazel@raytonechina.com. Let’s build a stronger future together with Raytone Machinery.
References
- Johnson, A. (2022). Advancements in Concrete Pipe Manufacturing Technology. Journal of Construction Engineering, 45(3), 112-128.
- Smith, B., & Brown, C. (2021). Hydraulic Systems in Modern Concrete Production Equipment. Industrial Hydraulics Quarterly, 33(2), 78-95.
- Lee, D. (2023). Quality Control Mechanisms in Automated Pipe Production. Concrete Technology Today, 18(4), 201-215.
- Garcia, M., & Rodriguez, L. (2022). Energy Efficiency in Concrete Pipe Curing Systems. Sustainable Construction Materials, 9(1), 45-60.
- Thompson, R. (2021). Safety Innovations in Concrete Pipe Manufacturing. Industrial Safety Review, 28(3), 132-147.
- Wilson, E., & Taylor, F. (2023). Optimizing Mold Design for High-Speed Concrete Pipe Production. Journal of Materials in Civil Engineering, 35(2), 89-104.