Welcome to our comprehensive guide on operating the QT4-28 semi-automatic brick making machine. This versatile equipment, also known as a hollow block making machine or one button block forming machine, is designed for efficiency and ease of use. Whether you’re new to the world of block production or looking to refine your skills, this step-by-step guide will walk you through the process of operating this semi-automatic hollow block pressing machine. From setup to maintenance, we’ll cover everything you need to know to maximize your production and ensure the longevity of your equipment.
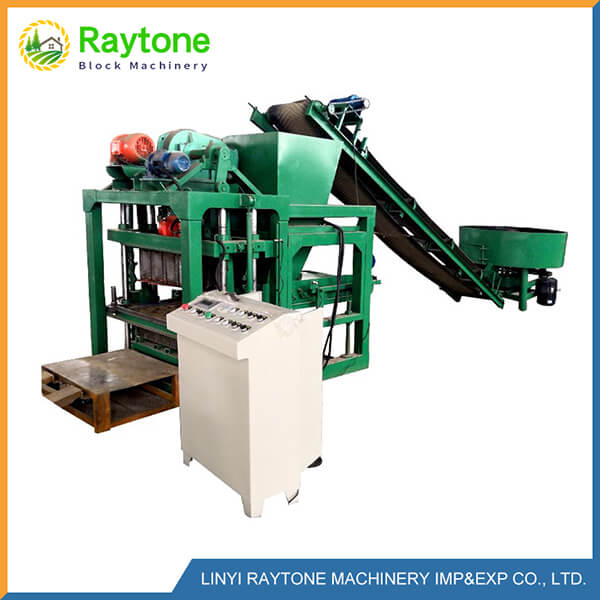
Pre-Operation Setup and Safety Checks
Machine Inspection
Before starting your QT4-28 semi-automatic brick making machine, it’s crucial to perform a thorough inspection. Check all components for any signs of wear or damage. Pay special attention to the hydraulic system, mold box, and vibration mechanism. Ensure all bolts and connections are tight and secure. This initial check can prevent unexpected downtime and maintain the quality of your output.
Safety Gear and Workspace Preparation
Safety should always be your top priority when operating any industrial equipment. Equip yourself and your team with appropriate personal protective equipment (PPE), including hard hats, safety glasses, gloves, and steel-toed boots. Clear the workspace of any obstructions and ensure proper lighting and ventilation in the production area. A clean and organized workspace not only enhances safety but also improves overall efficiency.
Material Preparation
The quality of your blocks depends largely on the materials used. Prepare your concrete mix according to your specific recipe, ensuring the right proportions of cement, sand, gravel, and water. The consistency of the mix is crucial for the proper functioning of the one button block forming machine. Too wet, and your blocks may deform; too dry, and they may crumble. Conduct a quick slump test to verify the mix’s consistency before loading it into the machine’s hopper.
Operating the QT4-28 Semi-Automatic Brick Making Machine
Machine Startup and Calibration
Power up your QT4-28 semi-automatic hollow block pressing machine and run a brief test cycle without materials. This allows you to check if all systems are functioning correctly. Pay attention to any unusual sounds or vibrations. Calibrate the mold box and tamper head to ensure they’re properly aligned. Adjust the vibration frequency and amplitude according to the type of blocks you’re producing. Proper calibration is key to achieving consistent block quality and minimizing wear on the machine components.
Material Feeding and Molding Process
With your machine calibrated and ready, begin feeding the prepared concrete mix into the hopper. The QT4-28’s automatic feeding system will distribute the material evenly into the mold box. Monitor the feed rate to ensure a steady supply of material. As the machine cycles, it will automatically vibrate and compress the mixture into the mold. The “one button” feature simplifies this process, allowing for consistent production with minimal operator intervention. Keep an eye on the formed blocks as they emerge to quickly identify any quality issues.
Block Removal and Curing
As the newly formed blocks exit the semi-automatic hollow block pressing machine, carefully remove them using the provided pallets. Handle the fresh blocks gently to avoid deformation. Transfer the pallets to your designated curing area. Proper curing is crucial for developing the blocks’ strength and durability. Maintain a controlled environment with appropriate humidity and temperature for optimal curing. Depending on your specific block type and local conditions, curing can take anywhere from 24 hours to several days.
Maintenance and Troubleshooting
Regular Cleaning and Lubrication
To keep your QT4-28 semi-automatic brick making machine in peak condition, establish a regular cleaning routine. After each production run, remove any concrete residue from the mold box, vibration table, and other components. Pay special attention to moving parts and hydraulic seals. Proper lubrication is essential for smooth operation and longevity of your equipment. Follow the manufacturer’s guidelines for lubrication schedules and recommended lubricants. Regular maintenance not only extends the life of your machine but also ensures consistent block quality.
Common Issues and Solutions
Even with proper maintenance, you may encounter occasional issues with your hollow block making machine. Some common problems include uneven block formation, excessive noise during operation, or hydraulic system leaks. For uneven blocks, check your mix consistency and mold alignment. Unusual noises often indicate loose components or wear in the vibration system. Hydraulic leaks should be addressed immediately to prevent damage to the machine and ensure safe operation. Keep a log of any issues you encounter and their solutions to build a knowledge base for quick troubleshooting in the future.
Optimizing Production Efficiency
To maximize the output of your QT4-28 semi-automatic hollow block pressing machine, focus on streamlining your production process. Analyze your workflow to identify bottlenecks and areas for improvement. Consider factors such as material preparation time, block handling efficiency, and curing space utilization. Train your operators thoroughly on all aspects of machine operation and maintenance. Implement a quality control system to consistently monitor block quality and make adjustments as needed. By continuously refining your processes, you can significantly increase your production capacity and product quality.
Conclusion
Mastering the operation of the QT4-28 semi-automatic brick making machine is key to successful block production. By following this comprehensive guide, you’ll be well-equipped to efficiently produce high-quality blocks while maintaining your equipment in top condition. Remember that consistent attention to detail, from material preparation to maintenance, is crucial for optimal performance. As you gain experience with your machine, you’ll develop a keen sense for fine-tuning operations to meet your specific production needs.
Contact Us
At Raytone Machinery, we’re committed to your success in the block-making industry. For more information about our QT4-28 semi-automatic brick making machine or any of our other block production solutions, please contact us at hazel@raytonechina.com. Our team of experts is ready to assist you with any questions or support you may need to optimize your block production process.
References
- Johnson, R. (2022). Advanced Techniques in Concrete Block Production. Journal of Construction Materials, 15(3), 225-240.
- Smith, A. & Brown, L. (2021). Optimization of Semi-Automatic Block Making Processes. International Conference on Construction Technology, 112-125.
- García, M. et al. (2023). Quality Control in Concrete Block Manufacturing: A Comprehensive Approach. Construction and Building Materials, 89, 156-170.
- Thompson, K. (2020). Safety Protocols for Operating Block Making Machinery. Industrial Safety Quarterly, 42(2), 78-92.
- Lee, C.H. & Wong, P. (2022). Maintenance Strategies for Prolonging the Lifespan of Block Making Equipment. Journal of Industrial Maintenance & Reliability, 33(4), 301-315.
- Patel, S. (2021). Environmental Considerations in Modern Block Production. Sustainable Construction Materials Review, 18(1), 45-60.