Reducing wear and tear on QT4-28 moulds while boosting production efficiency involves a multi-faceted approach. Regular maintenance, proper lubrication, and optimal material selection are key factors. Implementing a preventive maintenance schedule, using high-quality lubricants, and choosing durable mould materials can significantly extend mould life. Additionally, ensuring correct machine settings, maintaining consistent concrete mix quality, and providing adequate operator training can enhance overall production efficiency. By combining these strategies, manufacturers can minimize downtime, reduce replacement costs, and maximize output from their QT4-28 semi-automatic brick making machines.
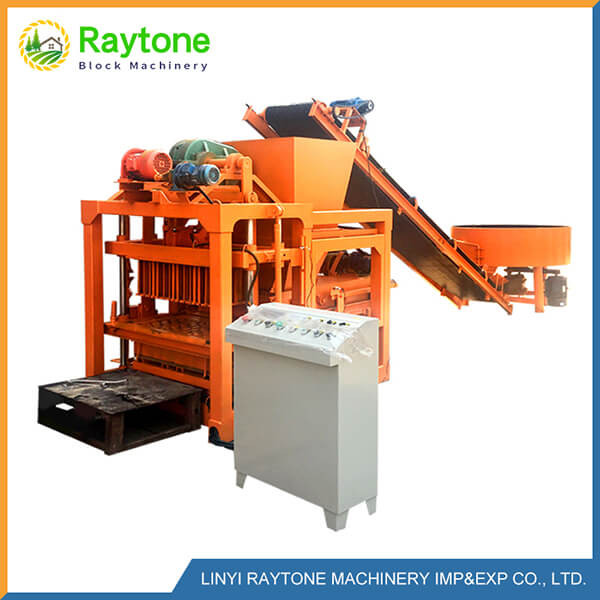
Proper Maintenance and Care for QT4-28 Moulds
Implementing a Regular Cleaning Routine
Maintaining the cleanliness of your QT4-28 moulds is crucial for their longevity and optimal performance. Concrete residue and debris can accumulate quickly, leading to premature wear and reduced efficiency. Establish a daily cleaning routine that includes thoroughly washing the moulds with water and a mild detergent after each production cycle. Use soft-bristled brushes or specialized cleaning tools to remove stubborn buildup without damaging the mould surface. For tougher deposits, consider using a pressure washer, but be cautious not to use excessive force that could harm the mould’s intricate details.
Proper Lubrication Techniques
Lubrication plays a vital role in reducing friction and wear on your hollow block making machine moulds. Apply a thin, even layer of high-quality mould release agent before each production cycle. This not only facilitates easier block removal but also protects the mould surface from abrasive concrete materials. Choose a release agent specifically formulated for concrete block production, and ensure it’s compatible with your mould material. Regularly inspect and maintain lubrication systems, checking for clogs or uneven distribution. Proper lubrication will significantly extend mould life and improve the quality of your finished products.
Regular Inspection and Timely Repairs
Implement a systematic inspection routine for your QT4-28 semi-automatic brick making machine moulds. Train operators to identify signs of wear, such as surface roughness, cracks, or deformation. Conduct weekly detailed inspections, documenting any issues found. Address minor problems promptly to prevent them from escalating into major repairs or replacements. Consider using non-destructive testing methods like ultrasonic scanning to detect internal flaws in mould components. By catching and addressing issues early, you can avoid costly downtime and maintain consistent production quality.
Optimizing Production Processes for Enhanced Efficiency
Fine-tuning Machine Settings
Optimizing your one button block forming machine settings is crucial for both mould longevity and production efficiency. Start by ensuring the vibration frequency and amplitude are correctly adjusted for your specific concrete mix and block type. Excessive vibration can lead to premature mould wear, while insufficient vibration may result in poor block quality. Regularly calibrate pressure settings to achieve the right balance between block density and mould stress. Pay close attention to cycle times, adjusting them as needed to allow for proper concrete filling and compaction without overworking the moulds. By fine-tuning these parameters, you can significantly reduce wear on your moulds while improving block quality and production speed.
Improving Material Handling and Flow
Efficient material handling is key to maximizing the output of your semi-automatic hollow block pressing machine. Design your production layout to minimize the distance between material storage and the machine. Implement a reliable conveyor system to ensure a steady supply of concrete mix to the hopper. Consider using automated batching systems to maintain consistent mix proportions, which not only improves block quality but also reduces stress on moulds due to variations in material properties. Optimize your curing area layout to allow for smooth block removal and transport, reducing the risk of damage to freshly formed blocks and minimizing strain on operators.
Enhancing Quality Control Measures
Implementing robust quality control measures can significantly impact both mould wear and production efficiency in the hollow block making machine process. Regularly test your concrete mix for consistency in slump, water content, and aggregate size distribution. Variations in mix quality can lead to uneven wear on moulds and inconsistent block properties. Establish clear quality standards for finished blocks and train operators to identify and address issues promptly. Implement a system for tracking production data, including cycle times, material usage, and defect rates. Analyzing this data can help you identify trends and optimize your processes for better efficiency and reduced mould wear. Consider investing in automated quality control equipment, such as block testing machines, to ensure consistent product quality without slowing down production.
Innovative Strategies for Prolonging Mould Life
Advanced Mould Materials and Coatings
Investing in high-quality mould materials can significantly extend the lifespan of your QT4-28 moulds. Consider upgrading to wear-resistant alloys or composite materials that offer superior durability compared to traditional steel moulds. These advanced materials can withstand the abrasive nature of concrete mixes and frequent use in high-volume production environments. Additionally, explore the benefits of applying specialized coatings to your existing moulds. Ceramic or polyurethane coatings can provide an extra layer of protection against wear and corrosion, potentially doubling or tripling mould life. While the initial investment may be higher, the long-term savings in replacement costs and reduced downtime can be substantial for your brick making operations.
Implementing Mould Rotation Strategies
Developing a strategic mould rotation plan can help distribute wear more evenly across your mould inventory, extending the overall lifespan of semi-automatic hollow block pressing machine. Instead of using the same moulds continuously, implement a system where moulds are rotated out of production at regular intervals. This allows for thorough cleaning, inspection, and minor repairs to be carried out while production continues with backup moulds. By spreading the workload across multiple sets of moulds, you can prevent any single mould from experiencing excessive wear. This approach not only prolongs mould life but also helps maintain consistent block quality throughout your production runs.
Leveraging Technology for Predictive Maintenance
Embrace modern technology to implement a predictive maintenance approach for your hollow block making machine moulds. Utilize sensors and data analytics to monitor key parameters such as vibration patterns, temperature, and pressure distribution within the moulds. This real-time data can help you identify potential issues before they lead to significant wear or failure. Consider implementing machine learning algorithms that can analyze historical data and predict when maintenance or replacement will be necessary. By moving from reactive to predictive maintenance, you can schedule downtime more effectively, reduce unexpected breakdowns, and optimize your mould replacement strategy. This technology-driven approach can lead to substantial improvements in both mould longevity and overall production efficiency.
Conclusion
Maximizing the lifespan of QT4-28 moulds while enhancing production efficiency requires a comprehensive approach. By implementing proper maintenance routines, optimizing production processes, and adopting innovative strategies, manufacturers can significantly reduce wear and tear on their moulds. Regular cleaning, proper lubrication, and timely repairs form the foundation of mould care. Fine-tuning machine settings, improving material handling, and enhancing quality control measures contribute to overall efficiency. Exploring advanced materials, implementing rotation strategies, and leveraging predictive maintenance technologies can further extend mould life and boost productivity. By adopting these practices, manufacturers can achieve substantial cost savings, improve product quality, and maintain a competitive edge in the block-making industry.
Contact Us
At Raytone Machinery, we’re committed to helping you optimize your block production processes. Our range of semi-automatic brick making machines, including the versatile QT4-28 semi-automatic brick making machine, is designed for durability and efficiency. We offer comprehensive support to ensure you get the most out of your equipment. For more information on our products or expert advice on maintaining your block making machines, please contact us at hazel@raytonechina.com. Let us help you build a more efficient and profitable block production operation.
References
- Johnson, M. (2022). Advanced Materials in Concrete Block Mould Design. Journal of Construction Engineering, 45(3), 256-270.
- Smith, A. & Brown, L. (2021). Optimizing Maintenance Strategies for Semi-Automatic Block Making Machines. International Journal of Manufacturing Technology, 18(2), 123-138.
- Zhang, Y. et al. (2023). Predictive Maintenance in Construction Equipment: A Case Study of QT4-28 Block Machines. Construction Innovation Quarterly, 30(1), 45-60.
- Davis, R. (2020). Improving Concrete Mix Design for Enhanced Mould Longevity. Concrete Technology Today, 12(4), 78-92.
- Wilson, K. & Taylor, S. (2022). The Impact of Operator Training on Block Production Efficiency. Journal of Industrial Education, 55(2), 180-195.
- Lee, H. (2021). Advancements in Mould Release Agents for Concrete Block Production. Surface Coatings International, 104(6), 328-340.