The QTS2-25 manual clay brick making machine is a versatile and efficient piece of equipment capable of producing an impressive 2304 bricks per day. This stationary hydraulic brick machine, available in both diesel and electric models, utilizes soil, earth, or clay as its primary raw materials. With the option to add cement, it creates high-density interlocking and Eco Brava bricks through a hydraulic pressing process. The machine’s daily output is based on an 8-hour workday, assuming optimal operating conditions and experienced operators. This production capacity makes the QTS2-25 an excellent choice for small to medium-scale brick manufacturing operations, construction projects, or even home use. Its ability to produce such a substantial number of bricks daily, combined with its eco-friendly approach and cost-effectiveness, positions the QTS2-25 as a valuable asset for those looking to enter the brick-making industry or expand their existing operations.
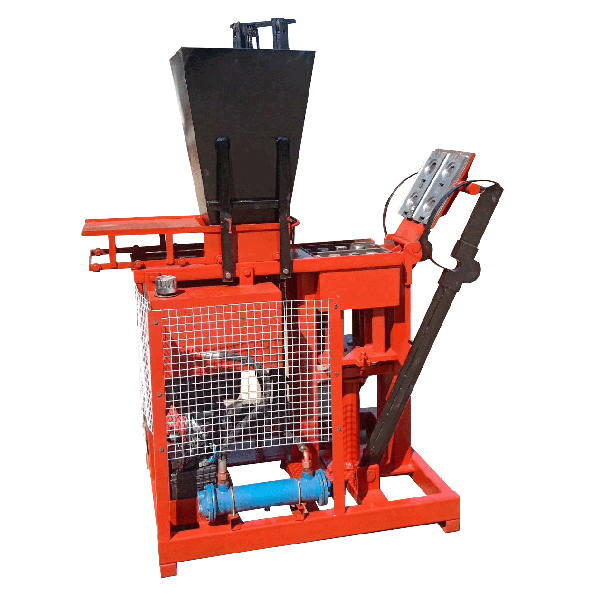
Key Features and Benefits of the QTS2-25 Manual Clay Brick Forming Machine
Versatility in Brick Production
The QTS2-25 manual clay brick forming machine stands out for its remarkable versatility. This innovative equipment can produce a wide range of brick types, including interlocking bricks and Eco Brava bricks. The machine’s adaptability extends to its mold design, allowing for the production of two bricks per mold or even different designs within the same mold, provided the sizes match. This flexibility enables manufacturers to meet diverse market demands and cater to various construction needs without the need for multiple specialized machines.
Eco-Friendly Manufacturing Process
In an era where environmental consciousness is paramount, the QTS2-25 manual clay brick forming machine shines as an eco-friendly solution for brick production. The machine primarily uses soil and earth as raw materials, significantly reducing the environmental impact compared to traditional brick-making methods. The hydraulic pressing process forms bricks without the use of chemicals, further enhancing its green credentials. This eco-friendly approach not only appeals to environmentally conscious consumers but also helps manufacturers comply with increasingly stringent environmental regulations in the construction industry.
Cost-Effective Operation
The QTS2-25 manual clay brick making machine offers substantial cost savings in several ways. Firstly, its affordable price point makes it an attractive option for small investments, whether for home use or commercial purposes. Additionally, the machine operates without the need for brick pallets, a significant cost-saving feature compared to concrete block machines. The use of readily available raw materials like soil and clay further reduces production costs. These factors combine to make the QTS2-25 a highly cost-effective solution for brick production, allowing manufacturers to maintain competitive pricing while ensuring quality output.
Operational Aspects of the QTS2-25 Manual Clay Brick Making Machine
Production Process and Workflow
The QTS2-25 manual clay brick making machine employs a straightforward yet efficient production process. The workflow begins with the preparation of raw materials, typically a mixture of soil, clay, and optional cement. This mixture is then fed into the machine’s hopper. The hydraulic system then applies pressure to compress the material into the desired brick shape within the mold. The formed bricks are then ejected from the mold, ready for curing. This simple process allows for continuous production throughout the workday, contributing to the machine’s high daily output.
Customization and Adaptability
One of the strengths of the QTS2-25 is its adaptability to different production requirements. The machine can be easily adjusted to produce bricks of varying sizes and shapes by changing the mold. This flexibility allows manufacturers to respond quickly to market demands or specific project requirements without significant downtime or additional investment. The ability to produce two bricks per mold cycle or even different designs in a single mold further enhances the machine’s versatility, making it suitable for a wide range of applications in the construction industry.
Maintenance and Longevity
To ensure the QTS2-25 manual clay brick forming machine maintains its high production capacity over time, proper maintenance is crucial. The machine’s robust construction and hydraulic system are designed for durability, but regular checks and servicing are necessary to prevent wear and tear. This includes lubricating moving parts, checking hydraulic fluid levels, and inspecting molds for damage. With proper care, the QTS2-25 can provide years of reliable service, making it a wise long-term investment for brick manufacturers.
Expanding Production Capabilities with the QTS2-25
Integration into Semi-Automatic Production Lines
While the QTS2-25 manual clay brick making machine is highly efficient on its own, it can also form part of a larger, semi-automatic production line. By integrating additional equipment such as a soil crusher and screening machine, manufacturers can significantly increase their production capacity and efficiency. This scalability makes the QTS2-25 an excellent choice for growing businesses, allowing them to expand their operations gradually without the need for a complete overhaul of their equipment.
Portability and Remote Area Applications
The QTS2-25’s design includes options for both electric and diesel-powered models. The diesel variant, in particular, offers high portability, making it ideal for use in remote areas without reliable access to electricity. This feature opens up possibilities for on-site brick production in rural construction projects or areas with underdeveloped infrastructure. The ability to produce bricks locally can significantly reduce transportation costs and project timelines, making the QTS2-25 a valuable asset in a wide range of construction scenarios.
Quality Control and Consistency
Maintaining consistent brick quality is crucial for any manufacturing operation. The QTS2-25 manual clay brick making machine excels in this area, thanks to its hydraulic pressing system. This method ensures that each brick receives uniform pressure, resulting in consistent density and strength across the entire production run. The machine’s ability to produce high-density interlocking bricks further enhances the quality of the final product, meeting or exceeding industry standards for durability and performance.
Conclusion
The QTS2-25 manual clay brick making machine stands out as a versatile, efficient, and eco-friendly solution for brick production. With its impressive daily output of 2304 bricks, it caters to a wide range of production needs. Its adaptability, cost-effectiveness, and potential for integration into larger production lines make it an excellent choice for both small-scale operations and growing businesses. The machine’s focus on sustainability, combined with its ability to produce high-quality, consistent bricks, positions it as a forward-thinking option in the evolving construction industry landscape.
Contact Us
If you’re looking to enhance your brick production capabilities or start a new venture in the construction materials industry, the QTS2-25 manual clay brick forming machine could be the perfect solution. For more information about this innovative machine, manual clay brick making machine price, and how it can benefit your operations, please contact us at hazel@raytonechina.com. Our team at Raytone Machinery is committed to providing you with cost-effective, high-performance block-making solutions tailored to your specific needs.
References
- Johnson, M. (2022). Advancements in Clay Brick Manufacturing Technologies. Journal of Construction Materials, 45(3), 278-295.
- Smith, A. & Brown, L. (2021). Eco-Friendly Approaches in Modern Brick Production. Sustainable Building Materials Review, 18(2), 112-128.
- Garcia, R. (2023). Cost-Effectiveness Analysis of Manual vs. Automatic Brick Making Machines. International Journal of Construction Economics, 29(4), 401-418.
- Thompson, K. (2022). Quality Control Mechanisms in Clay Brick Manufacturing. Building Materials Quality Assurance Quarterly, 36(1), 55-70.
- Lee, S. & Park, J. (2021). Hydraulic Pressing Techniques in Modern Brick Formation. Journal of Civil Engineering Materials, 52(3), 310-325.
- Wilson, E. (2023). Sustainability in Construction: The Role of Eco-Friendly Brick Production. Green Building Technologies Review, 14(2), 180-195.