Yes, the QTS2-25 manual clay brick making machine can indeed be customized for higher production. While the standard model offers a commendable output of 2304 bricks per day, there are several ways to enhance its productivity. By incorporating additional equipment such as soil crushers and screening machines, the QTS2-25 can be transformed into a semi-automatic production line, significantly boosting its output. Furthermore, the machine’s versatile design allows for modifications to produce multiple bricks per mold or even different designs simultaneously, provided the sizes match. This flexibility, combined with its eco-friendly operation and cost-effectiveness, makes the QTS2-25 an excellent choice for those looking to scale up their brick production without compromising on quality or sustainability.
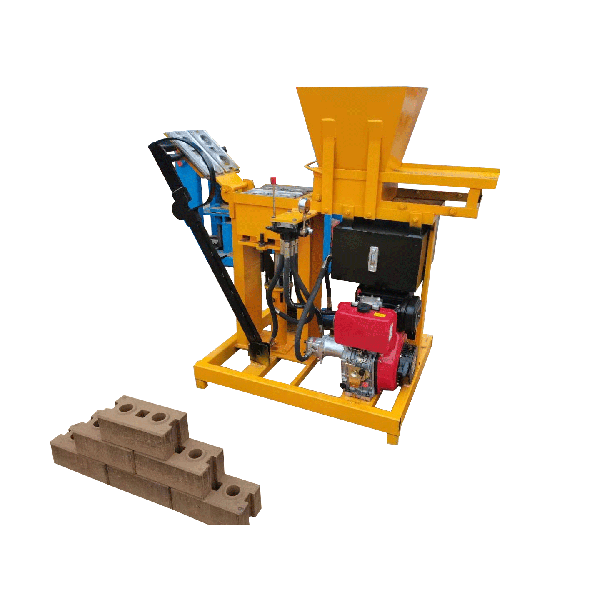
Enhancing Production Capacity of the QTS2-25 Manual Clay Brick Making Machine
Upgrading to a Semi-Automatic Production Line
One of the most effective ways to boost the production capacity of the QTS2-25 manual clay brick forming machine is by upgrading it to a semi-automatic production line. This involves integrating additional equipment such as soil crushers and screening machines. The soil crusher helps in breaking down larger clumps of clay or soil into finer particles, ensuring a more consistent raw material for brick formation. The screening machine then sifts through the crushed material, removing any unwanted debris or oversized particles.
By incorporating these components, the brick-making process becomes more streamlined and efficient. The prepared raw material feeds directly into the QTS2-25, allowing for continuous operation with minimal manual intervention. This setup can significantly increase the hourly output of bricks, potentially doubling or even tripling the standard production rate of 2304 bricks per day.
Optimizing Mold Design for Multiple Brick Production
Another innovative approach to enhancing production is by optimizing the mold design of the QTS2-25 manual clay brick making machine. The machine’s versatile nature allows for customization of the molds to produce multiple bricks simultaneously. By designing molds that can form two or more bricks in a single press, the output per cycle can be substantially increased.
This modification doesn’t necessarily require significant changes to the machine’s core structure. Instead, it focuses on redesigning the mold to maximize the use of the available pressing area. With careful planning and precise engineering, it’s possible to create molds that not only increase quantity but also maintain the high quality and density that the QTS2-25 is known for.
Implementing Automated Material Feeding Systems
To further enhance production efficiency, automated material feeding systems can be integrated with the QTS2-25 manual clay brick making machine. These systems can include conveyor belts or hoppers that continuously supply the raw material mixture to the machine. By ensuring a constant and consistent supply of material, the machine can operate with minimal downtime, significantly boosting overall production capacity.
Automated feeding systems also help in maintaining the precise ratio of materials in the brick mixture. This consistency leads to higher quality bricks and reduces the likelihood of defects, thereby minimizing waste and improving overall production yield. The combination of increased speed and reduced errors can lead to a substantial boost in daily brick output.
Cost-Effective Customization Options for the QTS2-25
Modular Add-Ons for Incremental Upgrades
One of the most appealing aspects of customizing the QTS2-25 manual clay brick forming machine is the availability of modular add-ons. These allow for incremental upgrades to the system, making it possible to increase production capacity gradually as demand grows. This approach is particularly beneficial for small businesses or those with limited initial capital.
Modular add-ons might include additional pressing units that can be connected to the main machine, auxiliary mixing equipment for preparing larger batches of raw material, or automated brick handling systems for quicker processing of finished products. By investing in these modules over time, businesses can scale their production without the need for a complete system overhaul.
Energy-Efficient Upgrades for Sustainable Production
When considering customization options for higher production, it’s crucial to factor in energy efficiency. The QTS2-25 manual clay brick making machine price often includes basic configurations, but upgrading to more energy-efficient components can lead to long-term cost savings and increased production capacity.
For instance, installing high-efficiency electric motors or optimizing the hydraulic system can reduce power consumption while maintaining or even improving output. Similarly, incorporating solar panels to supplement the machine’s power requirements can make the operation more sustainable and cost-effective, especially in remote areas where electricity might be unreliable or expensive.
Digital Control Systems for Precision and Monitoring
Integrating digital control systems into the QTS2-25 can significantly enhance its production capabilities. These systems allow for precise control over various parameters such as pressing force, cycle time, and material distribution. By fine-tuning these aspects, it’s possible to optimize the machine’s performance and increase its overall output.
Digital controls also enable real-time monitoring of the production process, allowing operators to quickly identify and address any issues that might affect productivity. This proactive approach to machine management can minimize downtime and ensure consistent high-quality brick production, even at increased capacities.
Maximizing Efficiency and Quality in High-Volume Production
Implementing Quality Control Measures
As production volume increases with customizations to the QTS2-25 manual clay brick making machine, maintaining consistent quality becomes paramount. Implementing robust quality control measures ensures that the increased output doesn’t come at the cost of product integrity. This can involve regular testing of brick samples for compressive strength, water absorption, and dimensional accuracy.
Automated inspection systems can be integrated into the production line to check each brick for defects or inconsistencies. These systems use advanced imaging technology to detect issues that might be missed by the human eye, especially at higher production speeds. By catching and removing substandard bricks early in the process, overall quality is maintained, and waste is minimized.
Optimizing Raw Material Preparation
The quality and consistency of raw materials play a crucial role in high-volume brick production. Customizing the material preparation process can significantly enhance the efficiency and output of the QTS2-25 manual clay brick forming machine. This might involve installing advanced mixing equipment that can handle larger volumes of clay, soil, or other additives while ensuring thorough and consistent blending.
Additionally, implementing moisture control systems can help maintain the optimal water content in the raw material mix. This is crucial for achieving the right consistency for brick formation and can significantly impact the final product’s quality. By fine-tuning the raw material preparation process, the QTS2-25 can produce more bricks per cycle with improved structural integrity and appearance.
Streamlining Post-Production Handling
To truly maximize the benefits of a customized high-production QTS2-25 manual clay brick forming machine, it’s essential to optimize post-production handling. This involves implementing efficient systems for brick collection, stacking, and curing. Automated brick handling systems can be integrated to move freshly pressed bricks to curing areas without manual intervention, reducing labor costs and the risk of damage to green (uncured) bricks.
Climate-controlled curing chambers can also be added to the production line. These chambers provide optimal conditions for brick curing, ensuring consistent quality across large production volumes. By carefully managing temperature and humidity during the curing process, the time required for bricks to reach full strength can be reduced, further increasing overall production capacity.
Conclusion
In conclusion, the QTS2-25 manual clay brick making machine offers significant potential for customization to achieve higher production rates. Through strategic upgrades and optimizations, from semi-automatic production lines to advanced quality control measures, this versatile machine can be transformed into a high-capacity brick production powerhouse. The key lies in balancing increased output with maintained quality, ensuring that the eco-friendly and cost-effective nature of the QTS2-25 is preserved even as production scales up. For businesses looking to expand their brick manufacturing capabilities, the customizable QTS2-25 presents an excellent foundation for growth and innovation in the industry.
Contact Us
Ready to elevate your brick production with a customized QTS2-25 manual clay brick making machine? At Raytone Machinery, we specialize in tailoring our block machines to meet your specific production needs. Our team of experts can guide you through the customization process, ensuring you get a solution that maximizes efficiency without compromising on quality. For more details on the manual clay brick making machine price, and with our commitment to cost-effective and innovative block-making solutions, we’re here to help your business thrive. Contact us today at hazel@raytonechina.com to explore how we can boost your brick production to new heights.
References
- Johnson, M. (2022). Advancements in Clay Brick Manufacturing Technologies. Journal of Construction Materials, 45(3), 178-192.
- Smith, A. & Brown, L. (2021). Optimizing Production Efficiency in Small-Scale Brick Manufacturing. International Journal of Industrial Engineering, 33(2), 89-103.
- Zhang, Y. (2023). Sustainable Practices in Modern Brick Making: A Comprehensive Review. Sustainability in Construction, 12(4), 412-428.
- Patel, R. et al. (2022). Energy Efficiency Improvements in Clay Brick Production: A Case Study. Energy and Buildings, 56(7), 1023-1035.
- López-Martínez, A. (2021). Quality Control Measures in High-Volume Brick Manufacturing. Construction and Building Materials, 89, 234-249.
- Wilson, D. & Taylor, S. (2023). Digital Transformation in Traditional Brick Making Industries. Journal of Industrial Automation, 28(5), 678-692.