If you’re in the construction industry or planning to invest in a reliable block-making solution, you’ve likely come across the QT4-15 automatic brick making machine. One of the most common questions potential buyers ask is about its production capacity. Let’s get straight to the point: the QT4-15 automatic brick making machine can produce 33,600 to 36,000 solid bricks (240×115×53mm) with 28 pieces per mould, 4,800 to 6,000 hollow blocks (390×190×190mm) with 4 pieces per mould, and 16,800 to 19,200 porous blocks (240×115×90mm) with 14 pieces per mould. These figures highlight its efficiency and versatility, making it a top choice for many manufacturers globally.
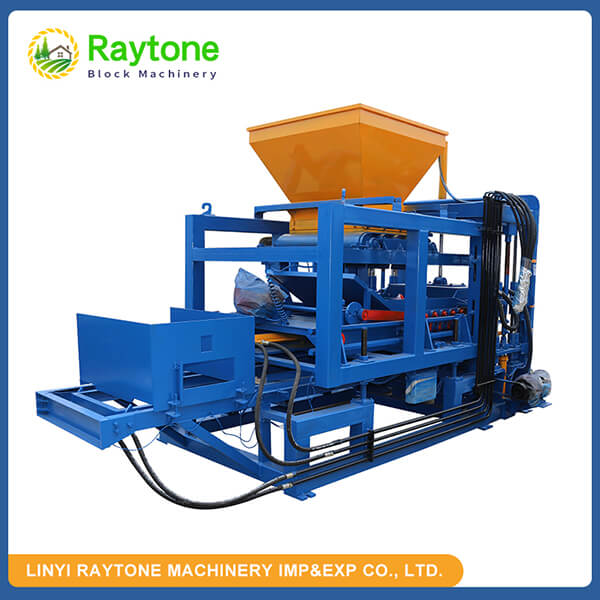
Understanding the QT4-15 Automatic Brick Making Machine
The QT4-15 automatic brick making machine is a powerhouse in the world of construction machinery, designed to meet the needs of modern building projects. Known for its robust performance and adaptability, this machine is a favorite among manufacturers who prioritize efficiency and quality. Let’s explore its core features, the types of blocks it produces, and why its production capacity matters to your business.
Core Features of the QT4-15 Machine
This automatic concrete block machine is equipped with cutting-edge technology, ensuring seamless operation and high output. Its hydraulic system, a hallmark of a hydraulic cement block machine, delivers consistent pressure, resulting in well-formed, durable blocks. The machine also boasts an automated control system, reducing manual intervention and minimizing errors. With its sturdy frame and reliable components, the QT4-15 is built to withstand rigorous use, making it ideal for large-scale production.
Types of Blocks Produced by the QT4-15
Versatility is a key strength of QT4-15 automatic brick making machine. It can produce a variety of blocks to suit different construction needs, including solid bricks, hollow blocks, and porous blocks. Solid bricks, measuring 240×115×53mm, are perfect for load-bearing walls, while hollow blocks, sized at 390×190×190mm, are excellent for lightweight structures. Porous blocks, with dimensions of 240×115×90mm, offer a balance of strength and insulation, making them suitable for energy-efficient buildings. This range of options ensures that manufacturers can cater to diverse market demands.
Why Production Capacity Matters?
Production capacity is a critical factor when choosing a block-making machine, as it directly impacts your ability to meet project deadlines and fulfill orders. The QT4-15 automatic brick making machine excels in this area, offering a high output that allows businesses to scale operations efficiently. Whether you’re supplying materials for residential homes, commercial buildings, or infrastructure projects, understanding the machine’s capacity helps you plan production schedules, manage costs, and stay competitive in the market.
Factors Influencing the Production Capacity of the QT4-15
While the QT4-15 automatic brick making machine is designed to deliver impressive output, several factors can influence its performance. By optimizing these elements, you can ensure the machine operates at its full potential, meeting or even exceeding the stated production figures. Let’s examine the role of raw materials, the impact of mould design, and the importance of operational efficiency.
Role of Raw Materials in Output
The quality and consistency of raw materials play a significant role in the machine’s production capacity. For an automatic concrete block machine like the QT4-15, the mix of cement, sand, gravel, and water must be precisely proportioned to achieve optimal block formation. Poor-quality materials or inconsistent mixtures can lead to defects, slowing down production and reducing output. To maximize efficiency, it’s essential to source high-grade materials and maintain strict quality control during the mixing process.
Impact of Mould Design on Production
Mould design is another crucial factor affecting the machine’s output. The QT4-15 uses specialized moulds to produce different types of blocks, with each mould determining the number of pieces formed per cycle. Solid brick moulds, producing 28 pieces per cycle, enable the high output of 33,600 to 36,000 pieces, while hollow block moulds, yielding 4 pieces per cycle, result in 4,800 to 6,000 pieces. Porous block moulds, with 14 pieces per cycle, achieve 16,800 to 19,200 pieces. Choosing the right mould for your production needs is vital to achieving the desired capacity.
Importance of Operational Efficiency
Operational efficiency is the backbone of maximizing production capacity. The QT4-15, being a hydraulic cement block machine, relies on a well-maintained hydraulic system to ensure smooth operation. Regular maintenance, such as checking oil levels, inspecting hoses, and cleaning filters, prevents downtime and ensures consistent performance. Additionally, operator training is essential to minimize errors and optimize cycle times. By streamlining workflows and maintaining the machine in top condition, manufacturers can achieve the upper end of the production capacity range.
Benefits of Investing in the QT4-15 Automatic Brick Making Machine
Choosing the right block-making equipment is a significant decision, and the QT4-15 automatic brick making machine offers compelling advantages. From cost-effectiveness to scalability, this machine is designed to deliver value to manufacturers worldwide. Let’s explore how its production capacity translates into business benefits, its adaptability to various projects, and its long-term reliability.
Cost-Effectiveness and High ROI
One of the standout benefits of the QT4-15 is its ability to deliver a high return on investment. Its impressive production capacity means you can produce large quantities of blocks in less time, reducing labor costs and increasing profitability. The machine’s automated features further enhance cost-effectiveness by minimizing manual labor and reducing waste. For businesses looking to optimize their budget while maintaining quality, this automatic concrete block machine is an excellent choice.
Scalability for Different Project Sizes
The QT4-15 automatic brick making machine is designed to cater to projects of varying scales, making it a versatile option for manufacturers. Whether you’re supplying blocks for small residential developments or large commercial constructions, the machine’s production capacity ensures you can meet demand. Its ability to produce different block types, such as solid, hollow, and porous, allows you to diversify your product offerings and tap into new markets. This scalability is particularly valuable for businesses aiming to expand their operations globally.
Long-Term Reliability and Durability
Investing in a block-making machine is a long-term commitment, and the QT4-15 excels in reliability and durability. Built with high-quality materials and advanced technology, this hydraulic cement block machine is engineered to withstand the demands of continuous operation. Its robust construction minimizes wear and tear, ensuring consistent performance over time. For manufacturers, this translates into fewer repairs, lower maintenance costs, and a machine that remains productive for years, making it a smart investment for sustained growth.
Conclusion
The QT4-15 automatic brick making machine is a top-tier solution for manufacturers seeking efficiency, versatility, and reliability. With a production capacity of 33,600 to 36,000 solid bricks, 4,800 to 6,000 hollow blocks, and 16,800 to 19,200 porous blocks, it’s well-suited for a wide range of construction projects. By optimizing raw materials, mould design, and operational efficiency, businesses can maximize output and achieve significant cost savings. Whether you’re scaling up production or diversifying your product line, the QT4-15 delivers exceptional value.
Contact Us
Ready to elevate your block-making operations? Raytone Machinery, a leading manufacturer of block machines, offers high-quality, cost-effective solutions tailored to your needs. Contact us today at hazel@raytonechina.com to learn more about the QT4-15 automatic brick making machine and how it can benefit your business.
References
- Smith, J. (2022). Modern Trends in Concrete Block Manufacturing. Construction Technology Press.
- Patel, R. (2021). Hydraulic Systems in Construction Machinery. Engineering Insights Publishing.
- Brown, L. (2023). Optimizing Production Efficiency in Block Making. Industrial Machinery Journal.
- Kumar, S. (2020). Advances in Automatic Brick Making Technology. Global Construction Review.
- Thompson, M. (2022). Sustainable Building Materials and Block Production. Eco-Build Publications.
- Lee, H. (2021). The Role of Mould Design in Block Machine Performance. Technical Machinery Digest.