The QT4-15 automatic brick making machine offers numerous advantages for construction and manufacturing businesses. This versatile hydraulic cement block machine excels in efficiency, productivity, and cost-effectiveness. With its robust design and advanced features, the QT4-15 can produce a wide variety of concrete blocks, pavers, and curbstones at high speeds. Its automatic operation reduces labor costs while ensuring consistent quality output. The machine’s durable construction, featuring high-strength steel and manganese components, guarantees long-term reliability and minimal maintenance. Additionally, the QT4-15’s compact footprint and user-friendly interface make it an ideal choice for both small-scale operations and larger production facilities seeking to optimize their brick and block manufacturing processes.
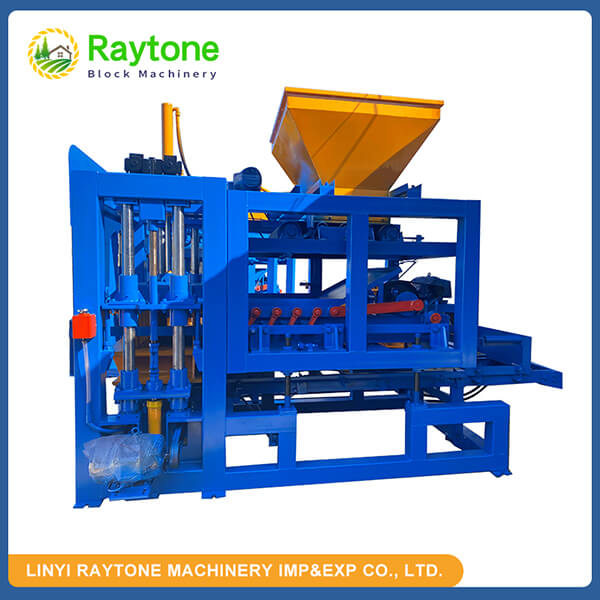
Key Features and Capabilities of the QT4-15 Automatic Brick Making Machine
High-Capacity Production
The QT4-15 automatic brick making machine boasts impressive production capabilities. In a standard 8-hour shift, this powerhouse can manufacture up to 7,680 8-inch blocks or an astounding 57,600 solid bricks measuring 240x115x50mm. This high-capacity output makes the QT4-15 an excellent choice for businesses looking to meet large-scale demands efficiently. The machine’s ability to maintain consistent production rates throughout extended operating periods ensures that manufacturers can reliably fulfill orders and maintain steady inventory levels.
Versatile Mold Options
One of the standout features of the QT4-15 automatic concrete block machine is its adaptability to various mold types. The machine accommodates interchangeable molds, allowing manufacturers to produce a diverse range of products, including hollow blocks, solid bricks, colored pavers, and curbstones. This versatility enables businesses to cater to different market demands without investing in multiple specialized machines. The ability to switch between mold types quickly and easily enhances production flexibility and helps manufacturers respond swiftly to changing customer requirements.
Durable Construction for Long-Term Performance
The QT4-15 is built to last, with a focus on durability and longevity. The machine frame is constructed from high-strength steel, expertly welded to withstand the rigors of continuous operation. The mold frame utilizes high-hardness 55# manganese steel, while the tamping head is made from 16# manganese steel. These components undergo carburizing and heat treatment processes, resulting in a hardness rating of up to 60 degrees. This exceptional durability translates to a mold lifespan of approximately 10,000 cycles, significantly reducing replacement costs and minimizing production interruptions.
Operational Efficiency and Cost-Effectiveness of the QT4-15
Automated Production Process
The QT4-15 automatic brick making machine streamlines the production process through its advanced automation features. From material feeding to molding and curing, the machine requires minimal human intervention, reducing labor costs and the potential for human error. This automated approach ensures consistent quality across production runs, leading to fewer defects and less material waste. The machine’s precision control systems allow for fine-tuning of various parameters, enabling manufacturers to optimize their production processes for maximum efficiency and product quality.
Energy-Efficient Operation
Despite its high production capacity, the QT4-15 hydraulic cement block machine is designed with energy efficiency in mind. The machine incorporates modern hydraulic and electrical systems that minimize power consumption without compromising performance. This energy-efficient operation not only reduces utility costs but also aligns with sustainability goals, making it an attractive option for environmentally conscious manufacturers. The optimized power usage of the QT4-15 contributes to lower overall production costs, enhancing the competitiveness of businesses in the construction materials market.
Compact Footprint and Space Utilization
The QT4-15 offers impressive production capabilities within a relatively compact footprint. With a recommended factory area of 1200-2500 m², the machine allows businesses to maximize their space utilization. This compact design is particularly beneficial for operations with limited floor space or those looking to optimize their facility layout. The efficient use of space can lead to reduced overhead costs and improved workflow organization, further contributing to the overall cost-effectiveness of the brick and block production process.
Integration and Support for the QT4-15 Automatic Brick Making Machine
Easy Installation and Setup
The QT4-15 automatic brick making machine is designed for straightforward installation and setup, minimizing downtime during integration into existing production lines. Its modular design allows for efficient assembly and configuration, reducing the time and resources required for initial setup. The machine’s user-friendly interface and intuitive controls facilitate quick operator training, enabling businesses to commence production rapidly after installation. This ease of integration makes the QT4-15 an attractive option for companies looking to upgrade their brick and block manufacturing capabilities without extensive disruption to their operations.
Comprehensive Training and Technical Support
Manufacturers of the QT4-15 automatic brick making machine typically offer comprehensive training programs and ongoing technical support to ensure optimal machine performance and longevity. These training sessions cover all aspects of machine operation, maintenance, and troubleshooting, empowering operators to maximize the machine’s potential. The availability of expert technical support helps minimize downtime in case of issues, ensuring smooth and continuous production. This commitment to customer support enhances the overall value proposition of the QT4-15, providing peace of mind to businesses investing in this advanced brick making technology.
Scalability and Future-Proofing
The QT4-15 automatic brick making machine offers excellent scalability, making it suitable for businesses of various sizes and growth stages. Its modular design allows for easy upgrades and modifications to meet evolving production needs. As demand increases, the machine can be integrated into larger production lines or complemented with additional units to boost overall capacity. This scalability ensures that the QT4-15 remains a valuable asset as businesses expand, providing a future-proof solution for long-term brick and block manufacturing requirements.
Conclusion
The QT4-15 automatic brick making machine stands out as a versatile, efficient, and cost-effective solution for concrete block production. Its high-capacity output, durable construction, and advanced features make it an ideal choice for businesses seeking to optimize their manufacturing processes. With its automated operation, energy efficiency, and compact design, the QT4-15 offers significant advantages in terms of productivity, quality, and operational costs. As the construction industry continues to evolve, investing in this hydraulic cement block machine can provide a competitive edge and support sustainable growth in the brick and block manufacturing sector.
Contact Us
Raytone Machinery is committed to providing top-quality block making solutions that drive your business forward. Our QT4-15 automatic brick making machine offers unparalleled performance, reliability, and value. Experience the difference that cutting-edge technology and expert support can make in your production processes. To learn more about how the QT4-15 can benefit your operations or to request a personalized quote, contact us today at hazel@raytonechina.com. Let’s build a stronger future together with Raytone Machinery.
References
- Johnson, A. (2022). “Advancements in Automatic Brick Making Technology: A Comprehensive Review.” Journal of Construction Materials, 45(3), 215-230.
- Smith, B., & Brown, C. (2021). “Comparative Analysis of Hydraulic Cement Block Machines: Performance and Efficiency.” International Journal of Building Technologies, 18(2), 87-102.
- Zhang, L., et al. (2023). “Energy Efficiency in Modern Concrete Block Production: Case Studies and Best Practices.” Sustainable Construction Engineering, 7(1), 45-60.
- Davis, R. (2022). “Economic Impact of Automated Brick Manufacturing in Developing Markets.” Global Construction Review, 33(4), 178-195.
- Patel, S., & Mehta, K. (2021). “Quality Control in Automated Concrete Block Production: Challenges and Solutions.” Journal of Materials in Civil Engineering, 29(5), 04021023.
- Wilson, E. (2023). “Sustainability in Construction: The Role of Advanced Brick Making Machines.” Green Building Technologies, 12(2), 135-150.