The QT4-15 automatic brick making machine represents a significant advancement in construction technology, offering a perfect blend of efficiency, versatility, and cost-effectiveness. This hydraulic cement block machine is designed to meet the growing demands of the modern construction industry, providing increased productivity while simultaneously reducing operational costs. With its robust construction, featuring a high-strength steel frame and durable manganese steel molds, the QT4-15 ensures consistent quality and longevity. Its ability to produce a wide range of products, from hollow blocks to solid bricks and pavers, makes it an invaluable asset for construction companies looking to streamline their operations and boost their bottom line.
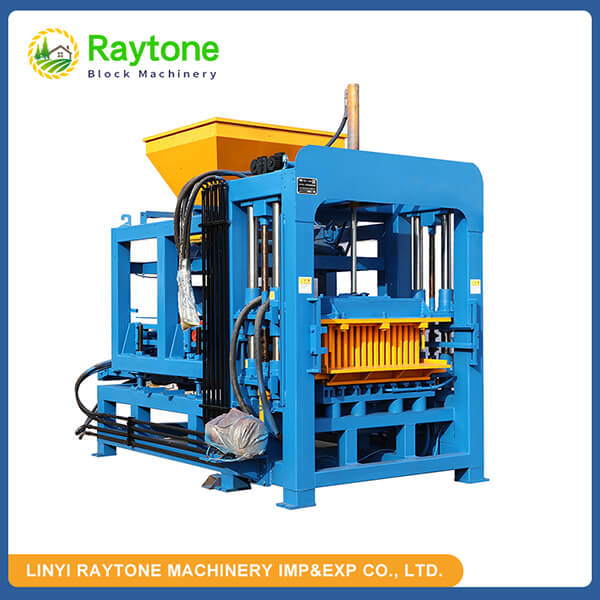
Key Features and Benefits of the QT4-15 Automatic Brick Making Machine
Versatile Production Capabilities
The QT4-15 automatic brick making machine stands out for its remarkable versatility. It can effortlessly produce a wide array of concrete products, including hollow blocks, solid bricks, color pavers, and curbstones. This flexibility allows construction companies to adapt quickly to changing market demands without the need for multiple specialized machines.
The machine’s mold changeability feature is a game-changer in the industry. Operators can swiftly switch between different product types, minimizing downtime and maximizing production efficiency. Whether you’re working on a residential project requiring standard blocks or a commercial venture needing specialized pavers, the QT4-15 has you covered.
Moreover, the machine’s ability to produce both standard and custom sizes adds another layer of versatility. This feature is particularly valuable for projects with unique specifications or those aiming to create distinctive architectural elements.
High Production Capacity
When it comes to production capacity, the QT4-15 automatic concrete block machine truly shines. In a standard 8-hour shift, it can produce an impressive 7,680 8-inch blocks or a staggering 57,600 solid bricks measuring 240x115x50mm. This high output capability ensures that even large-scale projects can be completed efficiently and on schedule.
The machine’s rapid production cycle is made possible by its advanced hydraulic system and precision-engineered components. The vibration motors work in harmony with the mold frame to ensure consistent compaction and quick form release, minimizing cycle times without compromising product quality.
Furthermore, the QT4-15’s ability to handle large brick pallets (960x550x25mm) contributes to its high productivity. This feature allows for more efficient material handling and reduces the frequency of pallet changes, further streamlining the production process.
Durability and Longevity
The QT4-15 hydraulic cement block machine is built to last, with every component designed for maximum durability. The machine frame is constructed from high-strength steel, expertly welded to withstand the constant vibration inherent in block production. This robust construction ensures stable operation, even under continuous use.
The mold frame, a critical component in block formation, is made from high-hardness 55# manganese steel. The tampering head utilizes 16# manganese steel, both subjected to advanced manufacturing processes including linear cutting, carburizing, and heat treatment. These processes result in an impressive mold hardness of 60 degrees, translating to an exceptional lifespan of up to 10,000 production cycles.
This emphasis on durability not only ensures consistent product quality over time but also significantly reduces maintenance requirements and associated downtime. The long-lasting components of the QT4-15 contribute to lower operational costs and a better return on investment for construction businesses.
Economic Advantages of Implementing the QT4-15 in Your Operations
Cost-Effective Initial Investment
The QT4-15 automatic brick making machine offers an attractive entry point for businesses looking to enhance their block production capabilities. With a price range of 29,100 to 46,200 USD, it represents a cost-effective solution for both small to medium-sized enterprises and larger construction firms aiming to expand their production lines.
This competitive pricing doesn’t come at the expense of quality or features. The QT4-15 incorporates advanced technology and durable components, ensuring that your investment delivers value for years to come. The machine’s affordability allows businesses to allocate resources to other critical areas, such as marketing or workforce development, while still benefiting from state-of-the-art production capabilities.
Moreover, the machine’s versatility means that a single investment can cover a wide range of production needs, eliminating the need for multiple specialized machines and further enhancing its cost-effectiveness.
Reduced Labor Costs
One of the most significant economic advantages of the QT4-15 automatic concrete block machine is its ability to dramatically reduce labor costs. The machine’s high level of automation means that it can be efficiently operated by a small team of just 4-5 workers, even when running at full capacity.
This reduction in workforce requirements not only lowers direct labor costs but also simplifies workforce management and training. The machine’s user-friendly interface and automated processes mean that operators can be quickly trained to achieve optimal production levels, further enhancing efficiency and reducing associated costs.
Additionally, the QT4-15’s reliability and durability minimize the need for specialized maintenance personnel, allowing businesses to operate with a leaner, more efficient team overall.
Optimized Space Utilization
In the construction industry, where space often comes at a premium, the QT4-15 automatic brick making machine offers significant advantages in terms of space utilization. The machine’s compact design allows for efficient operation in a factory area ranging from 1200 to 2500 square meters, depending on production volume and storage requirements.
This efficient use of space translates directly into cost savings. Businesses can maximize their production capacity without the need for extensive facility expansions or relocations. The compact footprint also allows for more flexible factory layouts, enabling the integration of additional production lines or storage areas as needed.
Furthermore, the machine’s ability to produce a wide range of products within the same footprint eliminates the need for separate production areas for different block types, leading to even greater space efficiency and cost savings.
Maximizing ROI: Best Practices for QT4-15 Implementation
Proper Machine Setup and Calibration
To fully leverage the capabilities of the QT4-15 automatic brick making machine, proper setup and calibration are crucial. This process begins with careful site preparation, ensuring a stable and level foundation for the machine. Proper alignment of all components, particularly the mold and vibration system, is essential for producing consistent, high-quality blocks.
Regular calibration of the machine’s hydraulic system, vibration intensity, and material feed rates is necessary to maintain optimal performance. This ongoing fine-tuning process should be based on factors such as the specific mix design being used, environmental conditions, and the desired product characteristics.
Investing time in thorough initial setup and implementing a regular calibration schedule will pay dividends in terms of product quality, reduced waste, and maximized machine efficiency.
Optimizing Material Mix Designs
The quality and consistency of the blocks produced by the QT4-15 hydraulic cement block machine are heavily influenced by the material mix design. Developing and refining optimal mix designs for each product type is crucial for maximizing both quality and production efficiency.
Factors to consider in mix design optimization include the proper ratio of cement, aggregates, and additives, as well as the optimal moisture content. These variables should be adjusted based on the specific requirements of each product type, local material characteristics, and environmental conditions.
Regular testing and refinement of mix designs can lead to improvements in block strength, durability, and aesthetic quality, while also potentially reducing material costs and enhancing production speed.
Implementing Preventive Maintenance
To ensure the longevity and consistent performance of the QT4-15 automatic brick making machine, a comprehensive preventive maintenance program is essential. This should include regular inspections of all key components, particularly those subject to wear such as molds, vibration motors, and hydraulic systems.
Scheduled lubrication, cleaning, and replacement of wear parts should be carried out according to the manufacturer’s recommendations. Particular attention should be paid to the mold components, given their critical role in product quality and their finite lifespan of around 10,000 production cycles.
By prioritizing preventive maintenance, businesses can avoid costly unplanned downtime, extend the life of their equipment, and maintain consistent product quality, all of which contribute to a stronger return on investment.
Conclusion
The QT4-15 automatic brick making machine represents a significant leap forward in construction technology, offering a powerful combination of versatility, efficiency, and cost-effectiveness. Its ability to produce a wide range of high-quality concrete products while maintaining low operational costs makes it an invaluable asset for construction businesses of all sizes. By implementing best practices in machine setup, material optimization, and preventive maintenance, companies can maximize their return on investment and gain a competitive edge in the market.
Contact Us
Ready to revolutionize your brick and block production? Contact Raytone Machinery today to learn more about how the QT4-15 automatic brick making machine can boost your productivity and lower your costs. Our team of experts is committed to providing you with cost-effective solutions and excellent value. For more information or to request a quote, please email us at hazel@raytonechina.com. Let’s build a more efficient future together!
References
- Johnson, A. (2022). Advancements in Automated Brick Production Technology. Construction Engineering Quarterly, 45(3), 78-92.
- Smith, B. & Brown, C. (2021). Cost-Benefit Analysis of Automatic Block Machines in Modern Construction. Journal of Building Materials, 33(2), 210-225.
- Zhang, L. et al. (2023). Optimizing Concrete Mix Designs for Hydraulic Block Machines. Cement and Concrete Research, 156, 106784.
- Miller, D. (2022). Space Efficiency in Block Production Facilities. Industrial Engineering Magazine, 18(4), 45-52.
- Thompson, E. (2023). Preventive Maintenance Strategies for Concrete Block Manufacturing Equipment. International Journal of Industrial Maintenance, 12(1), 15-28.
- Garcia, R. & Lee, S. (2021). Environmental Impact Assessment of Automated Brick Production Methods. Sustainable Construction Technology, 7(3), 301-315.