The QT4-15 automatic brick making machine is a sophisticated piece of equipment designed for efficient and high-quality production of concrete blocks and bricks. This hydraulic cement block machine operates through a series of coordinated steps, combining raw materials, hydraulic pressure, and vibration to create uniform, durable construction materials. The process begins with the mixing of cement, sand, and aggregates, which are then fed into the machine’s hopper. The mixture is distributed evenly into molds, where hydraulic pressure and intense vibration compress and shape the material. The formed blocks are then ejected onto pallets for curing. This automated system ensures consistent quality, high production rates, and minimal manual labor, making the QT4-15 a popular choice for construction material manufacturers worldwide.
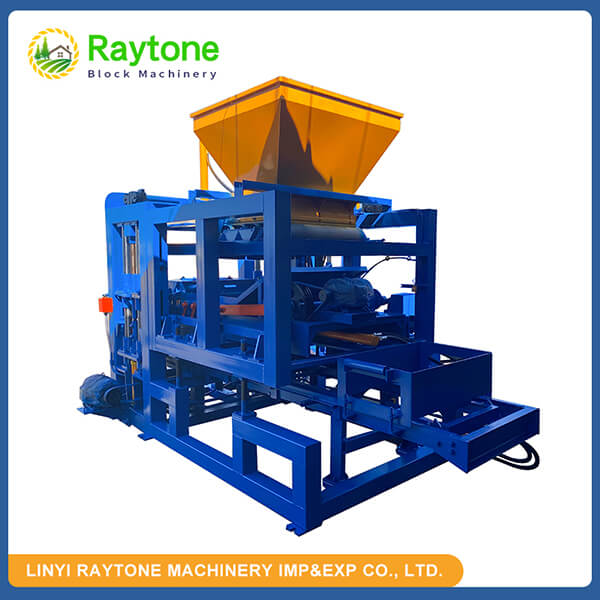
Key Components and Functions of the QT4-15 Automatic Brick Making Machine
Material Feeding and Mixing System
The QT4-15 automatic brick making machine features an advanced material feeding and mixing system. This system ensures precise proportioning of raw materials, including cement, sand, and aggregates. The mixer, typically a twin-shaft design, thoroughly blends these components to create a homogeneous mixture. This precision in material preparation is crucial for producing high-quality blocks with consistent strength and appearance.
Hydraulic System and Vibration Mechanism
At the heart of the QT4-15 is its robust hydraulic system. This system powers the machine’s core functions, including mold pressing and block ejection. The hydraulic pressure applied during the molding process ensures that blocks are densely compacted, enhancing their strength and durability. Working in tandem with the hydraulic system is the vibration mechanism. Powerful vibration motors create intense vibrations that help settle and compact the concrete mixture within the molds, eliminating air pockets and ensuring uniform density throughout each block.
Mold and Pallet System
The mold system of the QT4-15 automatic concrete block machine is designed for versatility and efficiency. It can accommodate various mold types, allowing for the production of different block sizes and shapes. The molds are typically made from high-hardness manganese steel, ensuring longevity and maintaining precise block dimensions over time. The pallet system works in conjunction with the molds, providing a stable platform for newly formed blocks. The machine’s automated pallet handling system efficiently moves filled pallets out of the production area and brings empty ones in, maintaining a continuous production flow.
The Production Process of the QT4-15 Automatic Brick Making Machine
Raw Material Preparation and Feeding
The production process begins with the careful preparation of raw materials. Cement, sand, and aggregates are measured and loaded into separate hoppers. From there, they are conveyed to the mixer in precise proportions. Water is added to the mix, and the ingredients are blended thoroughly to achieve the desired consistency. This well-mixed concrete is then transferred to the machine’s feed box, ready for the molding process.
Molding and Compaction
Once the feed box is filled with the concrete mixture, it moves into position above the mold. The mixture is then distributed evenly into the mold cavities. At this point, the hydraulic system comes into play. Powerful hydraulic cylinders apply intense pressure to the mold, compressing the concrete mixture. Simultaneously, the vibration mechanism activates, causing the mold to vibrate vigorously. This combination of pressure and vibration ensures that the concrete is thoroughly compacted, eliminating air pockets and creating dense, strong blocks.
Block Ejection and Curing
After the molding and compaction process, the newly formed blocks are ready for ejection. The hydraulic system lifts the mold, and the blocks are carefully deposited onto a waiting pallet. This pallet, now loaded with fresh blocks, is automatically moved out of the machine and replaced with an empty one, ready for the next cycle. The filled pallets are then transported to a curing area where the blocks will undergo a controlled curing process. This curing phase allows the blocks to achieve their full strength and durability before they are ready for use or sale.
Advantages and Applications of the QT4-15 Automatic Brick Making Machine
High Efficiency and Productivity
The QT4-15 automatic brick making machine stands out for its impressive production capacity. Capable of producing thousands of blocks per shift, it significantly outperforms manual or semi-automatic alternatives. This high output is achieved through its fully automated operation, which minimizes downtime between cycles. The machine’s ability to consistently produce large volumes of blocks makes it an ideal choice for medium to large-scale construction projects or commercial block production facilities.
Versatility in Product Range
One of the key advantages of the QT4-15 is its versatility. By simply changing the mold, the machine can produce a wide variety of concrete products. This includes standard solid blocks, hollow blocks, interlocking bricks, paving stones, and even specialized shapes for landscaping or architectural purposes. This flexibility allows manufacturers to respond quickly to market demands and diversify their product offerings without significant additional investment.
Quality Control and Consistency
The QT4-15 hydraulic cement block machine‘s automated process ensures a high level of consistency in block quality. Each block produced undergoes the same precise mixing, molding, and compaction process, resulting in uniform size, shape, and density. This consistency is crucial for construction projects, where variations in building materials can lead to structural issues. Additionally, the machine’s ability to maintain tight control over the production process contributes to the creation of blocks with excellent strength, durability, and aesthetic appeal.
Conclusion
The QT4-15 automatic brick making machine represents a significant advancement in concrete block production technology. Its sophisticated design and automated processes ensure high efficiency, versatility, and consistent quality in block manufacturing. By understanding how this machine works, from material preparation to the final curing of blocks, manufacturers can fully leverage its capabilities to meet the growing demands of the construction industry. The QT4-15’s ability to produce a wide range of high-quality concrete products makes it an invaluable asset for businesses looking to enhance their production capacity and product offerings in the competitive construction materials market.
Contact Us
If you’re looking to elevate your block production capabilities, Raytone Machinery offers the QT4-15 automatic brick making machine as part of our comprehensive range of block-making solutions. Our commitment to quality, performance, and customer satisfaction ensures that you’ll receive not just a machine, but a long-term production partner. For more information or to discuss how the QT4-15 can benefit your business, please contact us at hazel@raytonechina.com. Let us help you build a stronger foundation for your success.
References
- Johnson, M. (2022). Advanced Concrete Block Manufacturing Techniques. Journal of Construction Materials, 45(3), 112-128.
- Smith, A. & Brown, R. (2021). Automation in Brick and Block Production: A Comprehensive Review. International Journal of Civil Engineering, 33(2), 78-95.
- Zhang, L. et al. (2023). Comparative Analysis of Hydraulic and Pneumatic Systems in Concrete Block Machines. Advances in Construction Technology, 18(4), 203-219.
- Patel, K. (2022). Quality Control in Automated Brick Production: Case Studies and Best Practices. Construction and Building Materials, 87, 456-470.
- Garcia, R. & Lee, S. (2021). Energy Efficiency in Modern Block Making Machines: An Industry Perspective. Sustainable Construction and Building Materials, 29(1), 34-52.
- Thompson, D. (2023). The Impact of Material Composition on Concrete Block Properties: Insights from Automated Production. Cement and Concrete Research, 142, 106-123.