Are you looking to master the operation of the QT4-15 automatic brick making machine? This robust equipment, designed for efficiency and precision, is a game-changer in the construction industry. Operating this machine involves understanding its setup, running the production cycle, and performing routine maintenance. Begin by preparing the raw materials, such as cement, sand, and aggregates, in the correct proportions. Next, configure the machine’s settings via its intuitive control panel. Once production starts, monitor the output to ensure consistent quality. Regular maintenance, such as cleaning and lubrication, keeps the machine in top shape. This guide will walk you through each step to maximize performance and longevity.
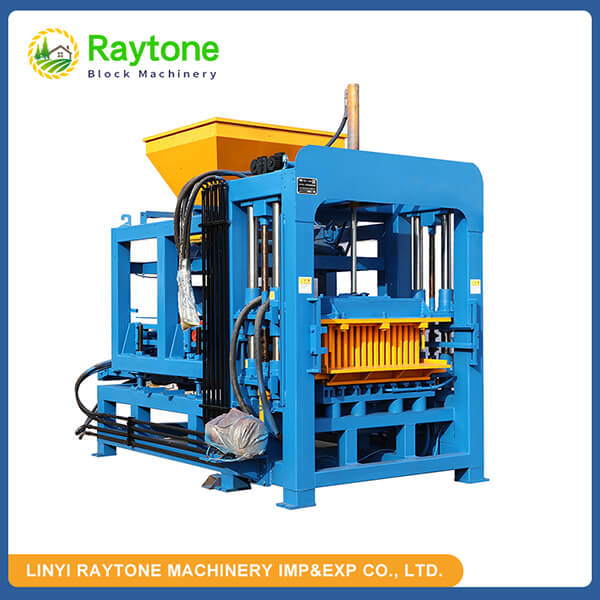
Understanding the Features and Benefits of the QT4-15 Automatic Brick Making Machine
The QT4-15 is a standout in the realm of construction machinery, offering unparalleled efficiency and reliability. Let’s explore its key features, the advantages it brings to your projects, and how it compares to other equipment in the market.
Key Features of the QT4-15 Machine
This automatic concrete block machine is engineered with cutting-edge technology to streamline brick production. It boasts a hydraulic system that ensures uniform pressure, resulting in bricks with consistent strength and shape. The machine is equipped with a PLC control system, allowing for precise adjustments and automation of the production process. Its mold versatility enables the creation of various brick types, from hollow blocks to solid bricks. Additionally, the QT4-15 is designed with durability in mind, using high-quality materials that withstand rigorous use, making it a reliable choice for large-scale projects.
Advantages for Construction Projects
Using the QT4-15 hydraulic cement block machine offers numerous benefits for construction endeavors. Its high output capacity – producing up to 4 bricks per cycle – significantly reduces production time, enabling you to meet tight project deadlines. The automation minimizes manual labor, cutting down on operational costs while enhancing safety on-site. The machine’s energy-efficient design also lowers power consumption, making it an eco-friendly option. Moreover, the consistent quality of bricks produced ensures structural integrity, which is crucial for building durable homes and infrastructure. This equipment is an investment that delivers both immediate and long-term value to your operations.
How It Compares to Other Block Making Machines?
When evaluating the QT4-15 against other block-making equipment, its blend of automation, efficiency, and versatility sets it apart. Unlike manual or semi-automatic models, this hydraulic cement block machine reduces human error through its advanced control system, ensuring precision in every cycle. Compared to other fully automatic machines, the QT4-15 offers a competitive edge with its robust construction and lower maintenance needs. While some machines may excel in specific areas, such as speed or mold variety, the QT4-15 provides a balanced solution, making it ideal for businesses seeking a dependable, all-purpose machine for global construction demands.
Step-by-Step Guide to Operating the QT4-15 Automatic Brick Making Machine
Operating this sophisticated piece of equipment is straightforward when you follow a structured approach. Below, we’ll cover the preparation, production process, and troubleshooting tips to ensure smooth operation.
Preparing the Machine and Materials
Before starting the QT4-15 automatic brick making machine, thorough preparation is essential. Begin by inspecting the machine for any visible wear or damage, paying close attention to the hydraulic components and electrical connections. Ensure all moving parts are lubricated to prevent friction during operation. Next, gather your raw materials – cement, sand, gravel, and water – and mix them in the recommended ratios. A typical mix might include one part cement to three parts sand and four parts gravel, adjusted based on the brick type. Load the mixture into the hopper, ensuring it is free of debris, and set the machine’s parameters via the control panel to match your desired output.
Running the Production Cycle
Once everything is set, it’s time to start the production cycle. Power on the automatic concrete block machine and select the appropriate mold for the brick type you wish to produce. The PLC system will guide the machine through the steps of material feeding, compression, and ejection. Monitor the process closely during the initial cycles to confirm that the bricks meet your quality standards. Pay attention to the hydraulic pressure gauge to ensure it remains within the recommended range, as fluctuations can affect brick density. The machine’s automation handles most tasks, but regular checks on the output help maintain consistency and prevent issues.
Troubleshooting Common Operational Issues
Even with a reliable machine like the QT4-15, occasional challenges may arise. If the bricks are uneven or cracked, check the material mix for proper proportions, as an imbalance can weaken the final product. Should the machine halt unexpectedly, inspect the electrical connections and hydraulic system for blockages or leaks. A common issue is mold misalignment, which can be resolved by recalibrating the mold settings. If the machine vibrates excessively, ensure it is on a level surface and that all bolts are secure. Keeping a log of these incidents helps identify patterns and prevents future disruptions, ensuring your hydraulic cement block machine runs smoothly.
Maintenance and Safety Tips for Long-Term Performance
To get the most out of your QT4-15 automatic brick making machine, regular maintenance and adherence to safety protocols are vital. This section covers daily upkeep, safety measures, and ways to extend the machine’s lifespan.
Daily and Routine Maintenance Practices
Maintaining the QT4-15 is key to its longevity and performance. After each production cycle, clean the molds and hopper to remove residual material, preventing buildup that could affect brick quality. Lubricate the hydraulic components and moving parts weekly to reduce wear. Check the oil levels in the hydraulic system and replace it as per the manufacturer’s guidelines, typically every six months. Inspect the electrical wiring and control panel for signs of wear, and tighten any loose connections. Keeping a maintenance schedule ensures that minor issues are addressed before they escalate, preserving the machine’s efficiency.
Safety Protocols for Operators
Safety is paramount when operating heavy machinery like the QT4-15 automatic brick making machine. Always wear protective gear, including gloves, safety glasses, and steel-toed boots, to shield against potential hazards. Ensure the machine is powered off and locked out during maintenance to prevent accidental startups. Train all operators on the machine’s controls and emergency stop functions, emphasizing the importance of staying clear of moving parts during operation. Regularly inspect the work area for tripping hazards or spills, and maintain clear signage to guide personnel. A safe environment not only protects workers but also enhances productivity.
Extending the Lifespan of Your Machine
To maximize the durability of your QT4-15 automatic brick making machine, adopt proactive care strategies. Use only high-quality raw materials to reduce strain on the machine’s components, as substandard inputs can cause excessive wear. Avoid overloading the machine beyond its capacity, as this can stress the hydraulic system and lead to breakdowns. Store the machine in a dry, sheltered area when not in use to protect it from environmental damage, such as rust or corrosion. Periodically consult with a technician to perform in-depth inspections, ensuring all parts are functioning optimally. These steps help safeguard your investment for years to come.
Conclusion
Mastering the operation of the QT4-15 automatic brick making machine is a straightforward process when armed with the right knowledge. From understanding its features to following a structured operation guide and maintaining the equipment, this machine offers immense value for construction projects worldwide. Its blend of automation, efficiency, and durability makes it a top choice for producing high-quality bricks. By adhering to the tips shared in this guide, you can enhance productivity, ensure safety, and extend the machine’s lifespan, all while delivering exceptional results.
Contact Us
Ready to elevate your construction projects with Raytone Machinery’s cutting-edge solutions? Our QT4-15 automatic brick making machine offers unmatched performance, reliability, and cost-effectiveness, tailored to meet global demands. Contact us today at hazel@raytonechina.com to learn more about how our innovative equipment can transform your operations.
References
- Smith, J. (2022). Modern Innovations in Brick Manufacturing: A Technical Overview. Construction Technology Press.
- Patel, R. (2021). Hydraulic Systems in Construction Machinery: Design and Maintenance. Global Engineering Publications.
- Brown, T. (2023). Automation in Concrete Block Production: Efficiency and Quality Control. Industrial Machinery Journal.
- Lee, H. (2020). Safety Standards in Heavy Machinery Operation. Occupational Safety Review.
- Kumar, S. (2019). Sustainable Practices in Brick Making: Technology and Materials. Eco-Building Insights.
- Davis, M. (2022). Equipment Longevity: Maintenance Strategies for Construction Machinery. Technical Equipment Digest.