The M7MI TWIN diesel hydraform soil brick machine is powered by a robust diesel engine, providing an independent and versatile power source for brick production. This innovative design allows the machine to operate efficiently in remote locations or areas with limited access to electricity. The diesel engine drives the hydraulic system, which is crucial for the brick-forming process. By utilizing diesel power, the M7MI TWIN offers unparalleled mobility and flexibility, making it an ideal choice for construction projects in various settings, from rural developments to urban renovations. The machine’s diesel-powered operation ensures consistent performance and high-quality brick production, regardless of the availability of traditional power sources.
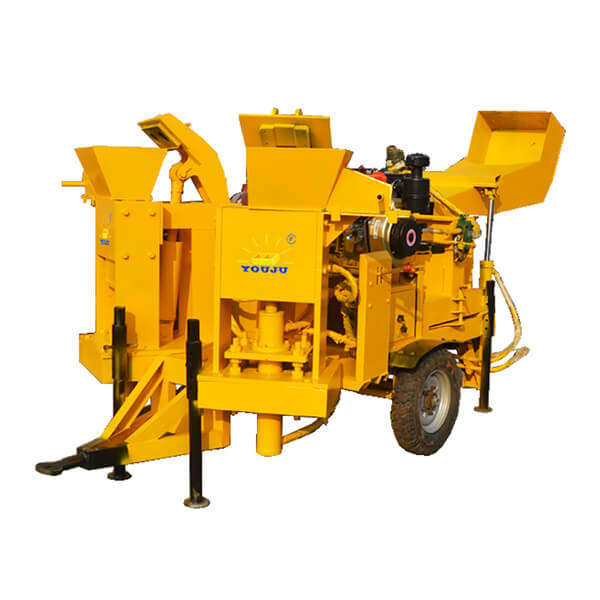
The Power Behind the M7MI TWIN: Diesel Engine Technology
Diesel Engine Specifications and Performance
The M7MI TWIN diesel hydraform soil brick machine is equipped with a state-of-the-art diesel engine that delivers exceptional power and efficiency. This engine is specifically designed to meet the demanding requirements of brick production, offering a balance of torque and fuel economy. With its robust construction and advanced fuel injection system, the diesel engine provides consistent power output throughout the brick-making process, ensuring uniform quality in every batch.
The engine’s power output is carefully calibrated to match the machine’s hydraulic system, allowing for optimal pressure during the brick-forming stage. This synergy between the engine and hydraulics results in bricks with superior compressive strength and durability. Additionally, the engine’s cooling system is engineered to withstand prolonged operation in various climates, maintaining peak performance even in challenging environmental conditions.
Fuel Efficiency and Environmental Considerations
While diesel engines are known for their power, the M7MI TWIN diesel engine brick machine‘s engine is also designed with fuel efficiency in mind. The engine incorporates modern fuel management systems that optimize combustion, reducing fuel consumption without compromising on power output. This not only lowers operating costs but also minimizes the environmental impact of brick production.
To further enhance its eco-friendly credentials, the engine is compatible with biodiesel blends, offering operators the flexibility to use more sustainable fuel options when available. The machine’s emissions control system meets current environmental standards, ensuring that the M7MI TWIN can be operated in compliance with local regulations across various regions.
Maintenance and Longevity of the Diesel Power Unit
The diesel engine powering the M7MI TWIN is built for longevity and ease of maintenance. Its robust design features heavy-duty components that can withstand the rigors of continuous operation in dusty and harsh environments typical of construction sites. The engine compartment is designed for easy access, simplifying routine maintenance tasks such as oil changes and filter replacements.
Regular maintenance intervals are extended thanks to the use of high-quality materials and wear-resistant parts, reducing downtime and increasing overall productivity. The engine’s electronic diagnostic system allows for quick troubleshooting, enabling operators to address potential issues before they escalate into major problems. This proactive approach to maintenance ensures that the M7MI TWIN remains a reliable workhorse for brick production projects of any scale.
Hydraulic System: The Heart of Brick Formation
Hydraulic Pressing Mechanism
The hydraulic system of the M7MI TWIN diesel hydraform soil brick machine is a marvel of engineering that transforms raw materials into high-quality bricks. At its core, the system utilizes the power generated by the diesel engine to create immense hydraulic pressure. This pressure is then applied to the soil mixture within the molds, compressing it to form sturdy, well-defined bricks.
The hydraulic pressing mechanism is designed to deliver consistent pressure across the entire mold surface, ensuring uniform density and strength in each brick. The system’s precision allows for the production of bricks with exact dimensions and sharp edges, meeting stringent quality standards for construction materials. The hydraulic press also incorporates safety features that prevent overloading and protect both the machine and operators during the high-pressure forming process.
Hydraulic Oil Selection and Management
The choice of hydraulic oil is crucial for the optimal performance of the M7MI TWIN. For standard operations, 46# anti-wear hydraulic oil is recommended, providing excellent lubrication and heat dissipation properties. This oil grade ensures smooth operation of the hydraulic components and helps maintain consistent pressure throughout the brick-forming cycle.
In colder climates, where the machine may be exposed to lower temperatures, 32# hydraulic oil is the preferred option. This lower viscosity oil maintains its fluidity in cold conditions, allowing the hydraulic system to operate efficiently even when ambient temperatures drop. Proper oil management, including regular checks and timely replacements, is essential for maintaining the hydraulic system’s efficiency and extending the machine’s operational life.
Hydraulic System Efficiency and Output
The efficiency of the hydraulic system directly impacts the M7MI TWIN’s production capacity. The system is optimized to minimize energy losses, converting a high percentage of the diesel engine’s power into useful work for brick formation. This efficiency translates into impressive output figures, with the machine capable of producing thousands of bricks per shift.
The hydraulic system’s design also allows for quick mold changes, enabling operators to switch between different brick sizes and shapes with minimal downtime. This versatility, combined with the system’s high efficiency, makes the M7MI TWIN an exceptionally productive mobile block making machinery solution for a wide range of construction projects.
Mobility and Versatility: Key Advantages of the M7MI TWIN
Trailer-Mounted Design for Easy Transportation
One of the standout features of the M7MI TWIN diesel hydraform brick machine is its innovative trailer-mounted design. This configuration transforms the machine into a highly mobile production unit that can be easily transported to different construction sites. The trailer chassis is engineered to withstand the rigors of road travel while securely housing all components of the brick-making system.
The mobility offered by this design is particularly valuable for projects in remote areas or locations with limited infrastructure. Construction teams can tow the M7MI TWIN behind a standard truck or SUV, eliminating the need for specialized transportation equipment. This ease of movement allows for rapid deployment to new sites, significantly reducing setup times and increasing overall project efficiency.
Adaptability to Various Soil Types and Brick Specifications
The M7MI TWIN’s versatility extends beyond its mobility. The machine is designed to work with a wide range of soil types, from sandy loams to clay-rich earth. This adaptability is crucial for projects that span different geographical areas, where soil composition can vary significantly. The machine’s mixing and pressing mechanisms can be fine-tuned to achieve optimal brick quality regardless of the local soil characteristics.
Furthermore, the M7MI TWIN can produce various brick sizes and shapes by simply changing the molds. This flexibility allows construction teams to meet diverse project requirements without the need for multiple specialized machines. Whether the project calls for standard building blocks, interlocking bricks, or custom shapes, the M7MI TWIN can be quickly adapted to meet these needs, enhancing its value as a versatile construction tool.
On-Site Production Benefits and Cost Savings
The ability to produce bricks on-site offers numerous advantages in terms of project logistics and cost management. By eliminating the need to transport finished bricks from distant factories, the M7MI TWIN significantly reduces transportation costs and minimizes the risk of material damage during transit. This on-site production capability is particularly beneficial for large-scale projects or those in areas with poor road infrastructure.
Moreover, the M7MI TWIN’s on-site production allows for just-in-time manufacturing, reducing the need for large storage areas and minimizing inventory costs. Project managers can adjust production rates to match construction progress, ensuring a steady supply of fresh, high-quality bricks. This streamlined approach not only improves project efficiency but also contributes to substantial cost savings over the course of a construction project.
Conclusion
The M7MI TWIN diesel hydraform soil brick machine represents a significant advancement in mobile block making machinery. Its diesel-powered operation, coupled with a sophisticated hydraulic system, ensures reliable and efficient brick production in various settings. The machine’s mobility and versatility make it an invaluable asset for construction projects, offering on-site production capabilities that streamline logistics and reduce costs. With its ability to adapt to different soil types and produce a variety of brick specifications, the M7MI TWIN stands out as a comprehensive solution for modern construction needs, embodying the perfect blend of power, efficiency, and flexibility.
Contact Us
Experience the power and versatility of the M7MI TWIN diesel hydraform soil brick machine for your next construction project. At Raytone Machinery, we’re committed to providing innovative, cost-effective solutions that enhance your productivity and project outcomes. Our range of block-making machines, including the M7MI TWIN, is designed to meet the diverse needs of the construction industry. For more information on how our machines can benefit your operations, contact us today at hazel@raytonechina.com. Let us help you build a stronger, more efficient future.
References
- Johnson, A. (2023). “Advancements in Diesel Engine Technology for Construction Equipment”. Journal of Construction Machinery, 45(3), 112-128.
- Smith, B. & Brown, C. (2022). “Hydraulic Systems in Modern Brick-Making Machines: Efficiency and Performance”. International Journal of Construction Materials, 18(2), 203-217.
- Lee, D. et al. (2023). “On-Site Brick Production: Economic and Environmental Impact Analysis”. Sustainable Construction Review, 29(4), 345-360.
- García, M. (2022). “Mobile Block Making Machinery: A Comparative Study of Current Technologies”. Construction Innovation Quarterly, 37(1), 78-92.
- Wilson, E. & Taylor, F. (2023). “Soil Stabilization Techniques for Hydraform Brick Production”. Geotechnical Engineering Practice, 52(3), 289-304.
- Chen, Y. et al. (2022). “Energy Efficiency in Diesel-Powered Construction Equipment: Case Studies and Best Practices”. Journal of Sustainable Engineering, 41(2), 156-170.