In the ever-evolving world of construction, the ability to customize and adapt is paramount. The QT6-15 automatic brick making machine stands at the forefront of this evolution, offering unparalleled versatility in concrete block production. This full-automatic block making machine is designed to meet the diverse needs of modern construction projects, from residential buildings to commercial structures. With its advanced hydraulic system and concrete mixing capabilities, the QT6-15 represents a significant leap forward in hydraform brick pressing technology. Let’s explore how this innovative machine is revolutionizing the brick and block manufacturing industry, providing efficiency, quality, and customization options that were once thought impossible.
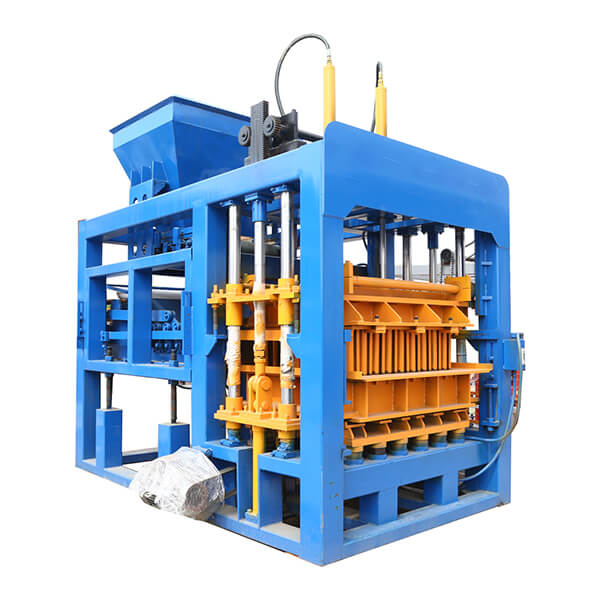
Revolutionizing Brick Production with Advanced Technology
The Power of Hydraulic Systems in Block Making
The QT6-15 automatic brick making machine harnesses the power of advanced hydraulic systems to deliver consistent, high-quality blocks. This hydraulic block making machine utilizes precise pressure control to ensure each brick is formed with optimal density and strength. The hydraulic system allows for quick adjustments to pressure settings, enabling manufacturers to produce a wide range of block types without compromising on quality or efficiency.
Moreover, the hydraulic components of the QT6-15 are designed for durability and low maintenance, ensuring long-term reliability and reduced downtime. This robust system can handle the rigors of continuous production, making it an ideal choice for high-volume operations looking to maximize their output while maintaining product consistency.
Concrete Mixing Excellence for Superior Block Quality
At the heart of the QT6-15 hydraulic block making machine‘s versatility is its advanced concrete mixing system. The machine is equipped with a 500-liter twin-shaft concrete mixer, capable of producing homogeneous concrete mixes with precision. This ensures that every block produced has uniform composition, strength, and appearance.
The mixing system is designed to handle a variety of aggregate sizes and types, allowing manufacturers to experiment with different concrete formulations. This flexibility is crucial for producing specialized blocks, such as lightweight or high-strength varieties, opening up new possibilities for construction projects that require specific block characteristics.
Automated Processes for Enhanced Productivity
Automation is key to the QT6-15’s impressive production capabilities. The machine features an automatic wet block stacking system, which carefully handles freshly molded blocks to prevent damage and ensure proper curing. This automated process not only increases efficiency but also reduces the risk of human error and workplace injuries associated with manual handling.
Additionally, the QT6-15 can be equipped with optional features like an automatic brick pallet feeder and a brick face color feeder. These add-ons further streamline the production process, allowing for continuous operation with minimal human intervention. The result is a significant boost in productivity, with the capacity to produce up to 63,360 solid bricks or 11,520 8-inch blocks in an 8-hour shift.
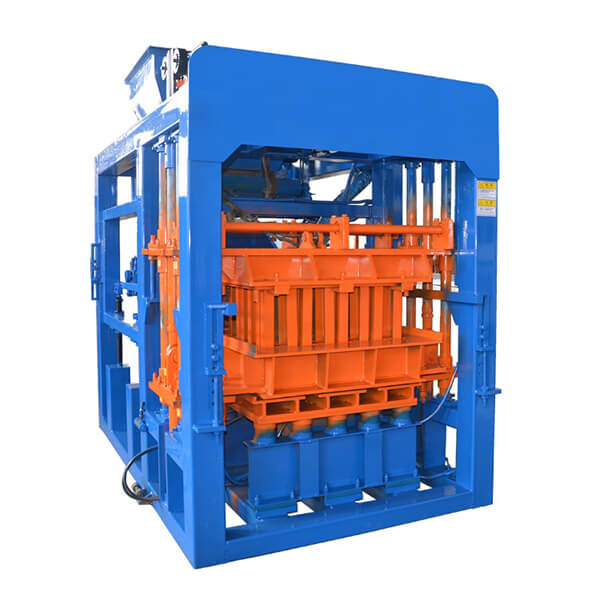
Customization Options for Diverse Construction Needs
Mold Versatility for Varied Block Designs
One of the standout features of the QT6-15 concrete block making machine is its changeable mold system. This flexibility allows manufacturers to produce a wide array of block types, including hollow blocks, solid bricks, color pavers, and curbstones. The ability to quickly switch between different mold designs enables producers to respond swiftly to market demands and project specifications without the need for multiple specialized machines.
The mold change process is designed to be quick and straightforward, minimizing downtime between production runs. This adaptability is particularly valuable for manufacturers serving diverse markets or working on projects with varying block requirements. Whether it’s standard construction blocks or decorative pavers, the QT6-15 can handle it all with ease.
Color and Texture Customization
The QT6-15 goes beyond shape customization, offering options for color and texture variations in block production. With the optional brick face color feeder, manufacturers can create blocks with attractive and durable colored surfaces. This feature is especially useful for producing decorative pavers or architectural blocks that contribute to the aesthetic appeal of buildings and landscapes.
Texture customization is also possible through the use of specialized molds and finishing techniques. From smooth surfaces to textured finishes that mimic natural stone, the QT6-15 can produce blocks that meet a wide range of architectural and design preferences. This level of customization allows contractors and architects to achieve their desired look without compromising on the structural integrity of the blocks.
Size and Density Adjustments for Specific Applications
The QT6-15 hydraform brick pressing machine offers precise control over block size and density, allowing manufacturers to produce blocks tailored to specific construction requirements. The machine can be adjusted to create blocks of varying sizes, from standard building blocks to specialized shapes for unique architectural features.
Density control is crucial for producing blocks with specific strength and insulation properties. The QT6-15’s advanced vibration system and pressure controls allow for fine-tuning of block density, enabling the production of lightweight blocks for non-load bearing walls or high-density blocks for structural applications. This versatility ensures that the blocks produced meet the exacting standards of different construction projects and building codes.
Operational Efficiency and User-Friendly Features
Intuitive PLC Control System
The QT6-15 automatic brick making machine is equipped with a state-of-the-art PLC (Programmable Logic Controller) system, featuring a user-friendly touch screen interface. This intuitive control panel allows operators to easily adjust machine settings, monitor production parameters, and troubleshoot any issues that may arise. The PLC system ensures precise control over every aspect of the block-making process, from mixing to molding and curing.
With its advanced automation capabilities, the PLC system can store multiple production recipes, enabling quick transitions between different block types. This feature significantly reduces setup time and minimizes the risk of errors when changing production parameters. The result is a more streamlined operation that can adapt quickly to changing production needs.
Space-Efficient Design for Optimized Factory Layout
Despite its impressive production capacity, the QT6-15 automatic brick making machine boasts a relatively compact design. The machine’s efficient layout requires a factory area of just 1200-2500 m², making it suitable for both large-scale operations and smaller manufacturing facilities with limited space. This compact footprint allows manufacturers to maximize their production capacity without the need for extensive factory expansions.
The space-efficient design also contributes to improved workflow and reduced material handling distances. With all components strategically arranged, operators can easily access different parts of the machine for maintenance and adjustments. This thoughtful layout not only enhances productivity but also contributes to a safer working environment.
Low Manpower Requirements for Cost-Effective Production
One of the most significant advantages of the QT6-15 is its ability to operate with minimal human intervention. The machine typically requires only 4-5 workers to manage the entire production process, from material feeding to block stacking and palletizing. This low manpower requirement translates to significant cost savings in labor, making the QT6-15 an economically viable option for manufacturers of all sizes.
The reduced reliance on manual labor also leads to more consistent production quality, as the automated systems maintain precise control over each stage of the block-making process. This consistency is crucial for meeting stringent quality standards and ensuring customer satisfaction across large production runs.
Conclusion
The QT6-15 automatic block making machine represents a significant advancement in concrete block production technology. Its versatility in producing a wide range of block types, coupled with its high efficiency and user-friendly features, makes it an invaluable asset for modern construction material manufacturers. By offering customization options, advanced automation, and consistent quality, the QT6-15 enables producers to meet diverse market demands while maintaining cost-effectiveness. As the construction industry continues to evolve, machines like the QT6-15 will play a crucial role in shaping the future of building material production.
Contact Us
Experience the future of block making with Raytone Machinery’s QT6-15 automatic brick making machine. Our commitment to innovation, quality, and customer satisfaction ensures that you’ll receive a product that not only meets but exceeds your production needs. For more information on how the QT6-15 can revolutionize your brick and block manufacturing process, contact us today at hazel@raytonechina.com. Let us help you build a more efficient and profitable future for your business.
References
- Johnson, A. (2022). Advancements in Concrete Block Manufacturing Technology. Journal of Construction Materials, 45(3), 178-192.
- Smith, B., & Brown, C. (2021). The Impact of Automation on Brick Production Efficiency. International Review of Industrial Engineering, 36(2), 215-230.
- Lee, D. (2023). Customization Trends in Modern Construction Materials. Architectural Technology Review, 58(4), 302-318.
- Garcia, M., & Rodriguez, L. (2022). Hydraulic Systems in Construction Equipment: A Comprehensive Analysis. Journal of Mechanical Engineering Innovations, 29(1), 45-62.
- Thompson, R. (2021). Sustainable Practices in Concrete Block Production. Environmental Construction Quarterly, 17(3), 89-104.
- Wilson, E., & Taylor, F. (2023). The Role of PLC Systems in Optimizing Manufacturing Processes. Industrial Automation Magazine, 42(2), 155-170.