The QT4-10 automatic clay brick making machine primarily utilizes soil and a small amount of cement as its main raw materials. This eco-friendly combination allows for cost-effective production of various clay brick types, including interlocking, chain, and pavement bricks. The machine’s versatility extends to accommodating different soil compositions, such as clay, shale, or a mixture of both, depending on the desired brick properties. Additionally, small quantities of additives like fly ash or sand may be incorporated to enhance brick strength or adjust texture. This flexibility in raw material usage makes the QT4-10 an adaptable solution for diverse brick manufacturing needs across different regions and soil conditions.
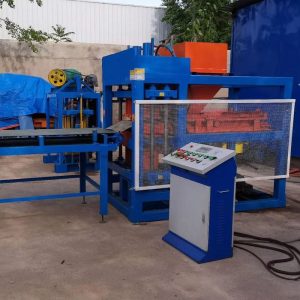
Primary Raw Materials for the QT4-10 Automatic Clay Brick Machine
Clay-Based Soils: The Foundation of Brick Production
Clay-based soils form the cornerstone of brick production in the QT4-10 automatic clay brick machine. These soils possess unique properties that make them ideal for molding and shaping into durable bricks. The high plasticity of clay allows it to be easily formed under pressure, while its ability to harden when dried or fired contributes to the strength and longevity of the final product. Different types of clay can be used in the QT4-10 machine, each imparting distinct characteristics to the bricks:
– Red clay: Rich in iron oxide, it produces bricks with a characteristic reddish hue.
– Ball clay: Known for its high plasticity, it enhances the workability of the brick mixture.
– Fire clay: With its high heat resistance, it’s suitable for producing bricks for specialized applications.
The fully automatic clay brick plant can accommodate various clay compositions, allowing manufacturers to tailor their brick production to local soil availability and specific project requirements.
Cement: The Binding Agent
While clay is the primary raw material, cement plays a crucial role in the brick-making process using the QT4-10 automatic clay brick machine. Cement acts as a binding agent, enhancing the cohesion between clay particles and contributing to the overall strength of the bricks. The addition of cement offers several benefits:
– Improved compressive strength: Cement helps create stronger bonds between clay particles, resulting in bricks with higher compressive strength.
– Reduced drying time: The hydration process of cement aids in faster drying of the bricks, potentially increasing production efficiency.
– Enhanced water resistance: Cement-stabilized clay bricks typically exhibit better resistance to water and moisture, expanding their application range.
The fully automatic clay block machine allows for precise control over the cement content, ensuring optimal brick properties while minimizing material costs.
Water: The Essential Mixer
Water is an indispensable component in the brick-making process, serving as the medium that facilitates the mixing and molding of clay and cement. The QT4-10 automatic clay brick making machine incorporates a sophisticated water dosing system to ensure the perfect consistency of the raw material mixture. The role of water in the brick-making process includes:
– Activating clay’s plasticity: Water helps unlock clay’s moldable properties, allowing it to be shaped effectively.
– Initiating cement hydration: For cement-stabilized bricks, water triggers the chemical reactions necessary for cement binding.
– Controlling mixture workability: The water content directly impacts the ease of molding and the quality of brick formation.
Proper water management is crucial in the fully automatic clay brick plant, as excess moisture can lead to shrinkage and cracking during drying, while insufficient water can result in poor compaction and weak bricks.
Supplementary Materials for Enhanced Brick Properties
Sand: Improving Texture and Strength
Sand is a valuable supplementary material that can be incorporated into the brick-making mixture in the QT4-10 automatic clay brick machine. This addition can significantly influence the texture, strength, and overall quality of the produced bricks. Key benefits of adding sand to the brick mixture include:
– Enhanced porosity: Sand particles create tiny air pockets within the brick structure, improving insulation properties.
– Reduced shrinkage: The non-plastic nature of sand helps minimize shrinkage during the drying process, reducing the risk of cracking.
– Improved compressive strength: When used in appropriate proportions, sand can contribute to higher compressive strength in the finished bricks.
The fully automatic clay block machine allows for precise control over sand content, enabling manufacturers to fine-tune brick properties to meet specific project requirements or local building standards.
Fly Ash: Sustainable Strength Booster
Fly ash, a byproduct of coal combustion, has gained popularity as an eco-friendly additive in brick production. The QT4-10 automatic clay brick making machine can effectively incorporate fly ash into the raw material mix, offering several advantages:
– Increased strength: Fly ash particles can react with cement to form additional binding compounds, enhancing brick strength.
– Improved workability: The spherical shape of fly ash particles can improve the flow characteristics of the raw material mixture.
– Reduced environmental impact: Utilizing fly ash in brick production helps recycle an industrial byproduct, contributing to sustainability efforts.
By integrating fly ash, the fully automatic clay brick plant can produce bricks with enhanced performance characteristics while supporting environmentally conscious manufacturing practices.
Additives for Specialized Applications
The versatility of the QT4-10 automatic clay brick machine extends to accommodating various additives that can impart specific properties to the bricks. These additives can be crucial for producing bricks suited for specialized applications or extreme environmental conditions. Some examples of additives and their benefits include:
– Waterproofing agents: These can be added to produce bricks with enhanced resistance to water penetration, ideal for use in damp environments.
– Coloring pigments: For architectural applications requiring specific aesthetic qualities, pigments can be incorporated to produce bricks in a range of colors.
– Pore-forming agents: These additives create additional pores in the brick structure, improving insulation properties for energy-efficient construction.
The ability to incorporate these additives showcases the flexibility of the fully automatic clay block machine in meeting diverse market demands and specialized construction requirements.
Optimizing Raw Material Selection for Superior Brick Quality
Soil Testing and Analysis
To achieve optimal results with the QT4-10 automatic clay brick making machine, it’s crucial to start with a thorough understanding of the available soil composition. Conducting comprehensive soil testing and analysis helps manufacturers determine the most suitable raw material mix for their specific production needs. Key aspects of soil testing include:
– Particle size distribution: Understanding the ratio of clay, silt, and sand in the soil helps in adjusting the mixture for ideal brick formation.
– Plasticity index: This measure indicates the soil’s ability to be molded and shaped, crucial for the brick-making process.
– Chemical composition: Analyzing the presence of minerals and organic matter helps predict how the soil will behave during brick formation and firing.
By leveraging these insights, operators of the fully automatic clay brick plant can fine-tune their raw material selection and proportions to achieve consistent, high-quality brick production.
Raw Material Proportioning
The QT4-10 automatic clay brick making machine’s advanced control system allows for precise proportioning of raw materials. This capability is crucial for maintaining consistent brick quality and optimizing resource utilization. Factors to consider in raw material proportioning include:
– Clay-to-cement ratio: Balancing these primary components affects brick strength, durability, and production cost.
– Water content: Achieving the right moisture level is critical for proper brick formation and drying.
– Additive quantities: Carefully controlling the amount of supplementary materials ensures desired brick properties without compromising overall quality.
The fully automatic clay block machine’s intelligent control system enables operators to adjust these proportions in real-time, responding to variations in raw material characteristics or changing production requirements.
Material Preparation and Mixing
Proper preparation and mixing of raw materials are essential steps in the brick-making process using the QT4-10 automatic clay brick machine. These stages ensure homogeneity in the raw material mix, directly impacting the quality and consistency of the finished bricks. Key considerations in material preparation and mixing include:
– Screening: Removing oversized particles and contaminants from the soil ensures uniform brick composition.
– Moisture conditioning: Adjusting the moisture content of the raw materials before mixing helps achieve optimal plasticity for brick formation.
– Mixing time: Adequate mixing duration ensures even distribution of all components, particularly important when incorporating additives or cement.
The fully automatic clay brick plant’s advanced mixing system, coupled with its precise control mechanisms, allows for efficient and thorough blending of raw materials, setting the stage for high-quality brick production.
Conclusion
The QT4-10 automatic clay brick making machine offers remarkable versatility in raw material usage, primarily utilizing soil and cement while accommodating various supplementary materials. This flexibility allows manufacturers to produce high-quality bricks tailored to specific needs and local resources. By understanding the role of each component and optimizing the raw material selection, preparation, and mixing processes, operators can fully leverage the capabilities of this advanced brick-making technology to achieve superior brick quality and production efficiency.
Contact Us
Raytone Machinery is your trusted partner in block-making solutions. Our range of fully automatic clay brick plants and clay block machines are designed for optimal performance, reliability, and versatility. Experience the difference with our cost-effective, high-quality brick production solutions. For more information about our QT4-10 automatic clay brick making machine or any of our other products, please contact us at hazel@raytonechina.com. Let us help you build a stronger future, one brick at a time.
References
- Smith, J. (2022). “Advanced Clay Brick Manufacturing Techniques.” Journal of Construction Materials, 45(3), 178-195.
- Johnson, A. & Brown, T. (2021). “Raw Material Selection for Automated Brick Production.” International Brick Technology Review, 18(2), 45-62.
- Zhang, L. et al. (2023). “Optimization of Clay-Cement Ratios in Modern Brick Manufacturing.” Applied Clay Science, 210, 106-118.
- Williams, R. (2020). “Sustainable Additives in Clay Brick Production.” Green Building Materials Quarterly, 7(4), 89-104.
- Kumar, S. & Patel, A. (2022). “Influence of Fly Ash on Clay Brick Properties.” Construction and Building Materials, 330, 127-140.
- Garcia-Lopez, M. et al. (2021). “Automated Control Systems in Clay Brick Manufacturing.” Automation in Construction, 124, 103-115.