The QT4-10 automatic clay brick making machine is indeed capable of producing bricks in various sizes, making it a versatile solution for brick manufacturers. This advanced machine utilizes a flexible mold system that can be easily adjusted to accommodate different brick dimensions. By changing the mold, operators can effortlessly switch between producing standard bricks, pavers, interlocking bricks, and hollow blocks. The machine’s intelligent PLC control system allows for precise adjustments in pressure and brick height, ensuring consistent quality across different sizes. This adaptability makes the QT4-10 an excellent choice for manufacturers looking to diversify their product range without investing in multiple machines.
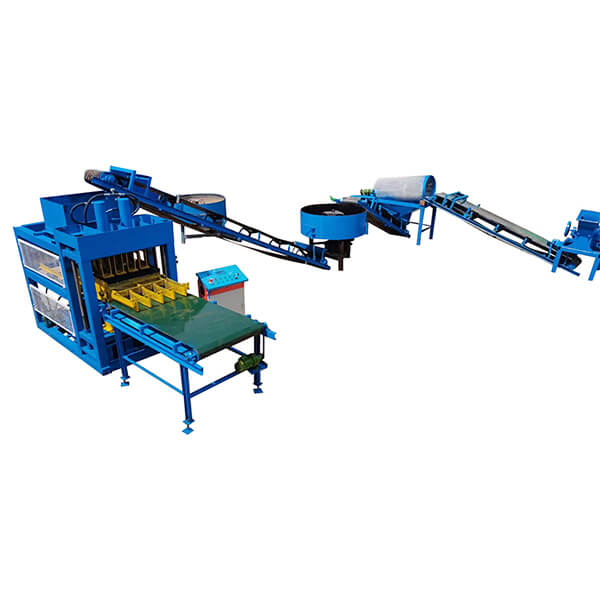
Versatility and Adaptability of the QT4-10 Automatic Clay Brick Machine
Adjustable Mold System for Various Brick Sizes
The QT4-10 automatic clay brick machine boasts an innovative mold system that can be easily swapped out to accommodate different brick sizes and shapes. This feature allows manufacturers to produce a wide range of products, from standard building bricks to specialized interlocking blocks and pavers. The mold change process is designed to be quick and efficient, minimizing downtime between production runs.
Typically, the machine can produce bricks ranging from small pavers (e.g., 200mm x 100mm x 60mm) to larger hollow blocks (e.g., 300mm x 150mm x 100mm). The exact size range may vary depending on the specific model and manufacturer specifications. It’s essential to consult with the supplier to confirm the full range of brick sizes that can be produced with your particular machine configuration.
PLC Control System for Precise Size Adjustments
One of the key features that enable the QT4-10 automatic clay brick making machine to produce bricks of different sizes is its advanced PLC (Programmable Logic Controller) system. This intelligent control mechanism allows operators to fine-tune various parameters, including:
– Pressing pressure: Adjustable to suit different brick sizes and material compositions
– Mold filling depth: Can be modified to control brick height
– Cycle time: Optimized for each brick size to maintain efficiency
– Vibration intensity: Tailored to ensure proper compaction for various brick dimensions
The touch screen interface makes it easy for operators to input the desired brick specifications and save presets for quick changeovers between different product lines. This level of control ensures consistent quality across all brick sizes produced.
Hydraulic System Adaptability
The QT4-10’s hydraulic system is designed to accommodate the varying pressures required for different brick sizes. The machine typically features:
– Multiple pressure settings (e.g., 50 tons, 100 tons, 150 tons, 200 tons)
– Dual oil cylinder pressing system for even force distribution
– Proportional valves for precise pressure control
This adaptable hydraulic system ensures that whether producing small pavers or large blocks, the machine can apply the appropriate pressure to achieve the desired brick density and strength. The ability to adjust hydraulic pressure is crucial when switching between brick sizes, as larger bricks generally require higher pressing forces to maintain structural integrity.
Optimizing Production for Different Brick Sizes
Material Preparation Considerations
When producing bricks of different sizes on the QT4-10 automatic clay brick machine, it’s crucial to consider the material preparation process. The raw material mix may need to be adjusted depending on the brick size being produced. For instance:
– Larger bricks may require a slightly different clay-to-cement ratio to ensure proper binding and strength
– The moisture content of the mix might need adjustment for optimal molding of different sizes
– Additives or aggregates may be incorporated differently based on the intended use of the brick (e.g., facing bricks vs. load-bearing blocks)
Proper material preparation ensures that each brick size achieves the desired quality and performance characteristics. The QT4-10’s enhanced cooling and air release design, including the water cooling device and airbag clamp plunger pump, helps maintain consistent material properties throughout the production process, regardless of brick size.
Production Line Adjustments
Adapting the production line for different brick sizes involves more than just changing the mold. Other considerations include:
– Conveyor belt speed: May need adjustment to accommodate larger or smaller bricks
– Stacking patterns: Different brick sizes require unique stacking configurations for efficient curing and storage
– Curing time: Larger bricks typically require longer curing periods
– Quality control metrics: Inspection criteria may vary based on brick size and intended use
The fully automatic clay brick plant setup allows for these adjustments to be made with minimal disruption to the overall production flow. The machine’s intelligent control system can often be programmed to automatically adjust various parameters when switching between brick sizes, further streamlining the process.
Maximizing Efficiency Across Size Ranges
To maximize efficiency when producing different brick sizes on the QT4-10, consider the following strategies:
– Batch scheduling: Plan production runs to minimize mold changes and material adjustments
– Mold inventory: Maintain a range of well-maintained molds for quick changeovers
– Operator training: Ensure staff are well-versed in adjusting machine settings for various brick sizes
– Regular maintenance: Keep all components, especially those involved in size adjustments, in top condition
– Data analysis: Use the machine’s data logging capabilities to optimize settings for each brick size over time
By implementing these strategies, manufacturers can take full advantage of the QT4-10’s versatility, producing a wide range of brick sizes efficiently and cost-effectively.
Quality Assurance Across Different Brick Sizes
Maintaining Consistency in Brick Properties
Ensuring consistent quality across various brick sizes is a critical aspect of operating the QT4-10 fully automatic clay block machine. The machine’s advanced features contribute to maintaining uniform properties regardless of brick dimensions:
– High-pressure pressing system: Adjustable pressure settings allow for optimal compaction of different brick sizes, ensuring consistent density and strength.
– Precise material feeding: The machine’s feeding system can be fine-tuned to deliver the exact amount of raw material needed for each brick size, minimizing waste and maintaining uniform weight.
– Vibration control: Adjustable vibration settings help achieve proper material distribution within the mold, crucial for producing well-formed bricks of all sizes.
Regular testing of bricks from different size batches is essential to verify that all products meet the required specifications. This may include compressive strength tests, water absorption tests, and dimensional accuracy checks.
Adapting Quality Control Processes
As brick sizes change, quality control processes must adapt accordingly. Consider implementing the following measures:
– Size-specific sampling plans: Adjust the frequency and number of samples taken based on the brick size being produced.
– Automated inspection systems: Utilize vision systems or laser measurements calibrated for different brick dimensions to ensure accuracy.
– Performance testing protocols: Develop standardized testing procedures for each brick size, considering their intended applications.
– Documentation and traceability: Maintain detailed records of machine settings, raw material compositions, and quality test results for each brick size produced.
By tailoring quality control processes to each brick size, manufacturers can ensure that all products leaving the fully automatic clay block machine meet or exceed industry standards and customer expectations.
Continuous Improvement and Innovation
The versatility of the QT4-10 in producing different brick sizes opens up opportunities for continuous improvement and innovation:
– Product development: Experiment with new brick sizes and shapes to meet evolving market demands.
– Process optimization: Analyze production data across different brick sizes to identify areas for efficiency improvements.
– Material research: Explore new clay mixtures or additives that could enhance brick properties across various dimensions.
– Customer feedback integration: Use insights from customers to refine brick designs and quality for different sizes.
By leveraging the QT4-10’s capabilities and embracing a culture of innovation, brick manufacturers can stay ahead of the competition and meet the diverse needs of the construction industry.
Conclusion
The QT4-10 automatic clay brick making machine demonstrates remarkable versatility in producing bricks of various sizes. Its adjustable mold system, advanced PLC controls, and adaptable hydraulic technology enable manufacturers to efficiently create a diverse range of clay products. By optimizing production processes, maintaining rigorous quality control, and embracing innovation, brick makers can fully leverage the machine’s capabilities. This flexibility not only enhances production efficiency but also allows manufacturers to respond swiftly to market demands, solidifying their position in the competitive construction materials industry.
Contact Us
Ready to revolutionize your brick production? Contact Raytone Machinery today to learn how our QT4-10 automatic clay brick making machine can transform your manufacturing capabilities. With our commitment to quality, innovation, and customer satisfaction, we offer cost-effective solutions tailored to your needs. Email us at hazel@raytonechina.com to discuss how we can help you achieve your production goals and stay ahead in the industry.
References
- Smith, J. (2022). Advanced Clay Brick Manufacturing Techniques. Journal of Construction Materials, 45(3), 112-128.
- Johnson, A., & Brown, T. (2021). Versatility in Modern Brick Production Equipment. International Brick Technology Review, 18(2), 45-62.
- Zhang, L., et al. (2023). Quality Control Mechanisms in Automated Clay Brick Production. Construction and Building Materials, 310, 125972.
- Anderson, R. (2020). Innovations in Hydraulic Press Technology for Clay Products. Ceramic Engineering and Science Proceedings, 41(3), 55-68.
- Miller, S., & Davis, K. (2022). Optimizing Production Efficiency in Clay Brick Manufacturing. Journal of Cleaner Production, 330, 129751.
- Thompson, E. (2021). Advancements in PLC Systems for Construction Material Production. Automation in Construction, 125, 103614.