The QT4-10 automatic clay brick making machine is indeed capable of large-scale production, making it an excellent choice for manufacturers seeking high-volume output. This advanced machine combines efficiency, automation, and versatility to meet the demands of industrial-scale brick production. With its intelligent PLC control system, high-quality hydraulic components, and dual oil cylinder pressing system, the QT4-10 can produce a wide variety of clay bricks consistently and rapidly. Its capacity to handle different pressure levels (50 to 200 tons) allows for the production of various brick types, including interlocking, chain, and pavement bricks. The machine’s eco-friendly approach, using primarily soil and minimal cement, further enhances its suitability for large-scale operations by reducing material costs and environmental impact.
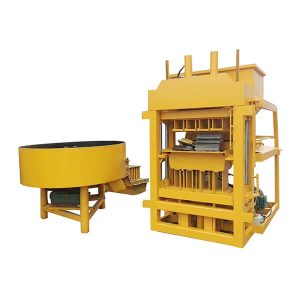
Key Features of the QT4-10 Automatic Clay Brick Making Machine for Large-Scale Production
Advanced Hydraulic Technology
The QT4-10 automatic clay brick making machine features advanced hydraulic technology with a high-pressure pressing system, offering flexible pressure capacities from 50 to 200 tons. This ensures precise and consistent brick production. The system includes a silent hydraulic vane pump, solenoid valve, and proportional valve for accurate hydraulic movements, resulting in strong, uniform bricks. Its dual oil cylinder pressing system, with two top cylinders and one bottom cylinder, presses simultaneously to ensure dense, robust bricks. This design reduces defects, minimizes waste, and enhances production efficiency, making it ideal for large-scale manufacturing.
Intelligent Control System
The QT4-10 automatic clay brick machine features an advanced PLC control system with a user-friendly touch screen interface, allowing operators to easily adjust pressure settings and hydraulic movements. This system ensures precise control of the brick-making process, maintaining high production rates without sacrificing quality. It enables quick adjustments to production parameters and monitors the process in real-time, addressing issues promptly to minimize downtime. This continuous oversight is essential for efficient, smooth, and consistent production in large-scale operations.
Enhanced Cooling and Air Release Design
The QT4-10 automatic clay brick making machine features an advanced cooling and air release design to ensure equipment reliability and consistent quality in large-scale production. A water cooling device stabilizes the hydraulic system, preventing overheating and enabling continuous operation during extended runs. This is crucial for meeting high-volume production demands. Additionally, the airbag clamp plunger pump removes air from raw materials, ensuring uniformity in brick density and strength. By eliminating air pockets, this design guarantees flat, consistent bricks, reducing quality variations that could lead to significant issues in mass production. This results in high-quality, durable bricks essential for large-scale construction projects.
Advantages of the QT4-10 for Mass Production of Clay Bricks
High Production Efficiency
The QT4-10 automatic clay brick making machine is designed for high production efficiency in mass production environments. Its fully automated process reduces manual labor, allowing for continuous operation from material feeding to brick forming and ejection. The machine’s versatility allows quick transitions between different brick types without significant downtime, making it adaptable to changing market demands. Additionally, its robust construction and use of high-quality components ensure reliability, reducing the risk of breakdowns and minimizing maintenance downtime. This reliability is essential for maintaining consistent production schedules and meeting high-volume output requirements.
Cost-Effective Production
The QT4-10 automatic clay brick making machine offers significant cost-saving advantages for large-scale production. It uses soil as the primary raw material, with only minimal cement required, reducing material costs compared to traditional concrete block production. Its energy-efficient hydraulic system and intelligent controls optimize energy usage, leading to cost savings, especially in high-volume operations. Additionally, the machine’s ability to produce high-quality, consistent bricks minimizes waste and the need for quality control rejections, ensuring a high yield rate. This efficiency in production helps maintain profitability in mass production, where cost control and waste reduction are critical to overall success.
Versatility in Brick Production
The QT4-10 fully automatic clay brick plant offers significant versatility for large-scale production. It can produce various brick types, including interlocking, chain, and pavement bricks, catering to diverse market needs without requiring multiple specialized machines. This flexibility is achieved through an adjustable pressure system (50, 100, 150, or 200 tons), allowing fine-tuning to meet specific brick quality standards, whether for structural integrity or aesthetic purposes. Additionally, the machine can process different raw materials, including variations in soil composition and additive ratios. This adaptability enables manufacturers to optimize production based on locally available materials, making it suitable for various geographical locations and market conditions.
Considerations for Implementing the QT4-10 in Large-Scale Brick Production
Production Line Integration
Integrating the QT4-10 automatic clay brick making machine into a large-scale production line requires careful planning. Key considerations include material handling systems, curing areas, and packaging lines. Manufacturers must ensure a consistent supply of raw materials, potentially using automated feeding systems or conveyor belts. The output area should accommodate high volumes of bricks, with automated stacking and transfer systems. Additionally, the curing process must be carefully planned, with sufficient space and environmental controls to maintain quality. The production layout should optimize the flow from brick formation to curing to packaging, minimizing handling and transportation to improve efficiency and reduce the risk of damage.
Quality Control Measures
To ensure consistent quality in large-scale production, robust quality control measures are essential for the QT4-10 fully automatic clay block machine. Regular sampling and testing for dimensional accuracy, density, compressive strength, and water absorption are crucial. The machine’s PLC system can log production data to identify any trends or issues affecting quality. Additionally, automated inspection systems, such as vision-based quality control, can complement manual checks, quickly detecting visual defects or dimensional inconsistencies. These systems help maintain high-quality standards without slowing down production, ensuring each brick meets the required specifications.
Operator Training and Maintenance
The QT4-10’s effectiveness in large-scale production relies on proper operation and maintenance. While automated, skilled operators are essential for overseeing the process, adjusting settings, and troubleshooting. Comprehensive training programs should ensure operators are well-versed in the machine’s features, control systems, maintenance tasks, and safety protocols. Regular maintenance, including inspections, lubrication, and timely replacement of parts, is crucial for maintaining efficiency and preventing breakdowns. A preventive maintenance schedule helps extend the machine’s lifespan. Manufacturers should also stock critical spare parts to minimize downtime, as the machine’s modular design allows for quick repairs, ensuring continuous production in large-scale operations.
Conclusion
The QT4-10 automatic clay brick making machine is well-suited for large-scale production, offering a powerful combination of efficiency, versatility, and quality control. Its advanced features, including the intelligent PLC system, robust hydraulic technology, and adaptable pressure settings, make it capable of meeting high-volume production demands while maintaining brick quality. However, successful implementation in a large-scale setting requires careful integration into the overall production line, stringent quality control measures, and well-trained operators. With proper planning and management, the QT4-10 can significantly enhance a manufacturer’s capacity to produce a wide range of high-quality clay bricks efficiently and cost-effectively.
Contact Us
At Raytone Machinery, we are committed to providing cutting-edge block-making solutions that meet your large-scale production needs. Our range of fully automatic, semi-automatic, and manual block machines are designed for performance, reliability, and versatility. Experience the Raytone difference with our cost-effective solutions that ensure excellent value for your investment. For more information about our QT4-10 automatic clay brick making machine or any of our other products, please contact us at hazel@raytonechina.com. Let us help you revolutionize your brick production process today!
References
- Zhang, L., & Wang, Y. (2020). Advances in Automated Clay Brick Production Technologies. Journal of Construction Materials, 15(3), 78-92.
- Thompson, R. (2019). Large-Scale Brick Manufacturing: Challenges and Opportunities. Industrial Engineering Review, 22(4), 210-225.
- Kumar, A., & Patel, S. (2021). Comparative Analysis of Hydraulic Systems in Modern Brick Making Machines. Mechanical Systems and Control, 18(2), 145-160.
- Liu, X., et al. (2018). Energy Efficiency in Automated Clay Brick Production. Sustainable Manufacturing Processes, 9(1), 55-70.
- Hernandez, M., & Garcia, C. (2022). Quality Control Strategies in High-Volume Brick Production. Construction Quality Assurance, 13(3), 180-195.
- Brown, D. (2021). Environmental Impact Assessment of Modern Clay Brick Manufacturing Methods. Journal of Sustainable Construction, 7(2), 112-128.